Medical Device Manufacturing
The Crescent team manages the entire process for you!
For over half a century, Crescent Industries has been leading the charge in providing top-tier medical injection molding solutions to the ever-evolving medical, pharmaceutical, and dental industries. Starting with diagnostic well plates, we've expanded our expertise to include Class I, II, and III medical devices and components, utilizing a wide range of medical-grade resins.
Our state-of-the-art machines, automated quality inspection equipment, and scientifically-backed molding processes guarantee that YOU can rely on our services with confidence. And if that wasn't enough, we offer ISO 7 cleanroom molding, assembly, and packaging services to provide you with a complete solution for your medical products.
With complete quality control and inspection, including IQ, OQ, PQ validations, and lot traceability, we uphold the critical medical quality standards required for plastic injection molding medical parts. Trust us to bring your medical device projects to life!
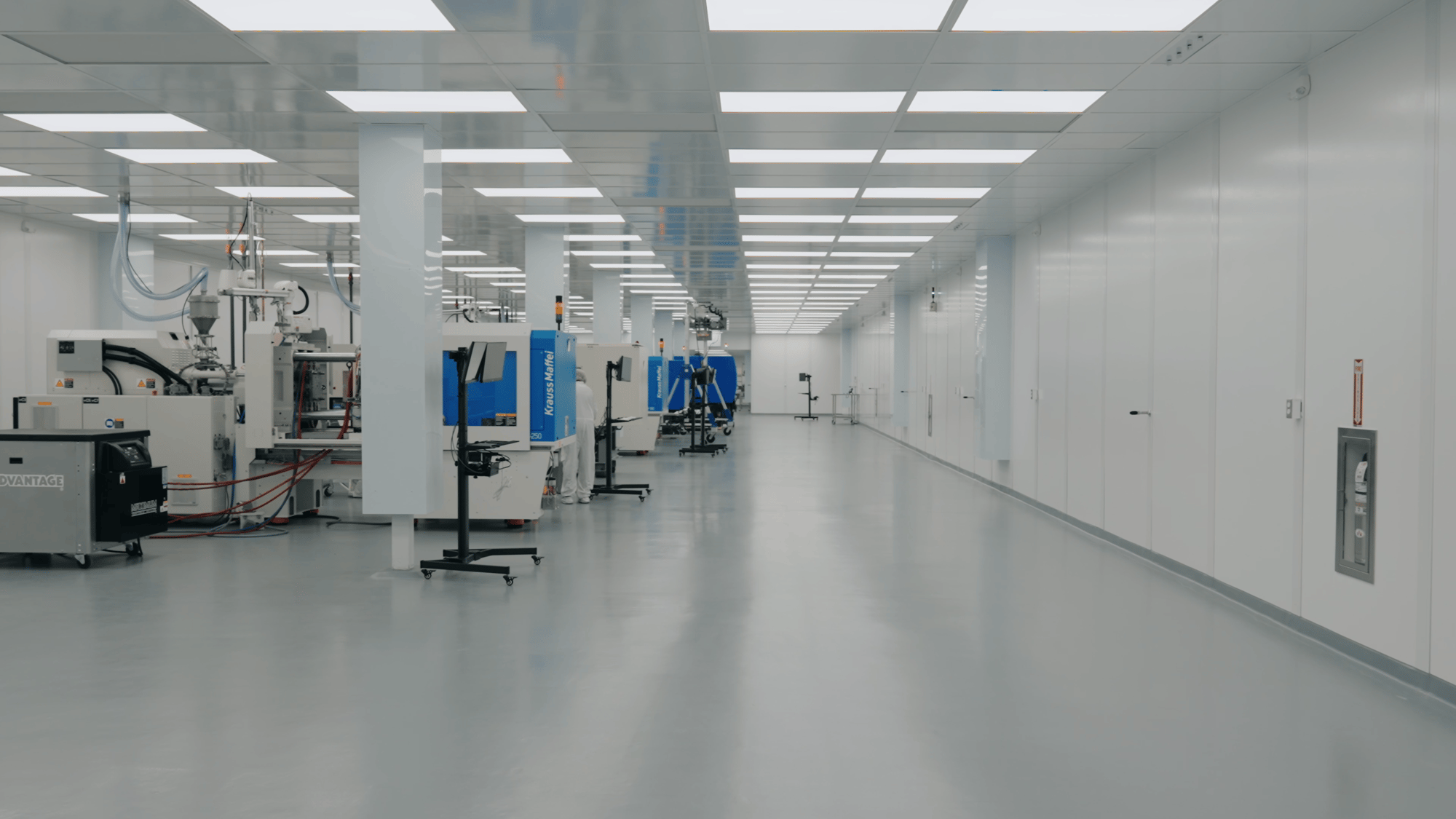
Medical Device Injection Molding Samples & Experience
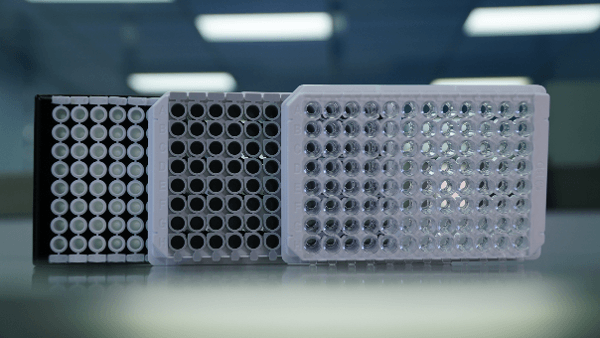
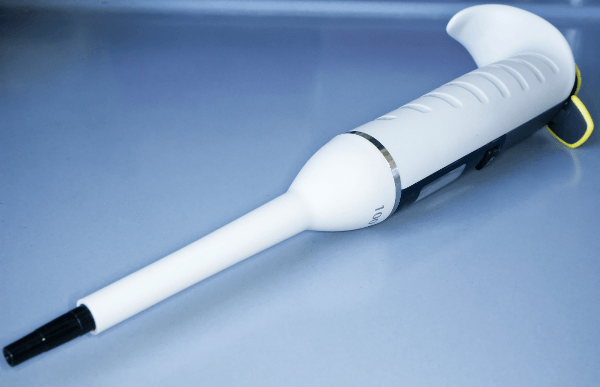
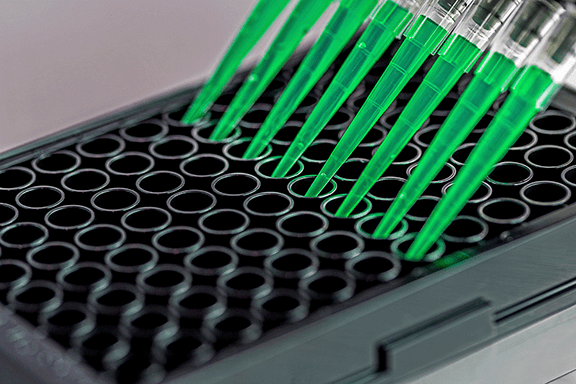
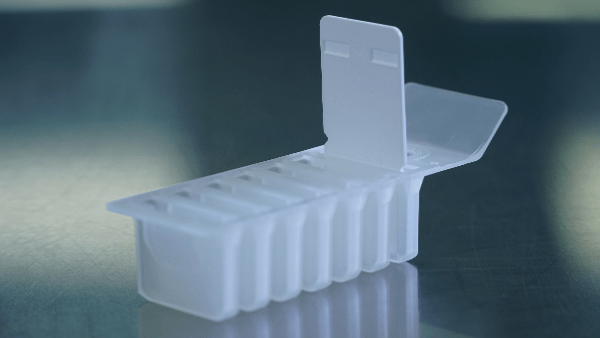
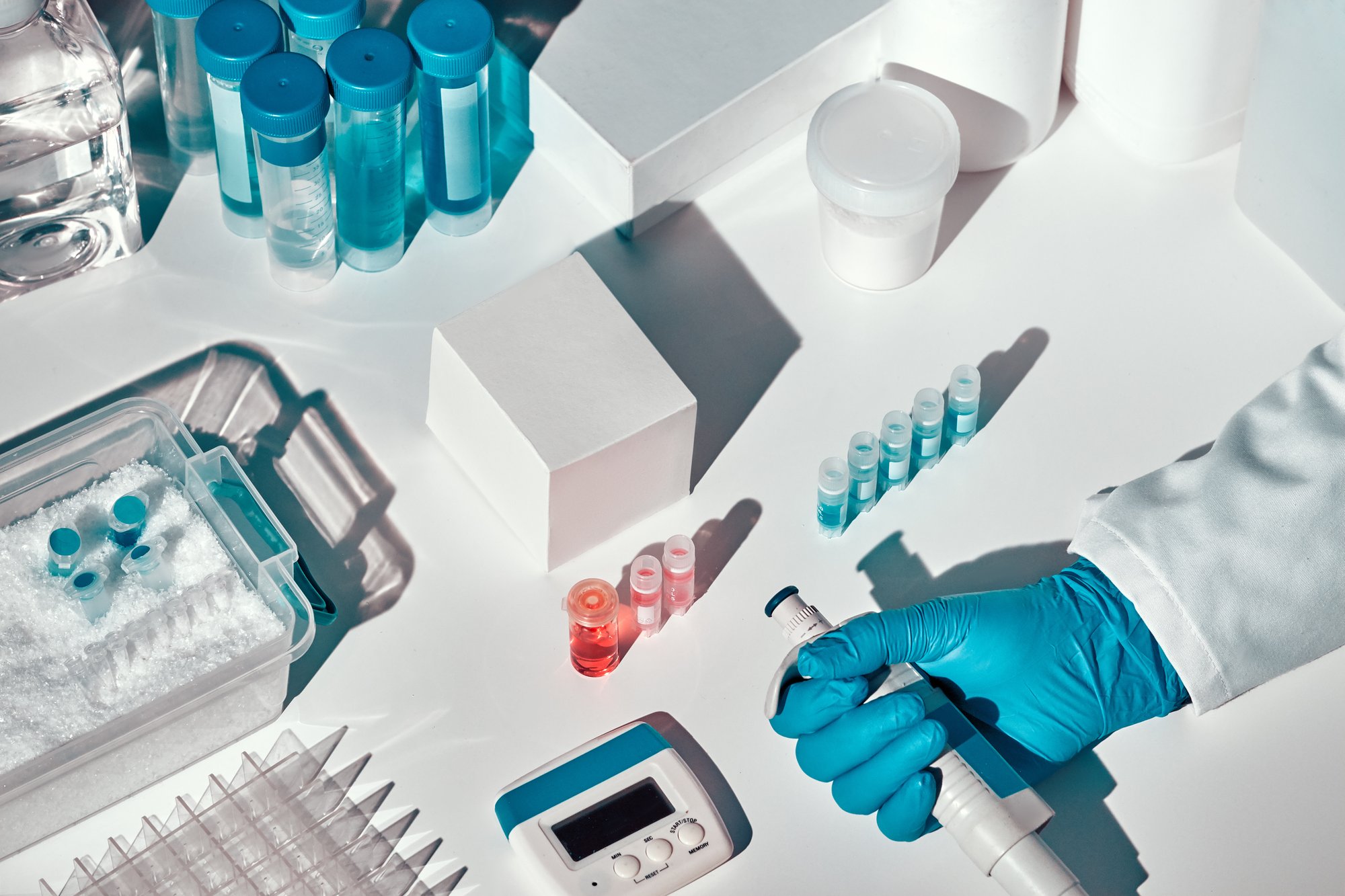
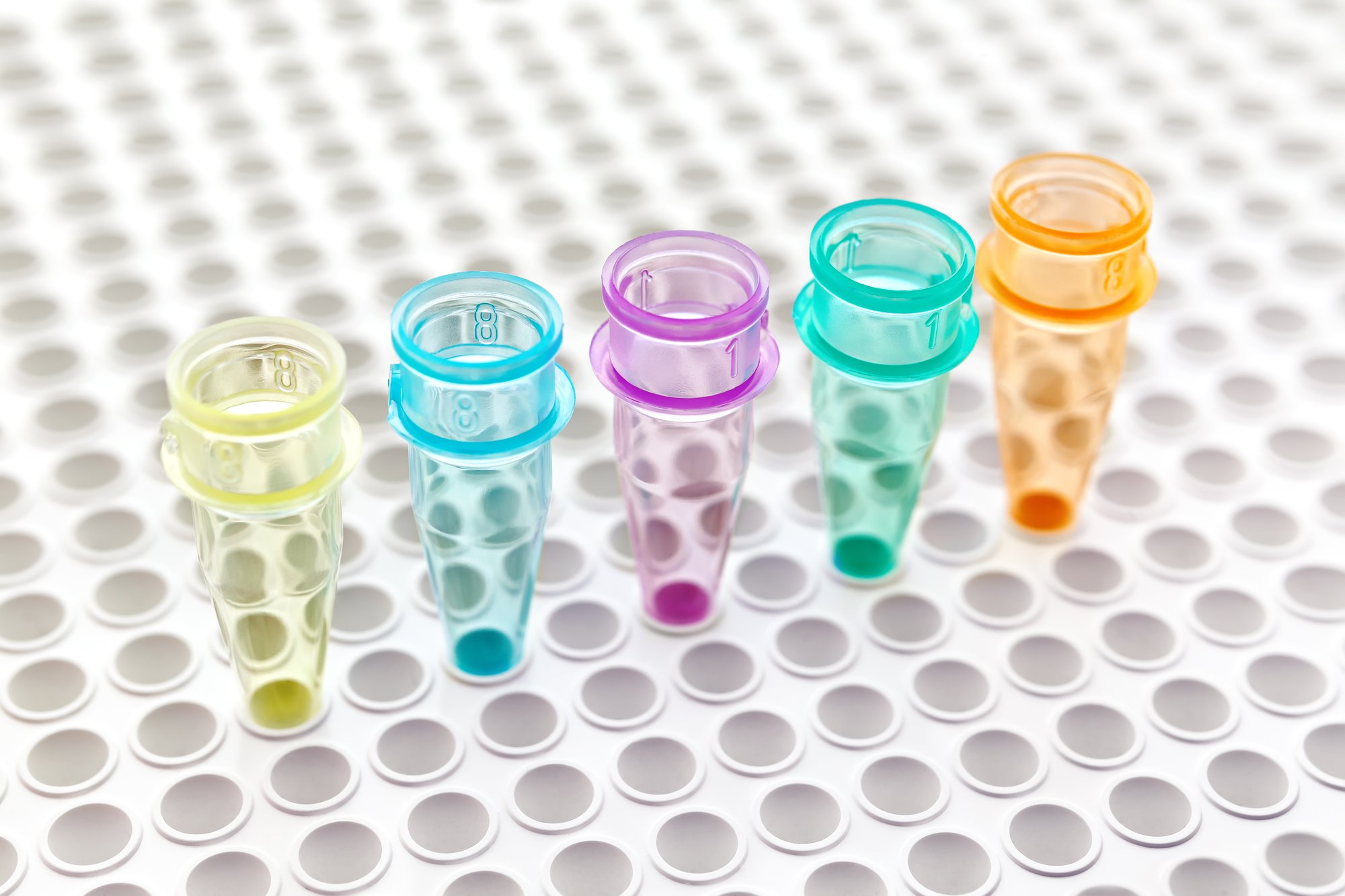
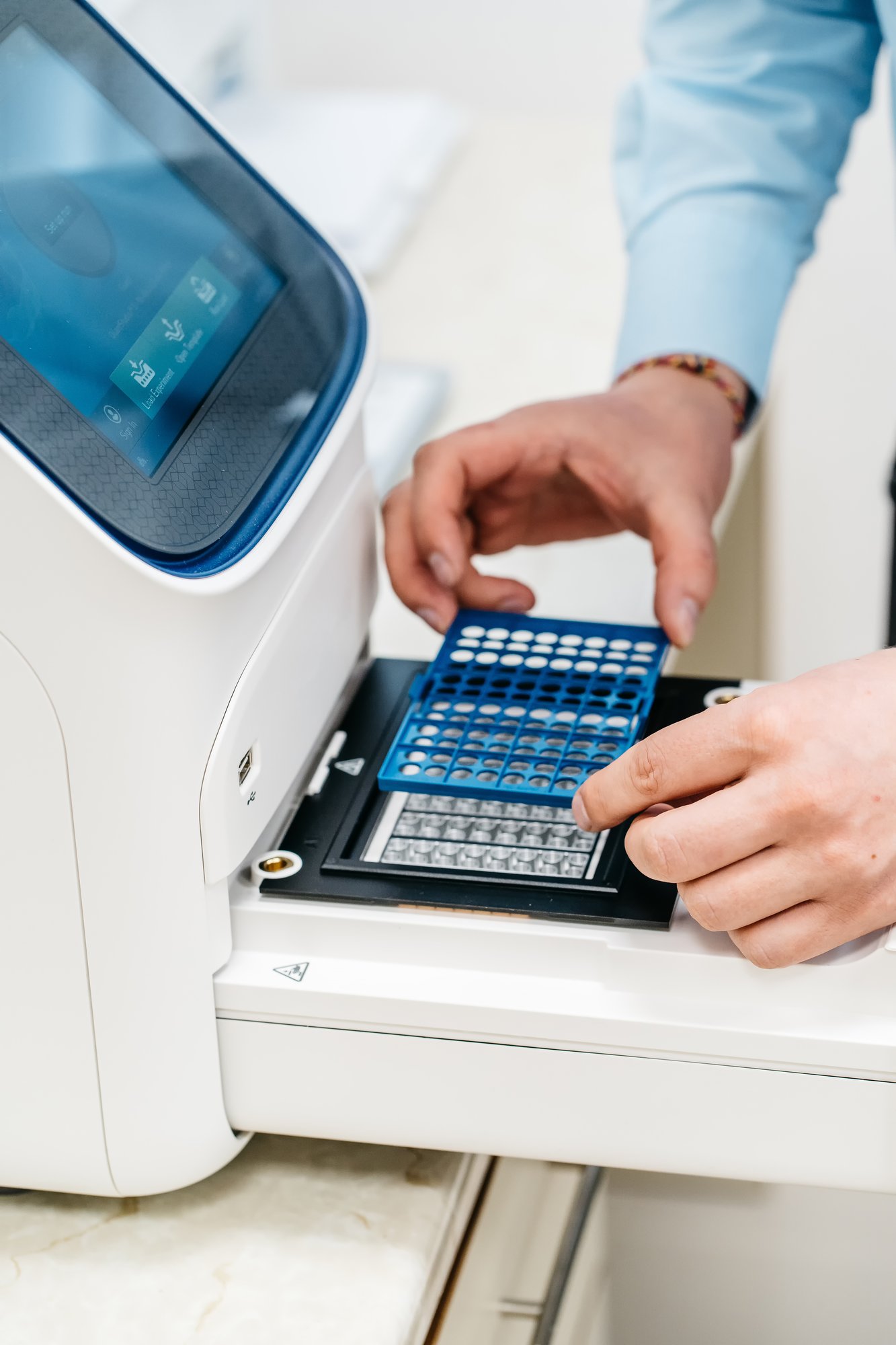
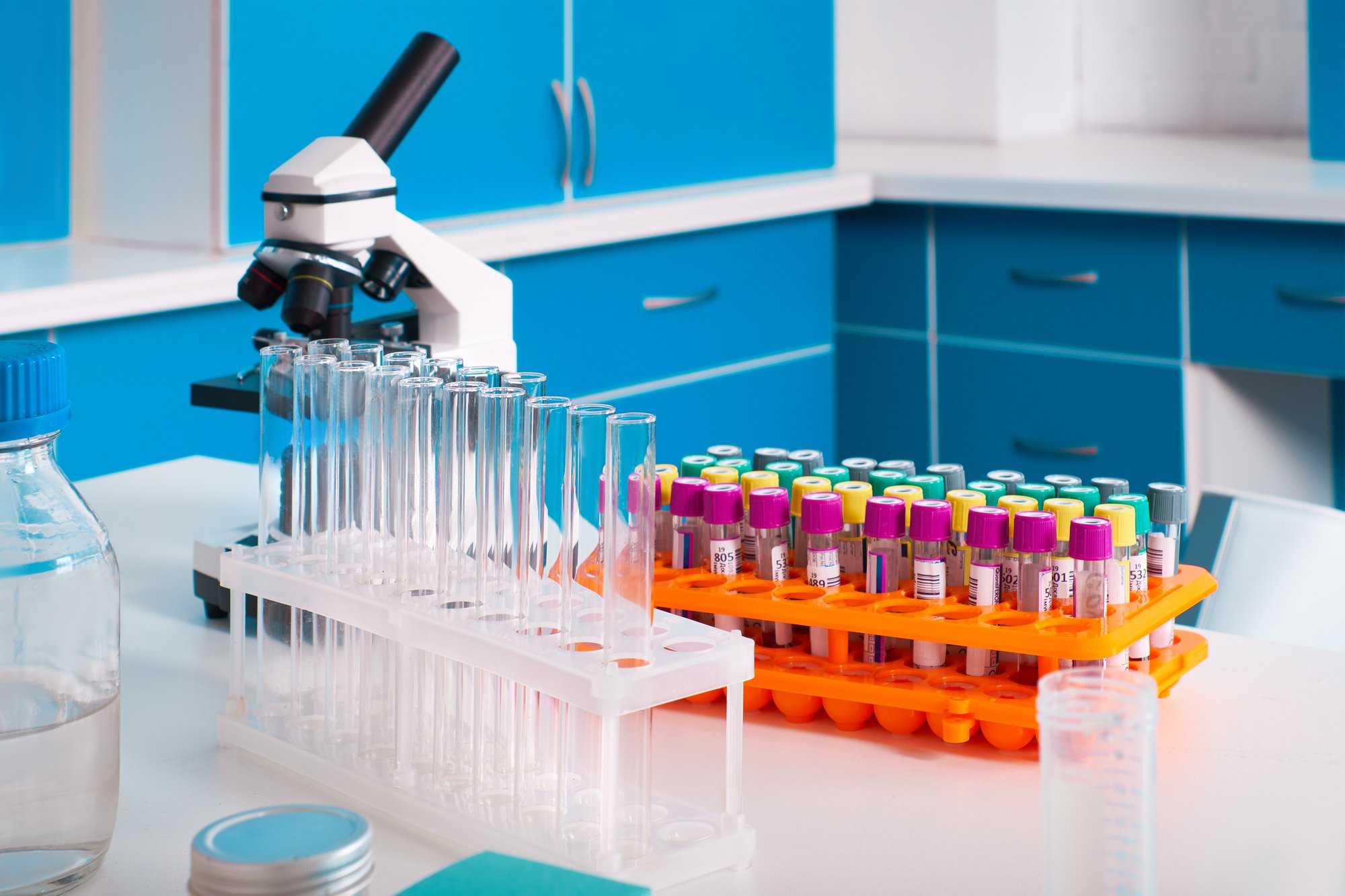
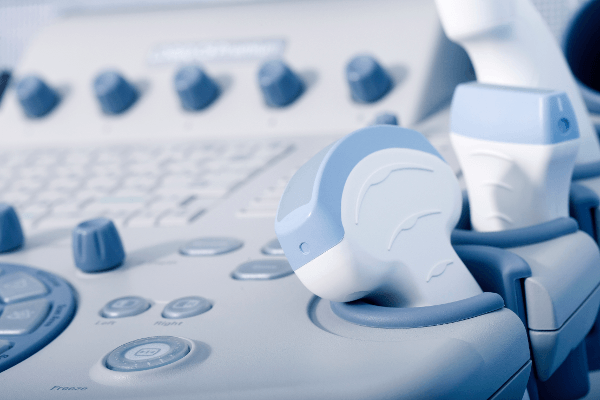
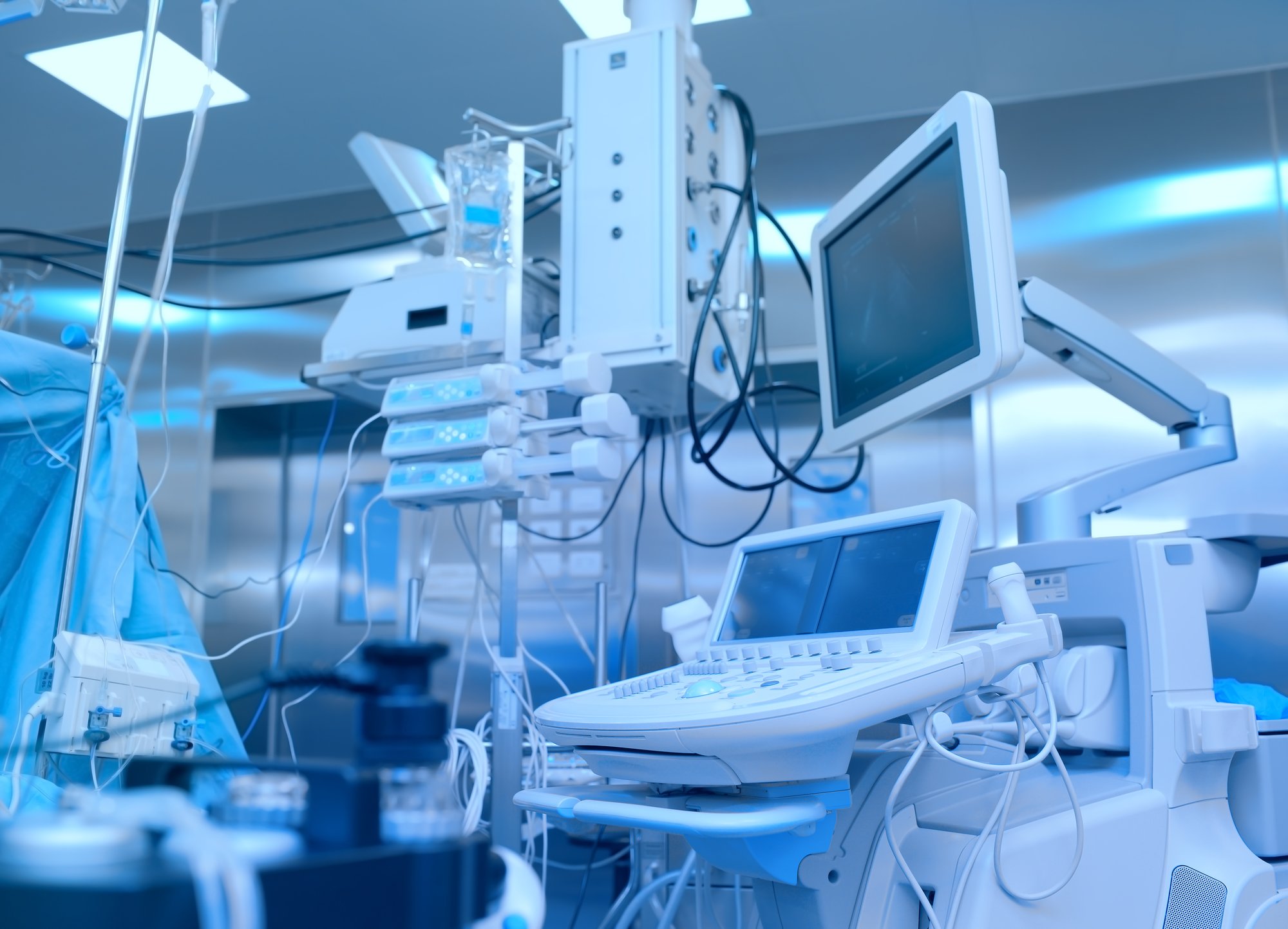
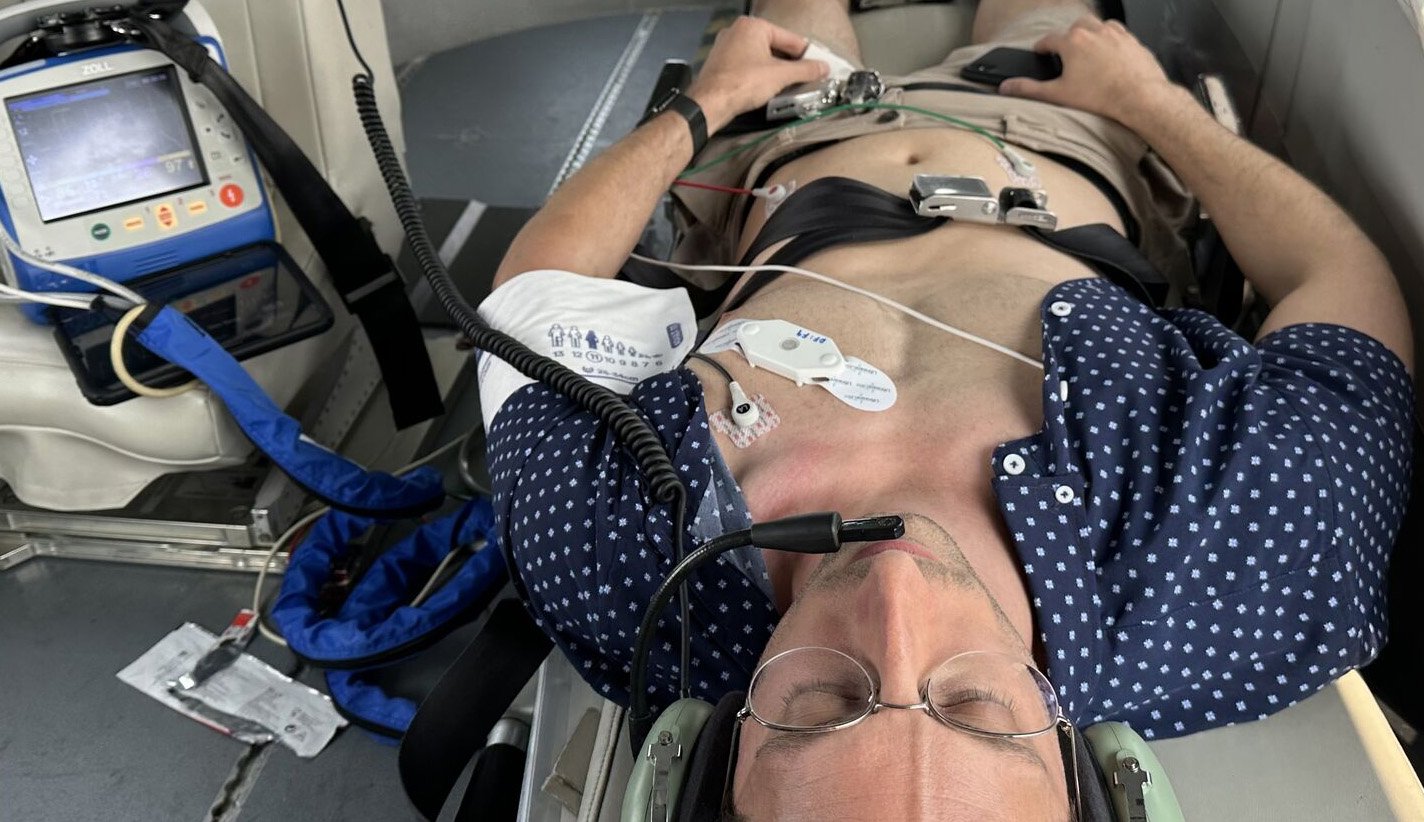
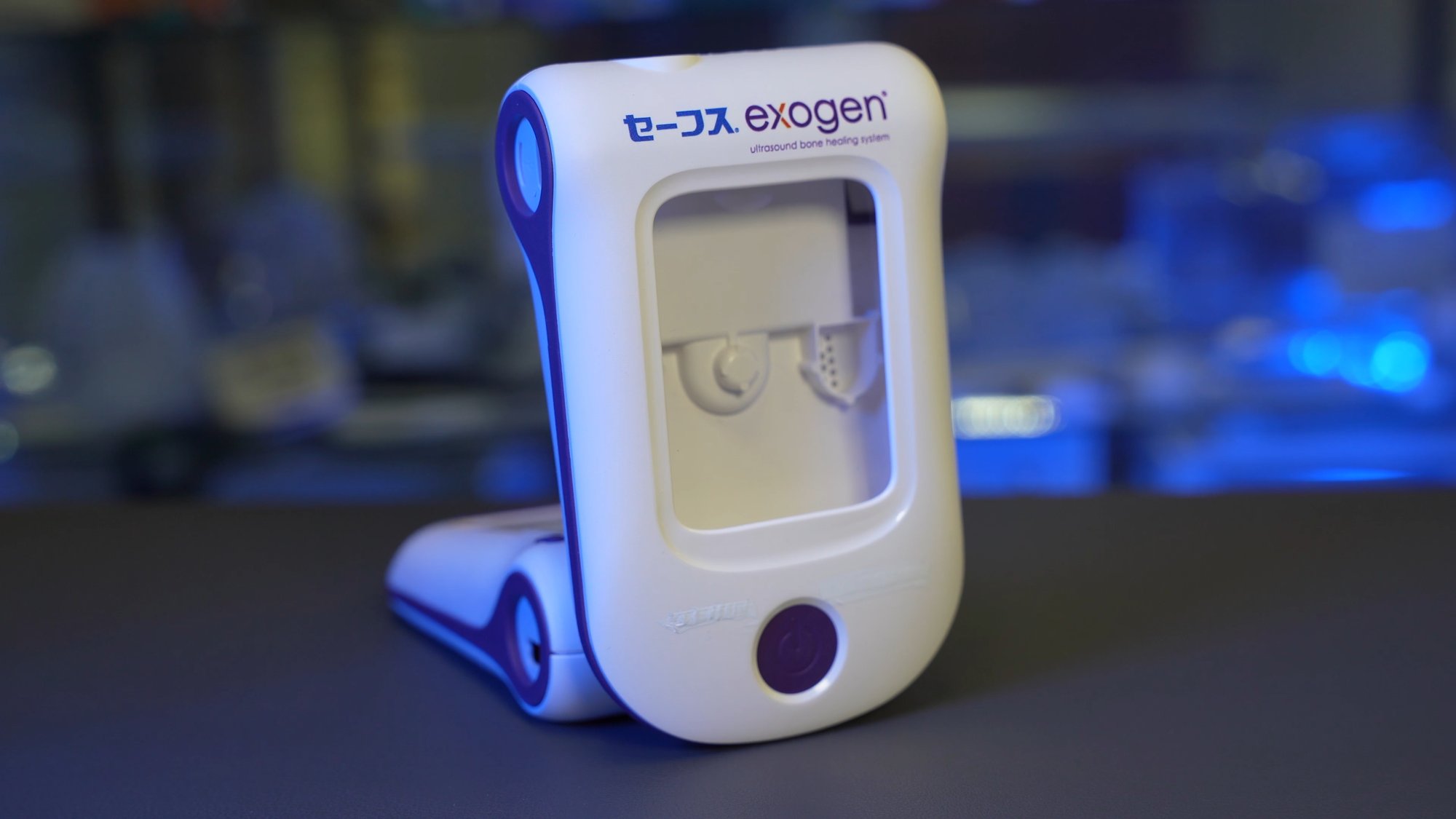
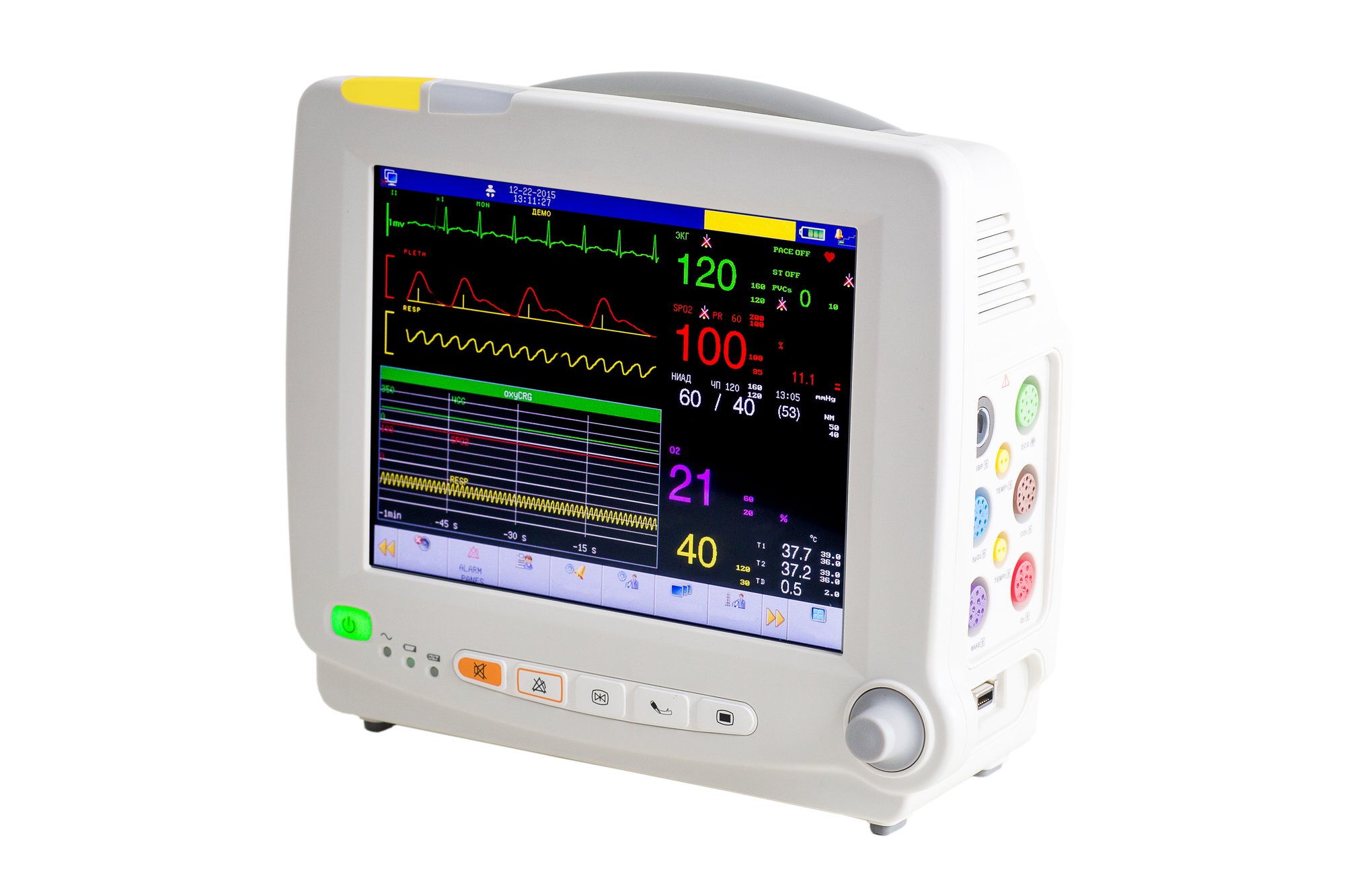
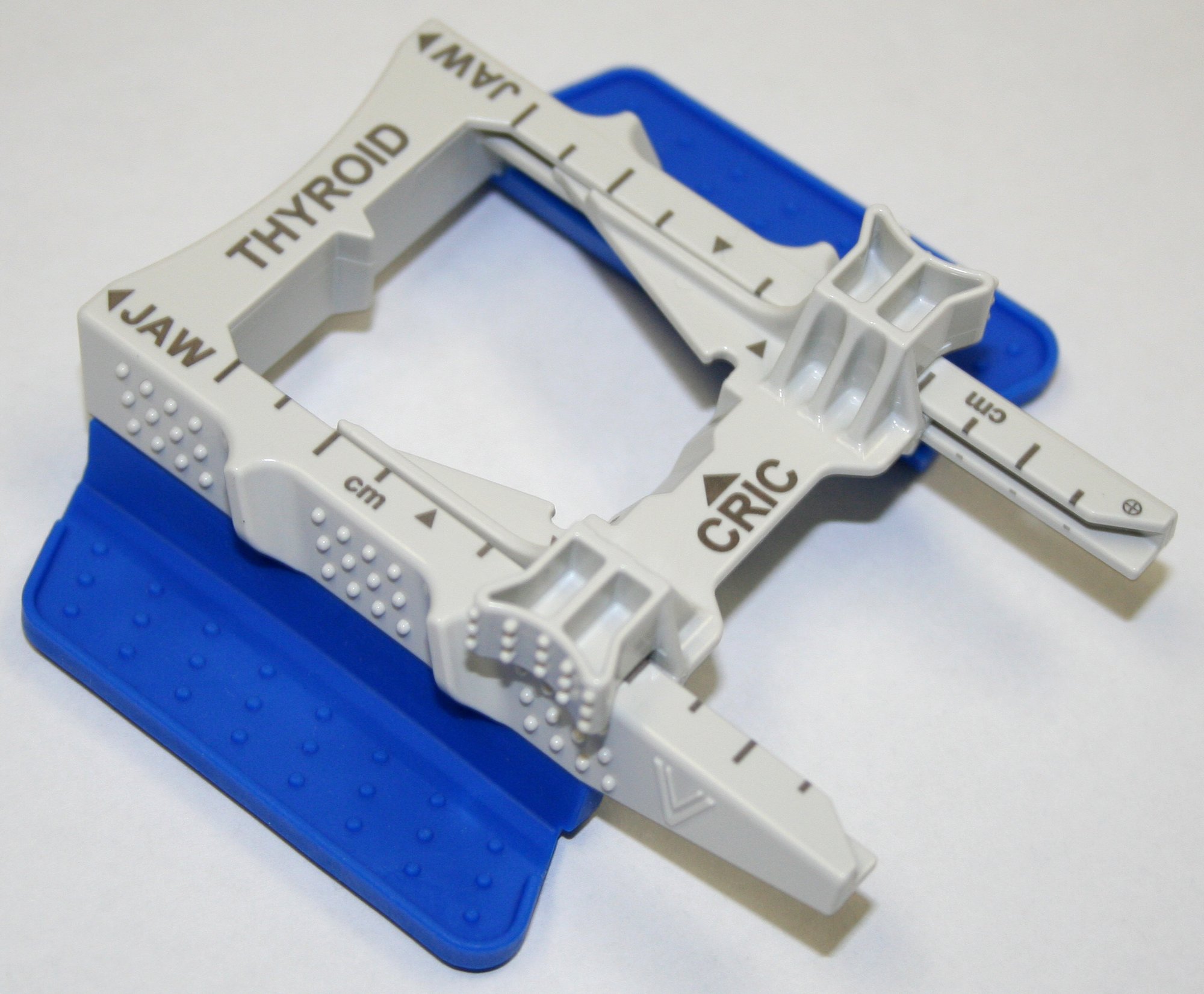
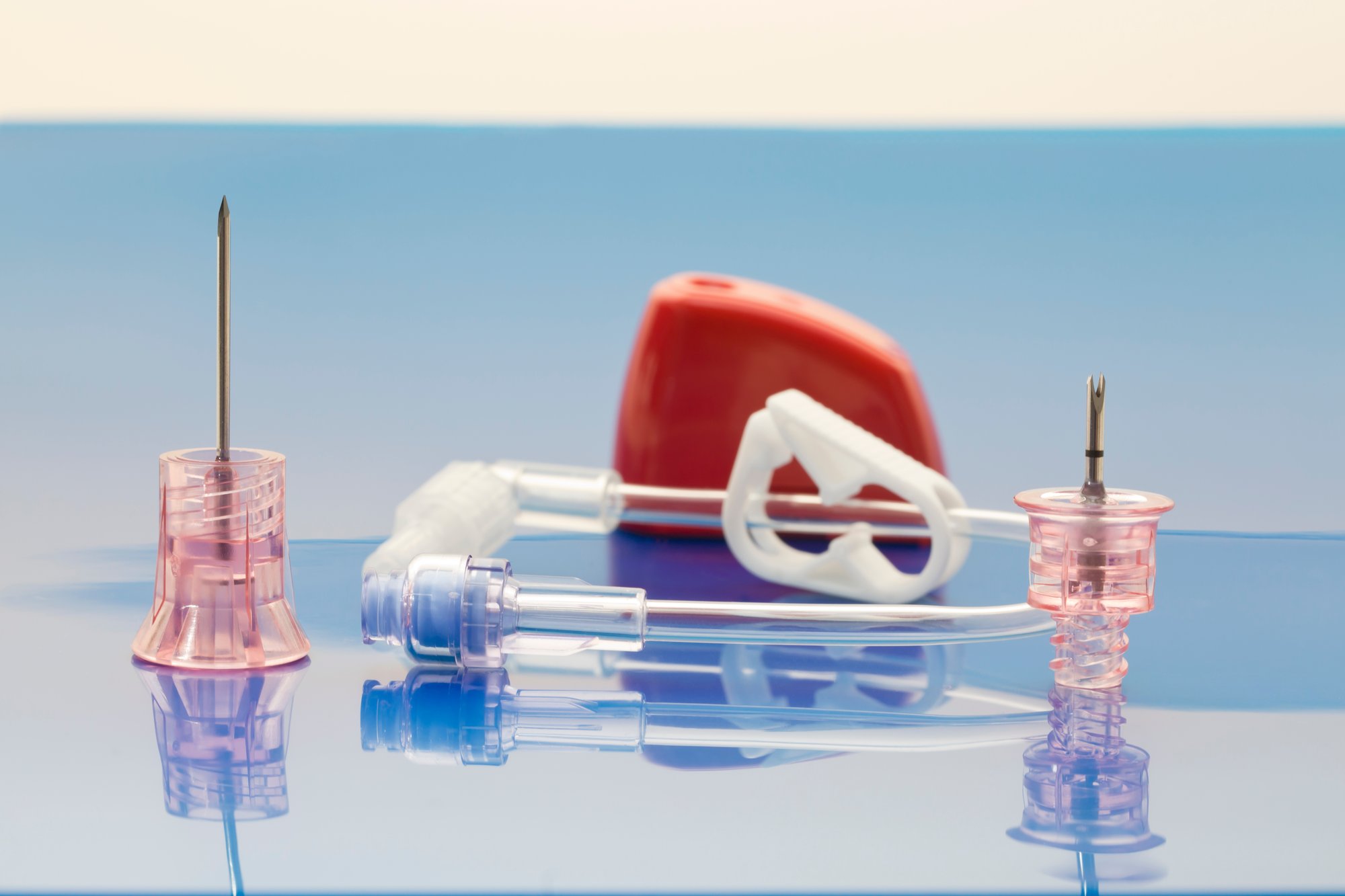
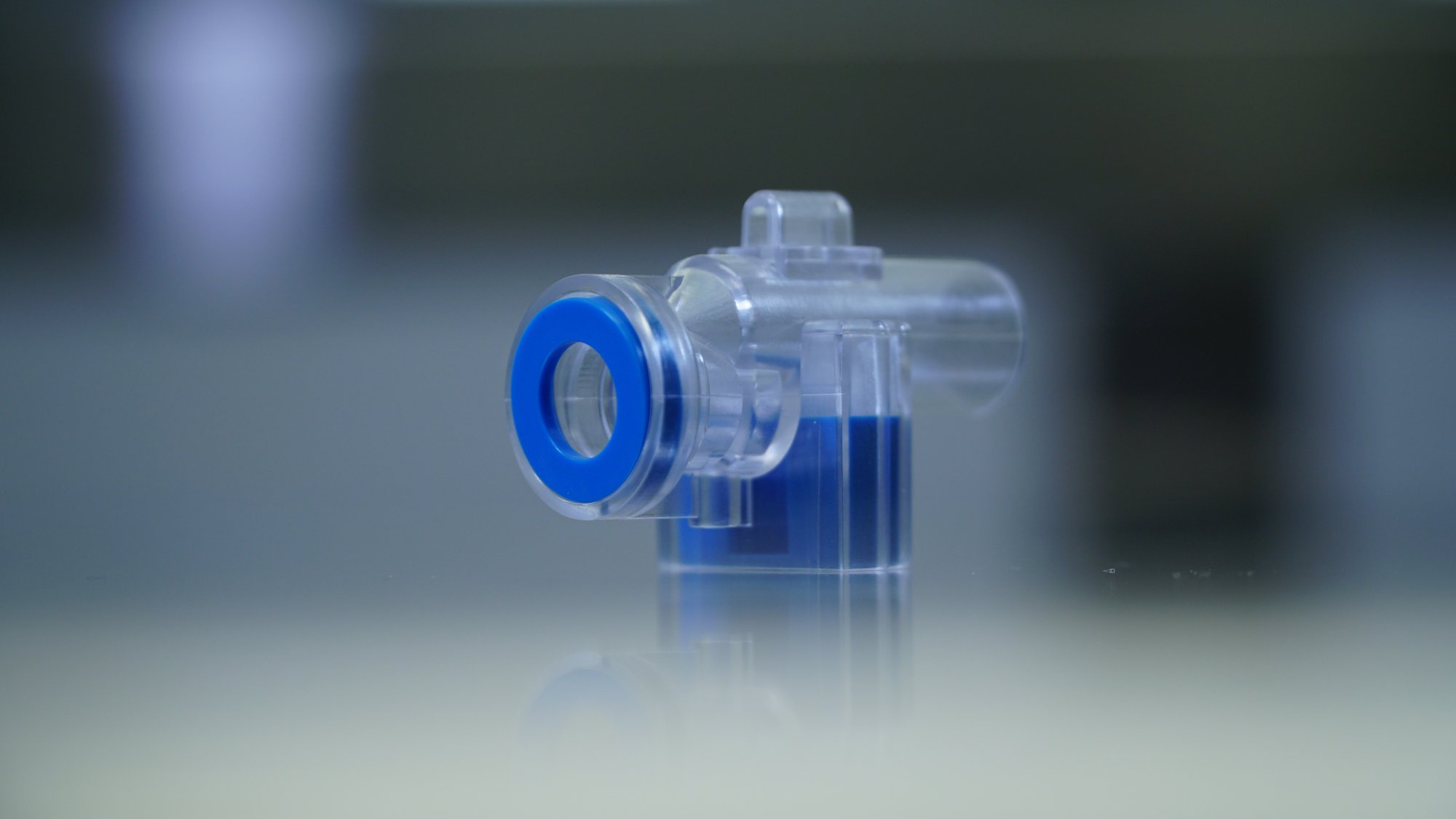
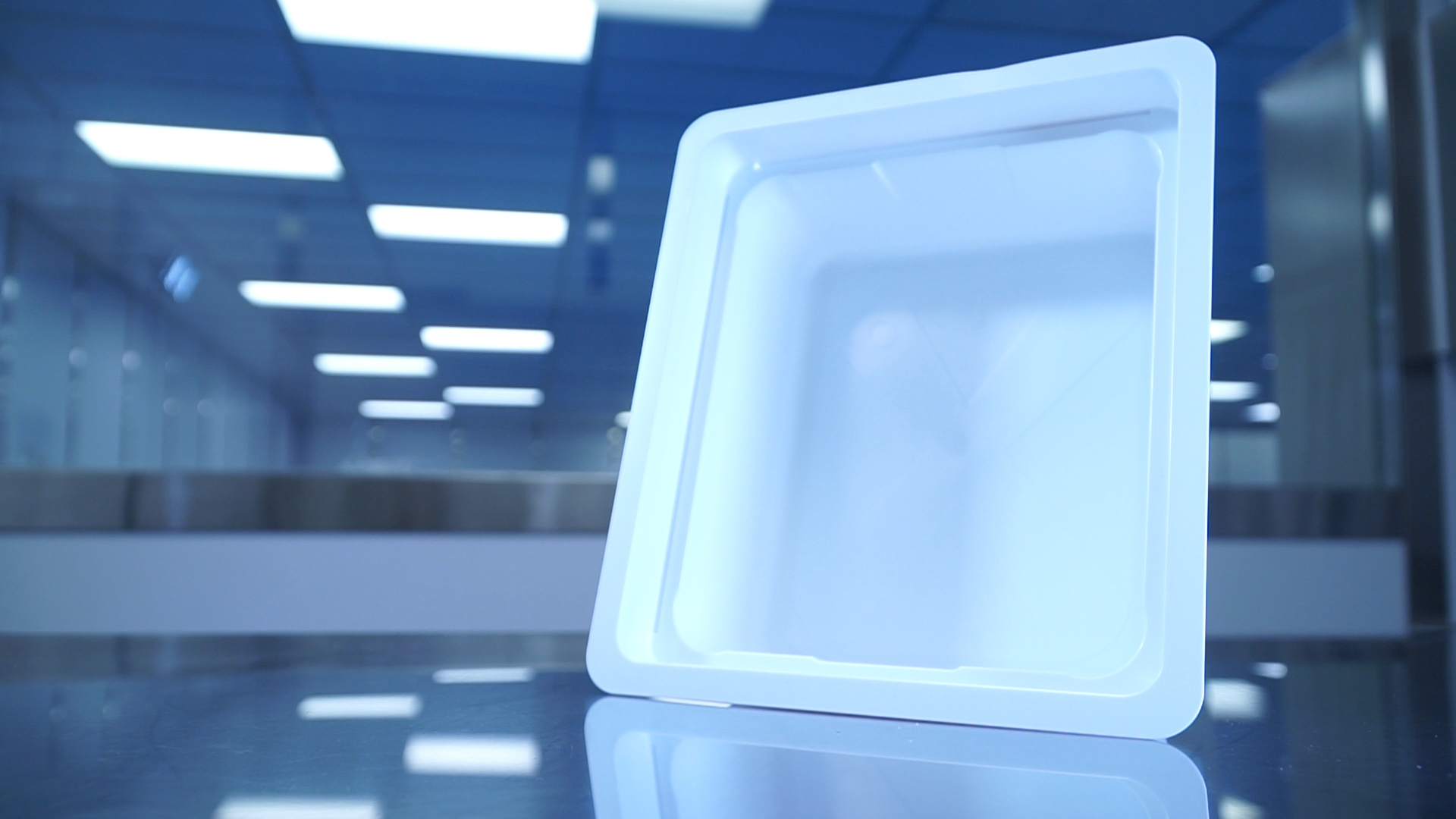
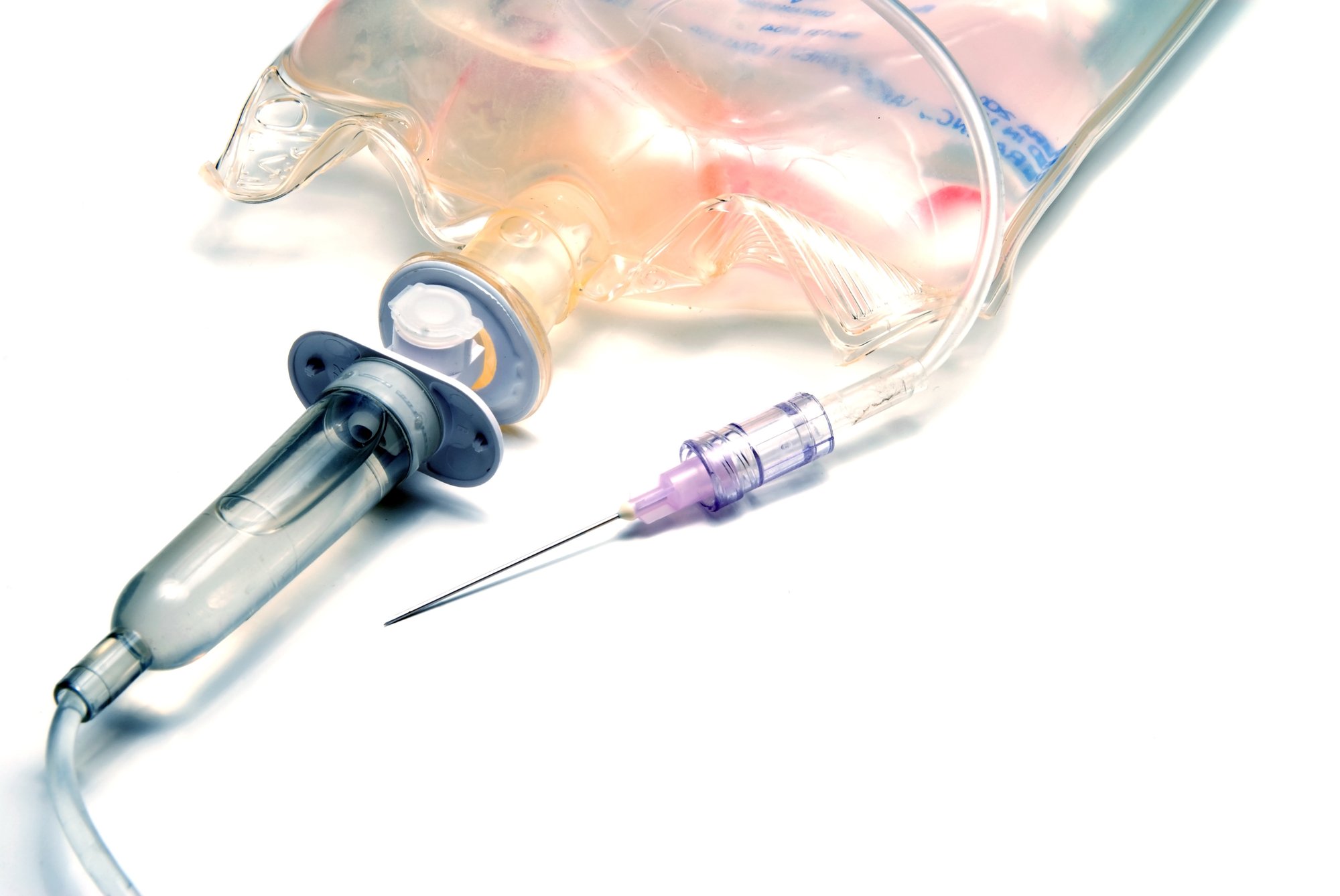
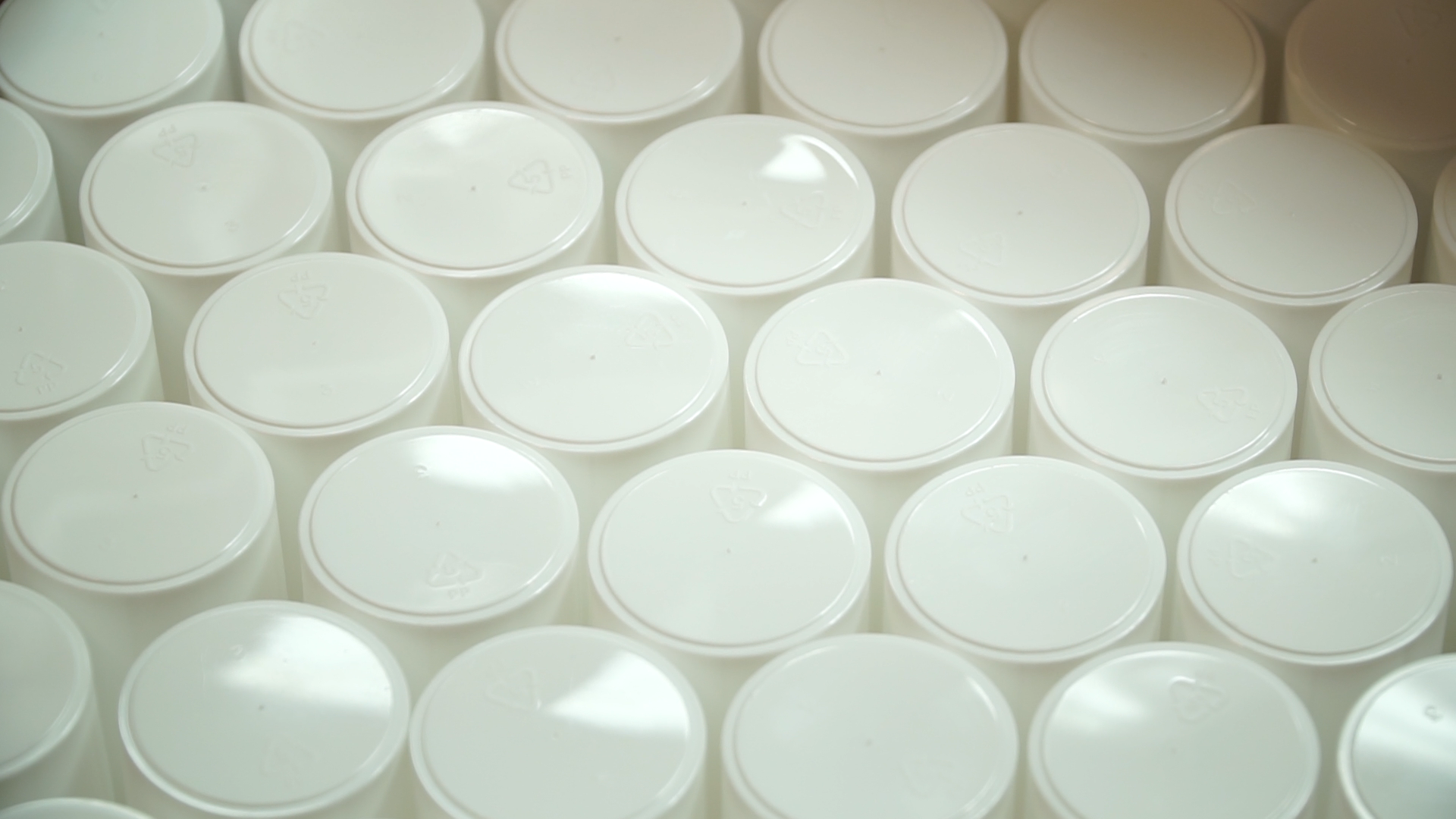
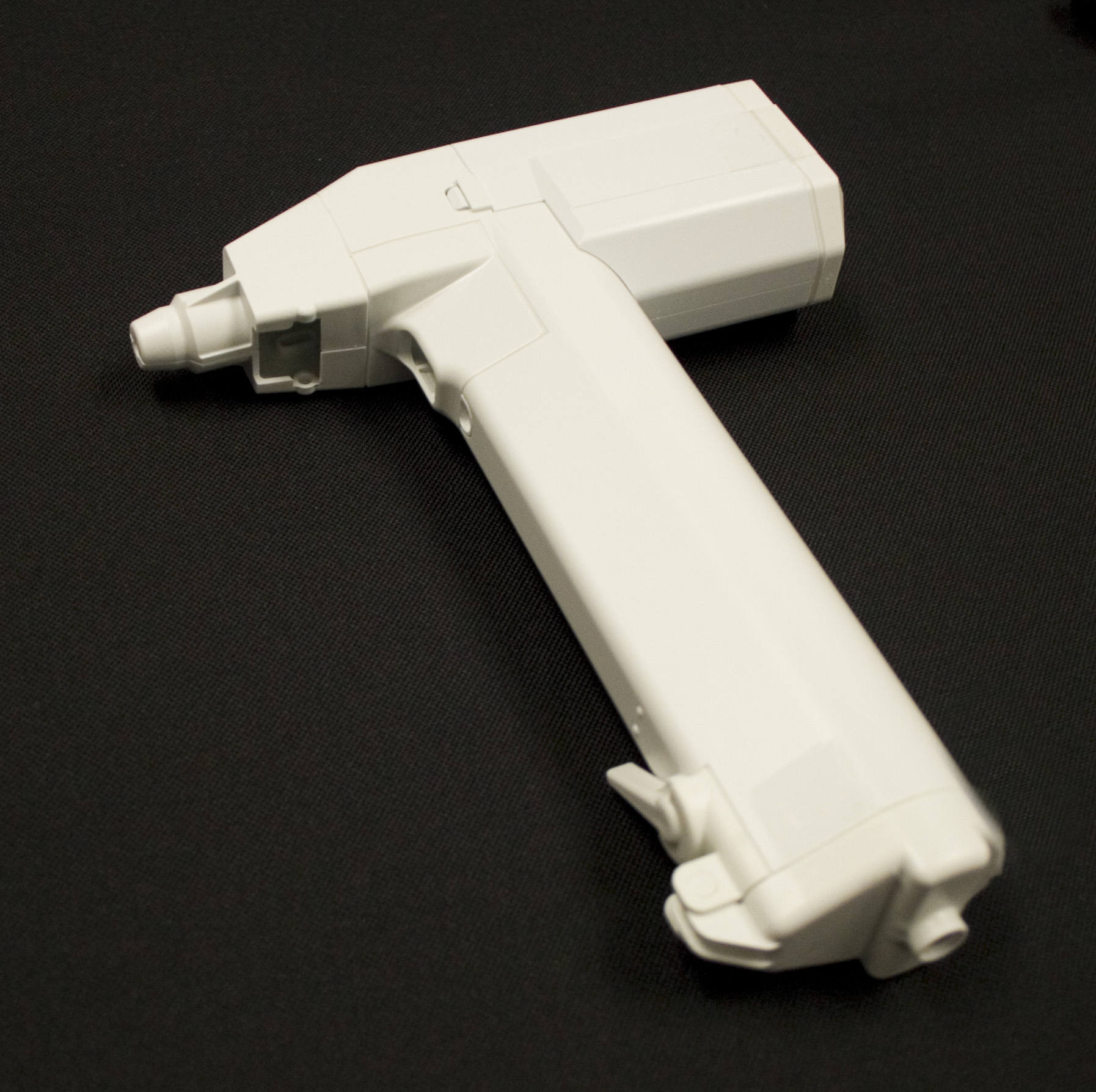
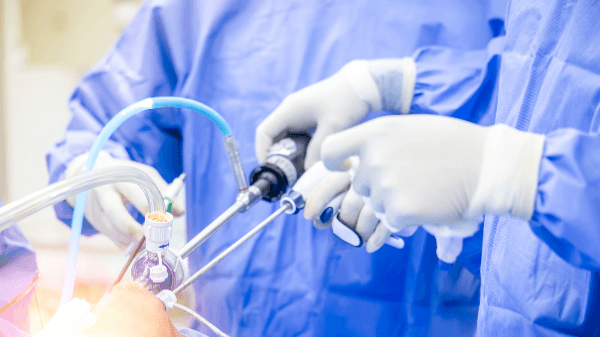
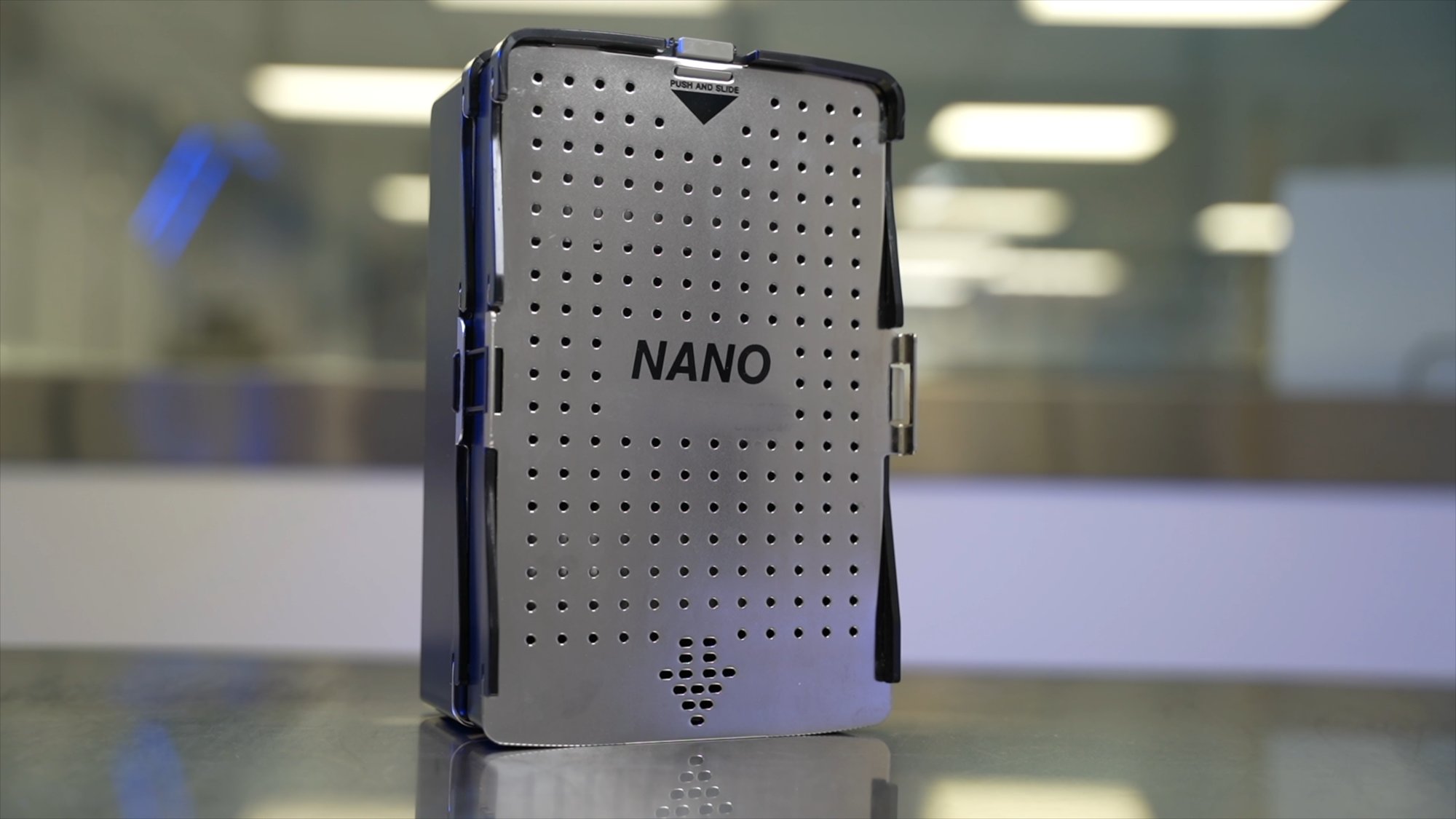
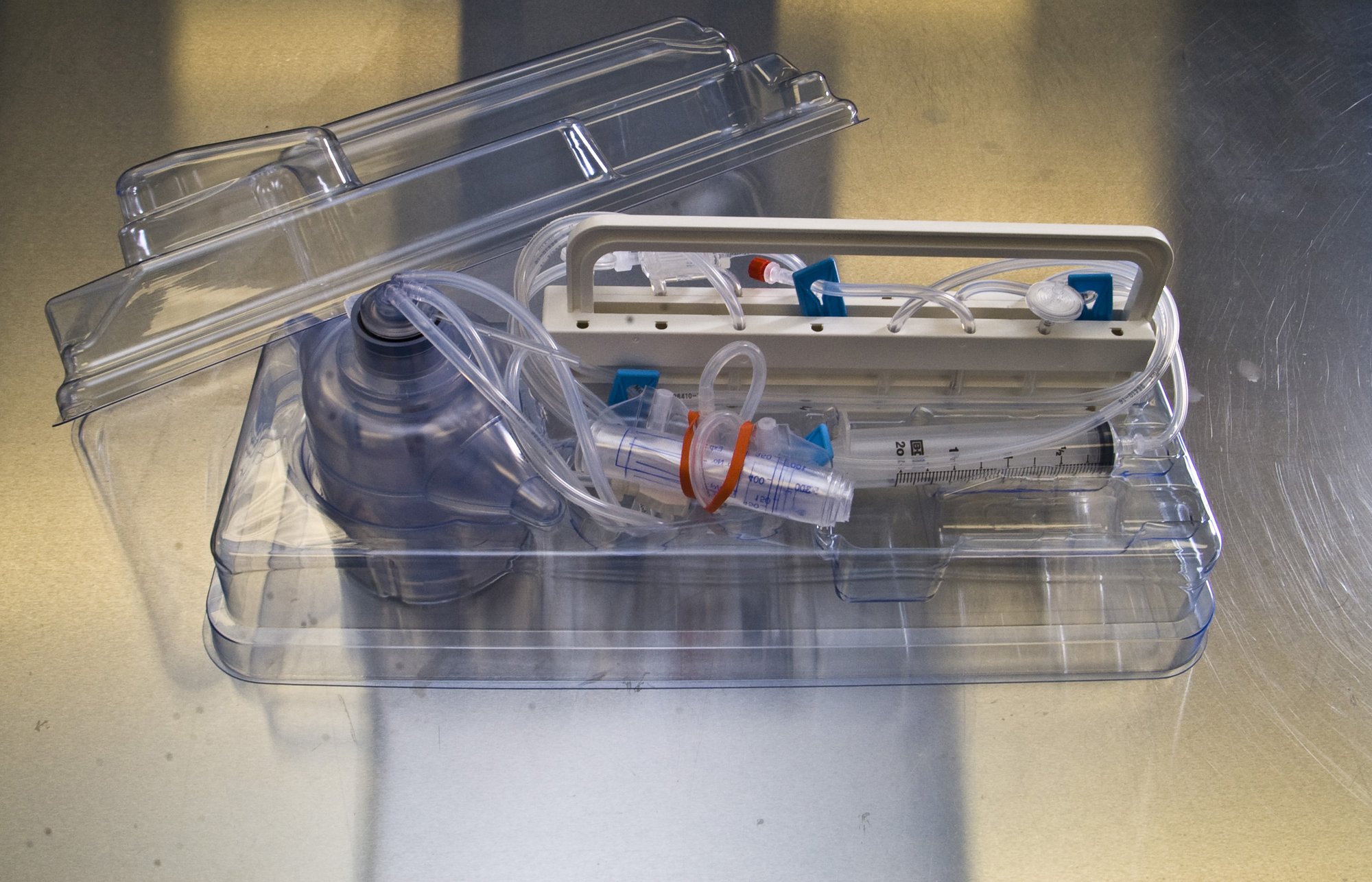
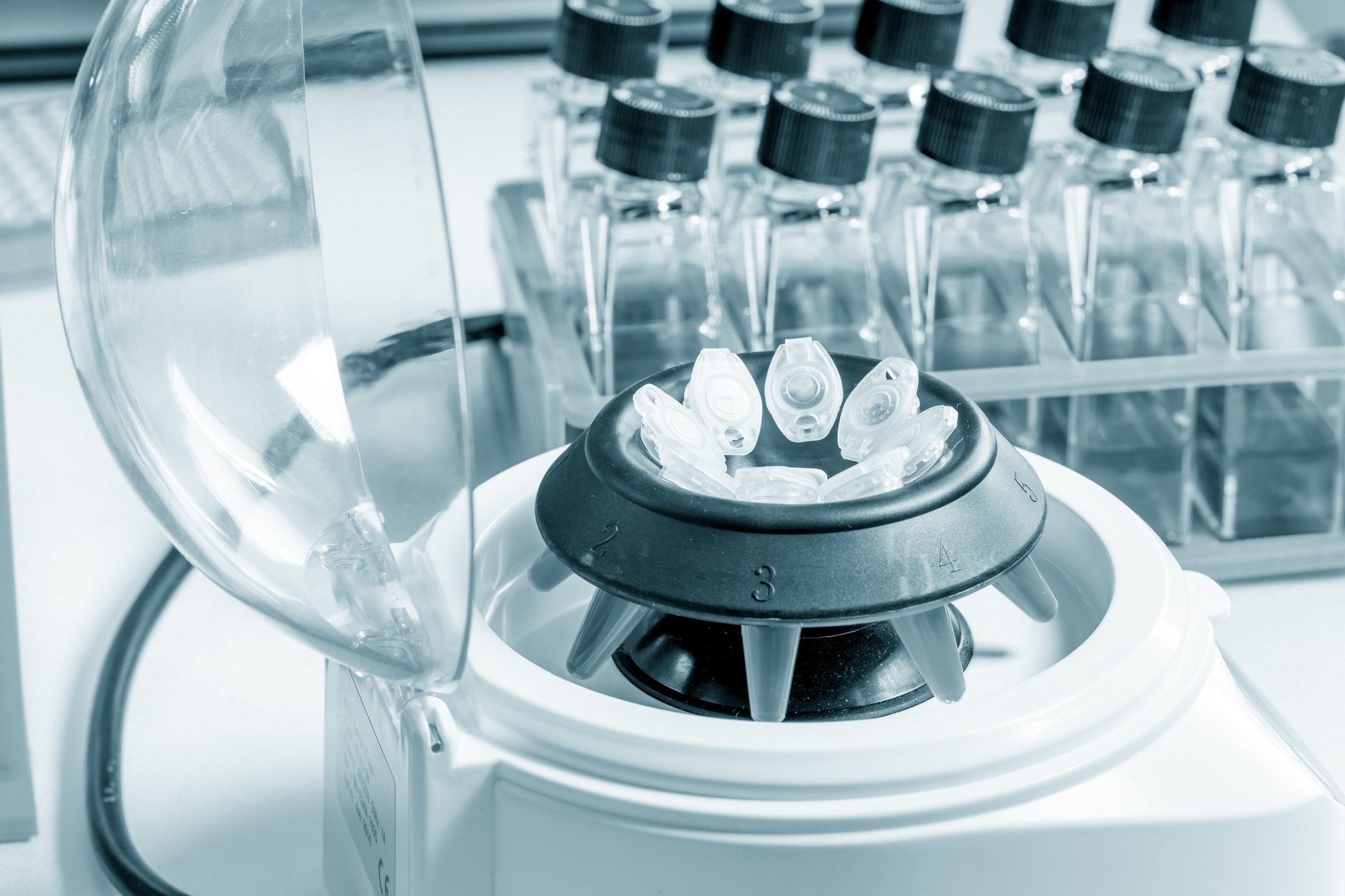
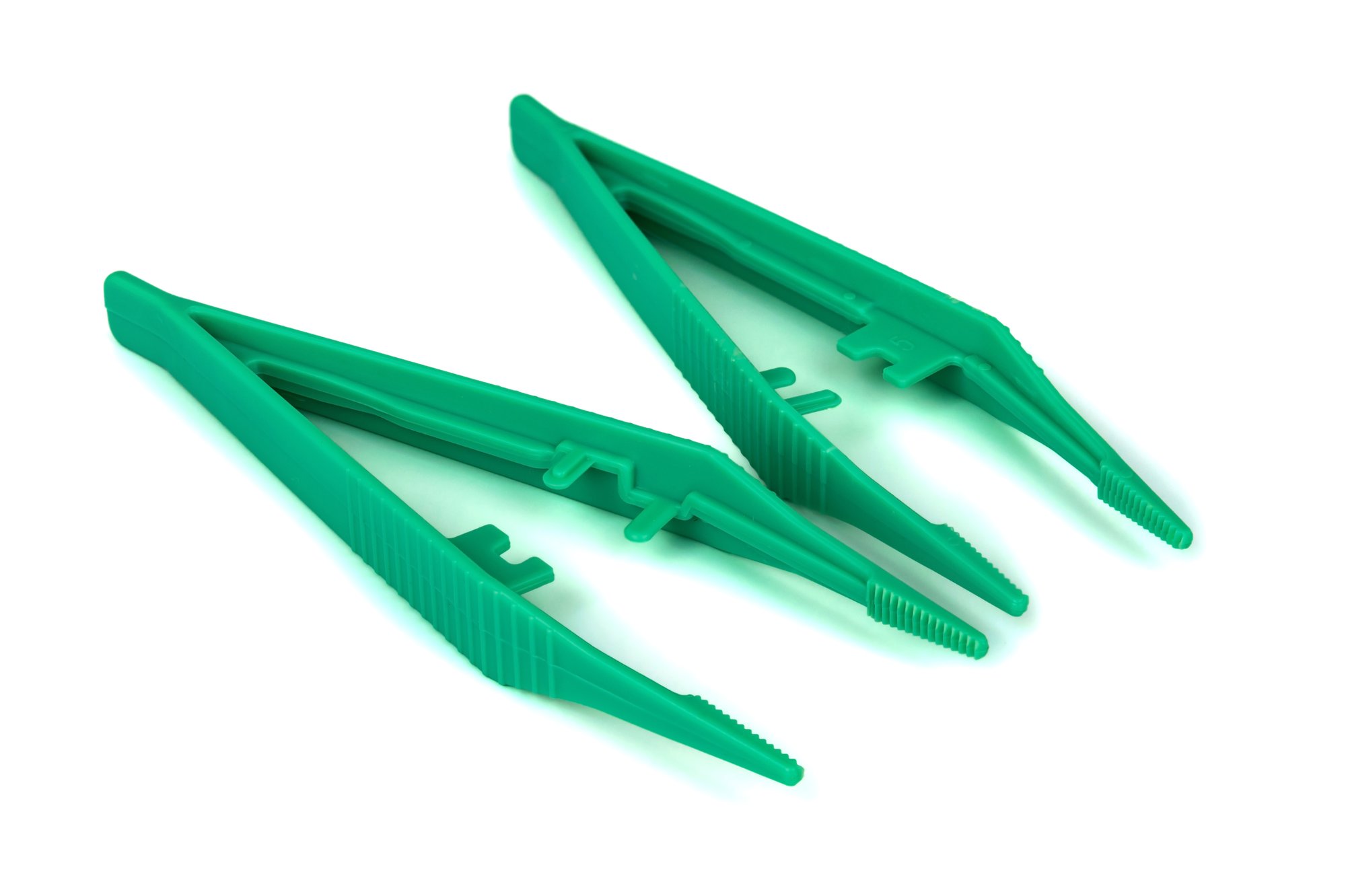
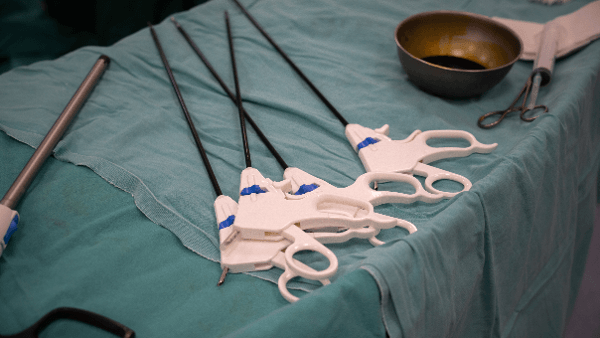
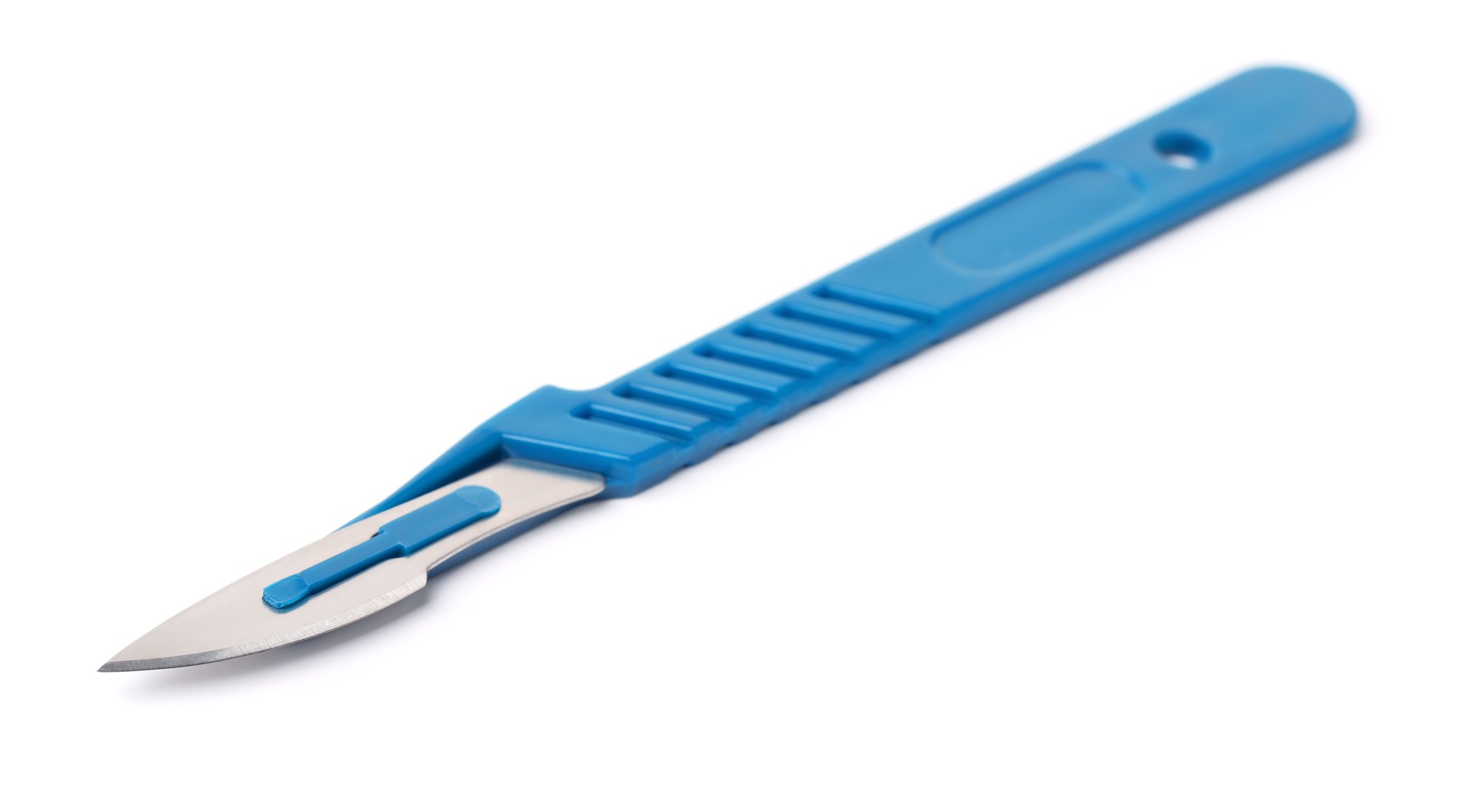
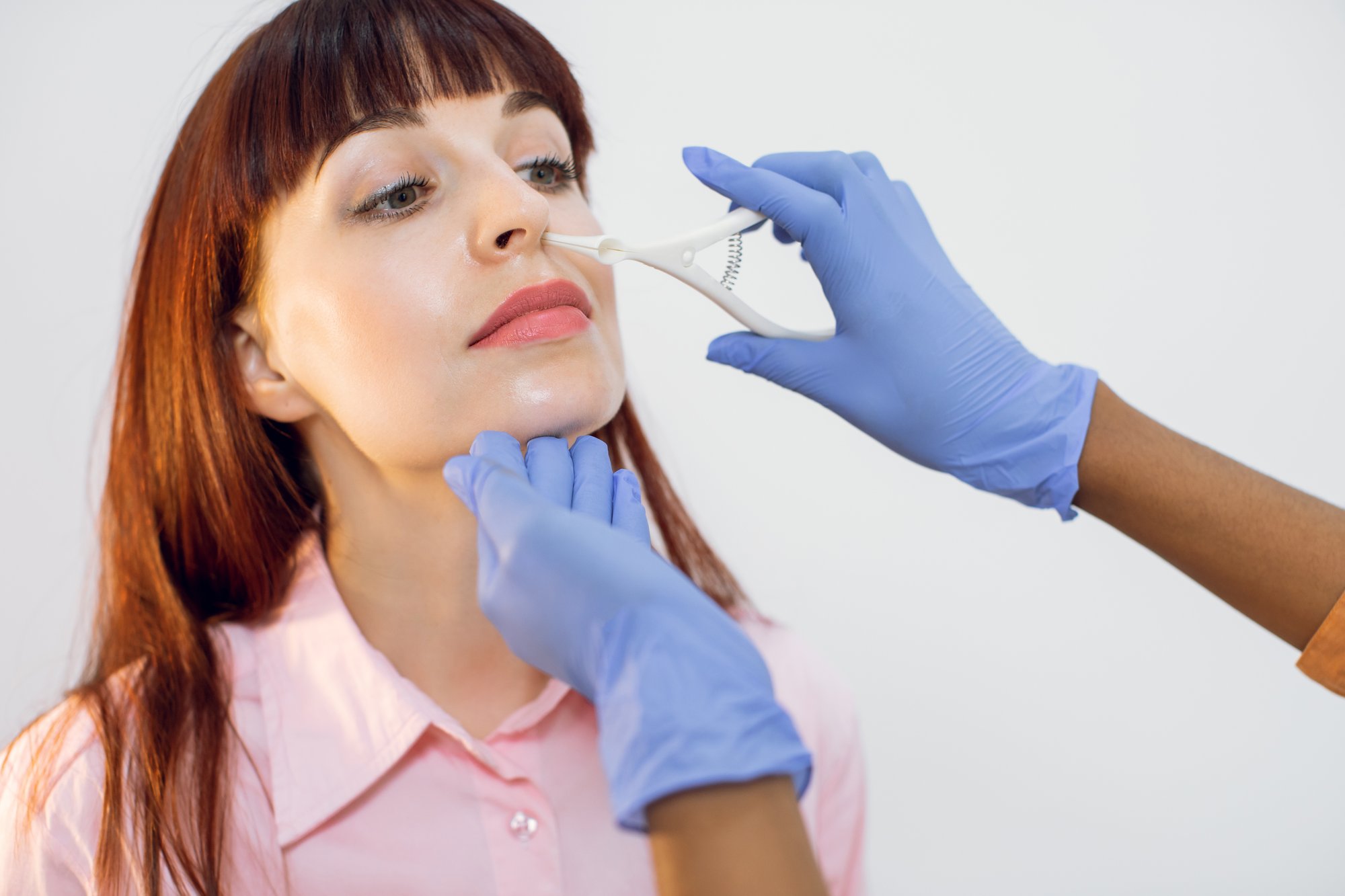
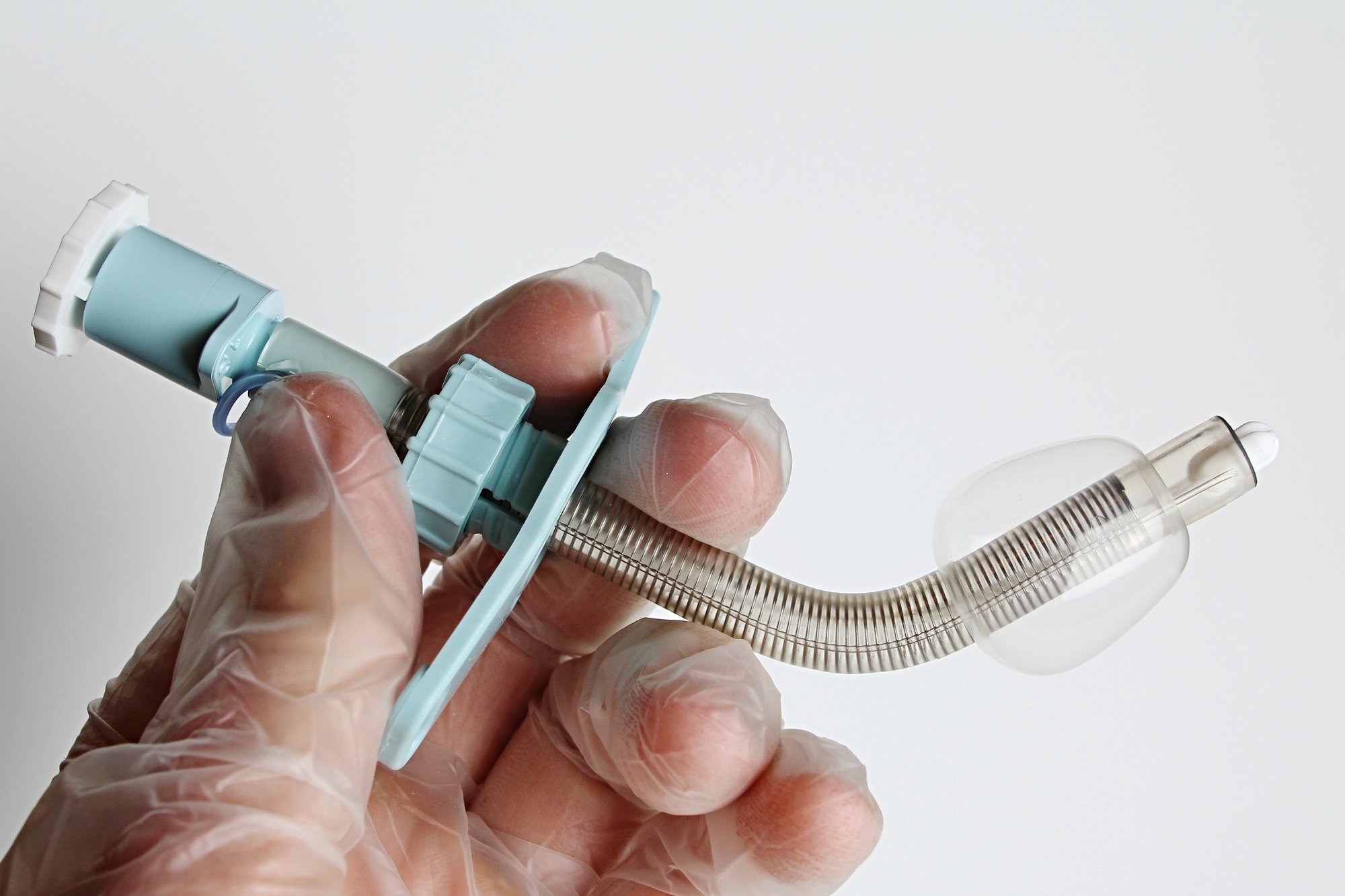
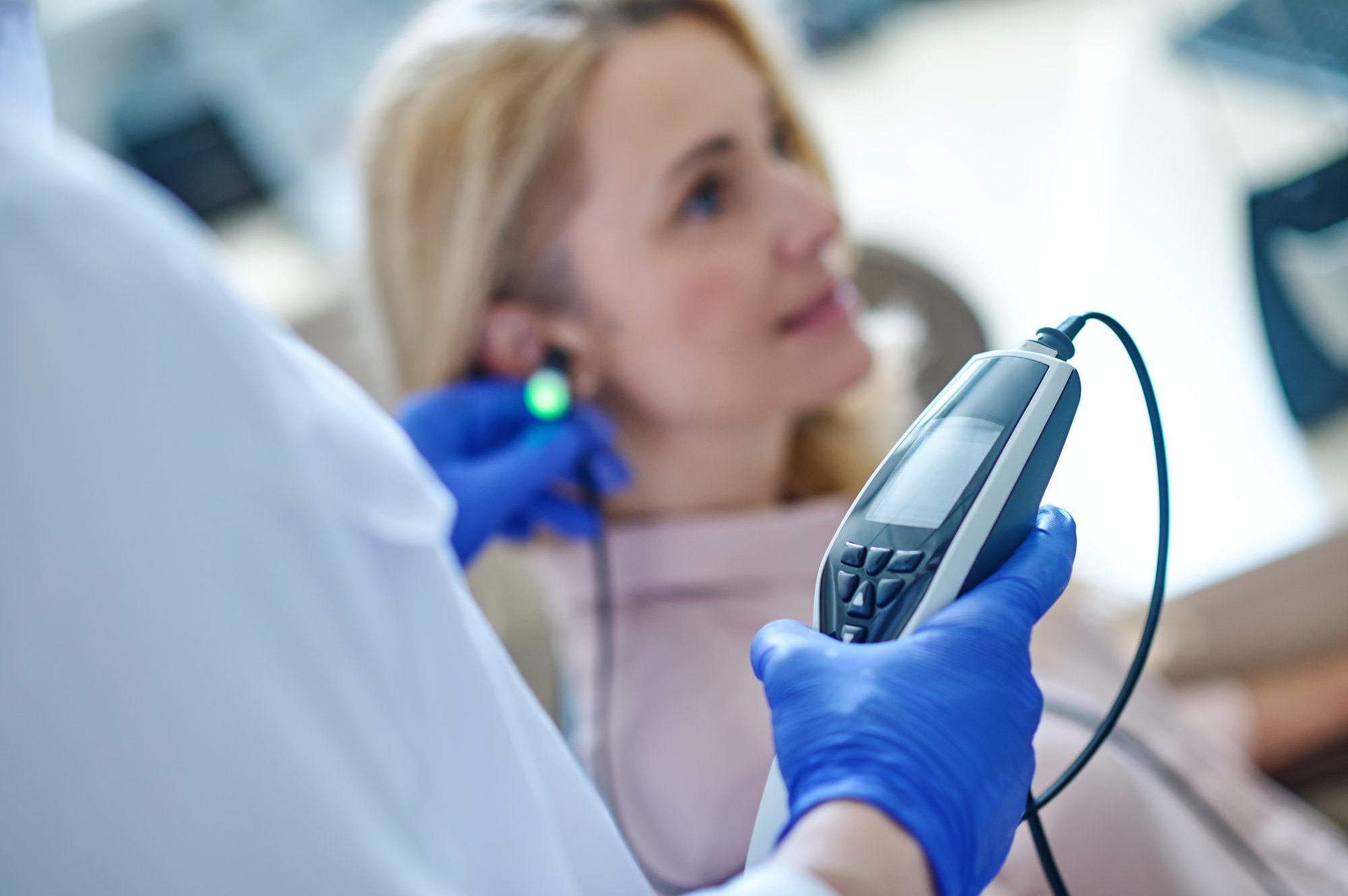
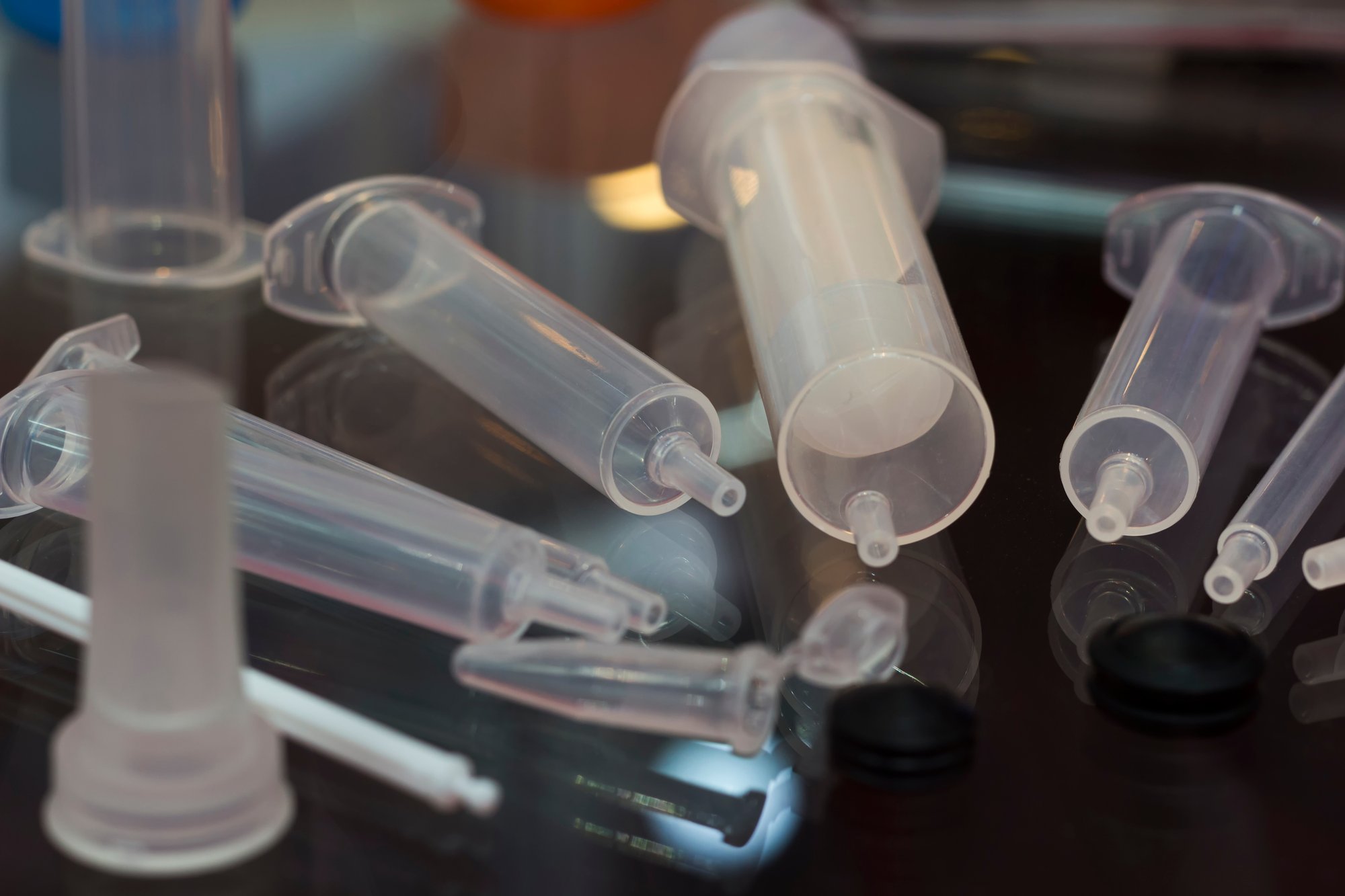
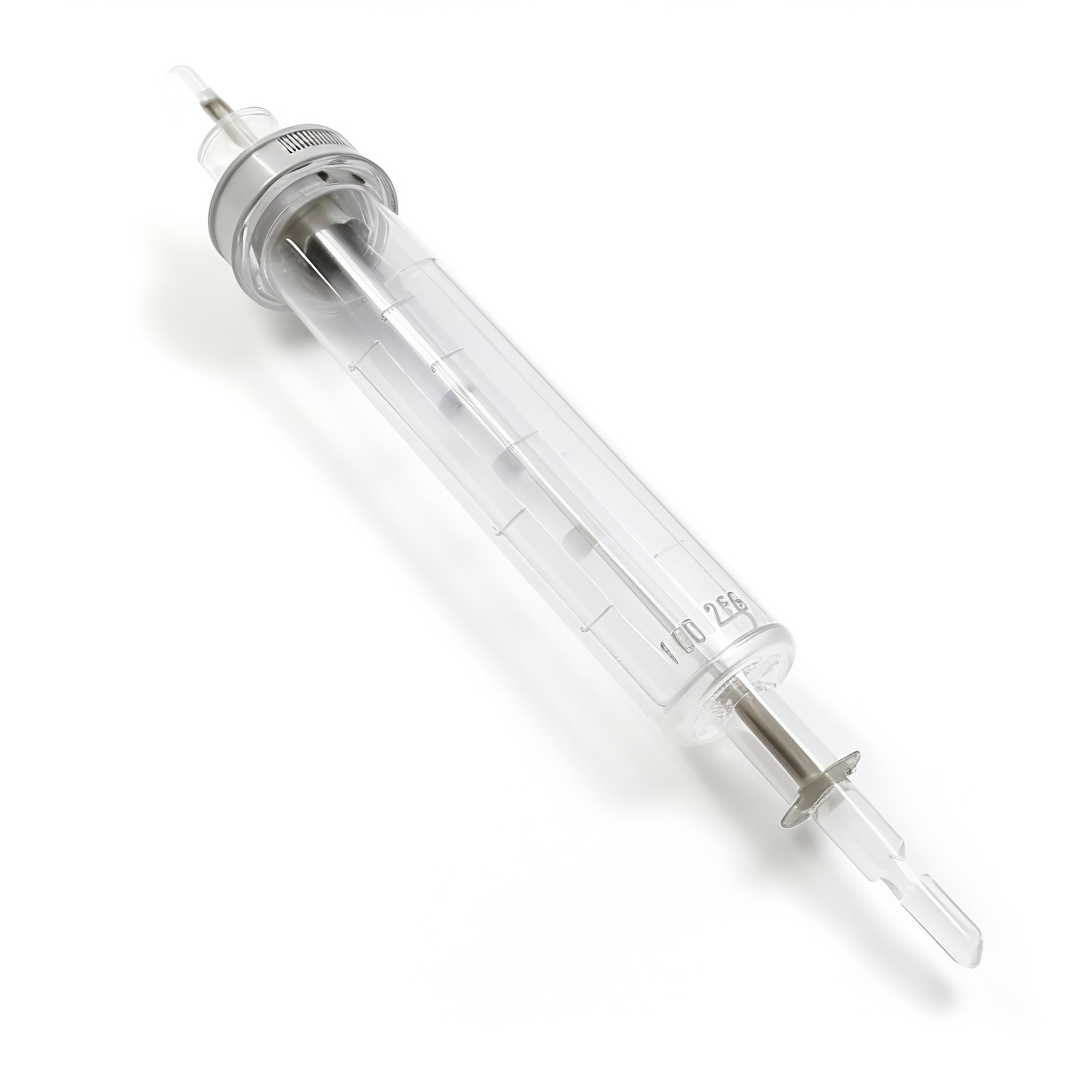
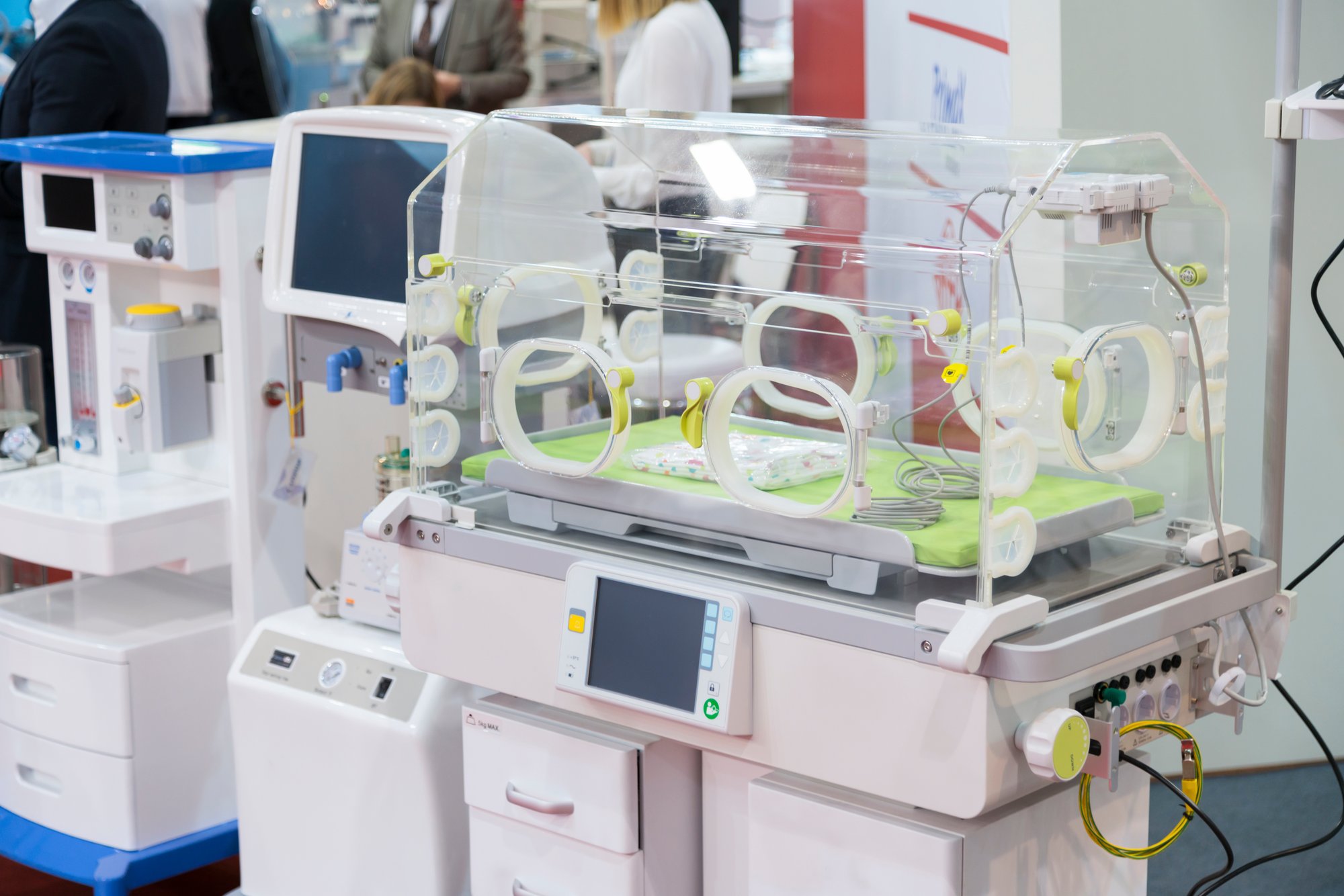
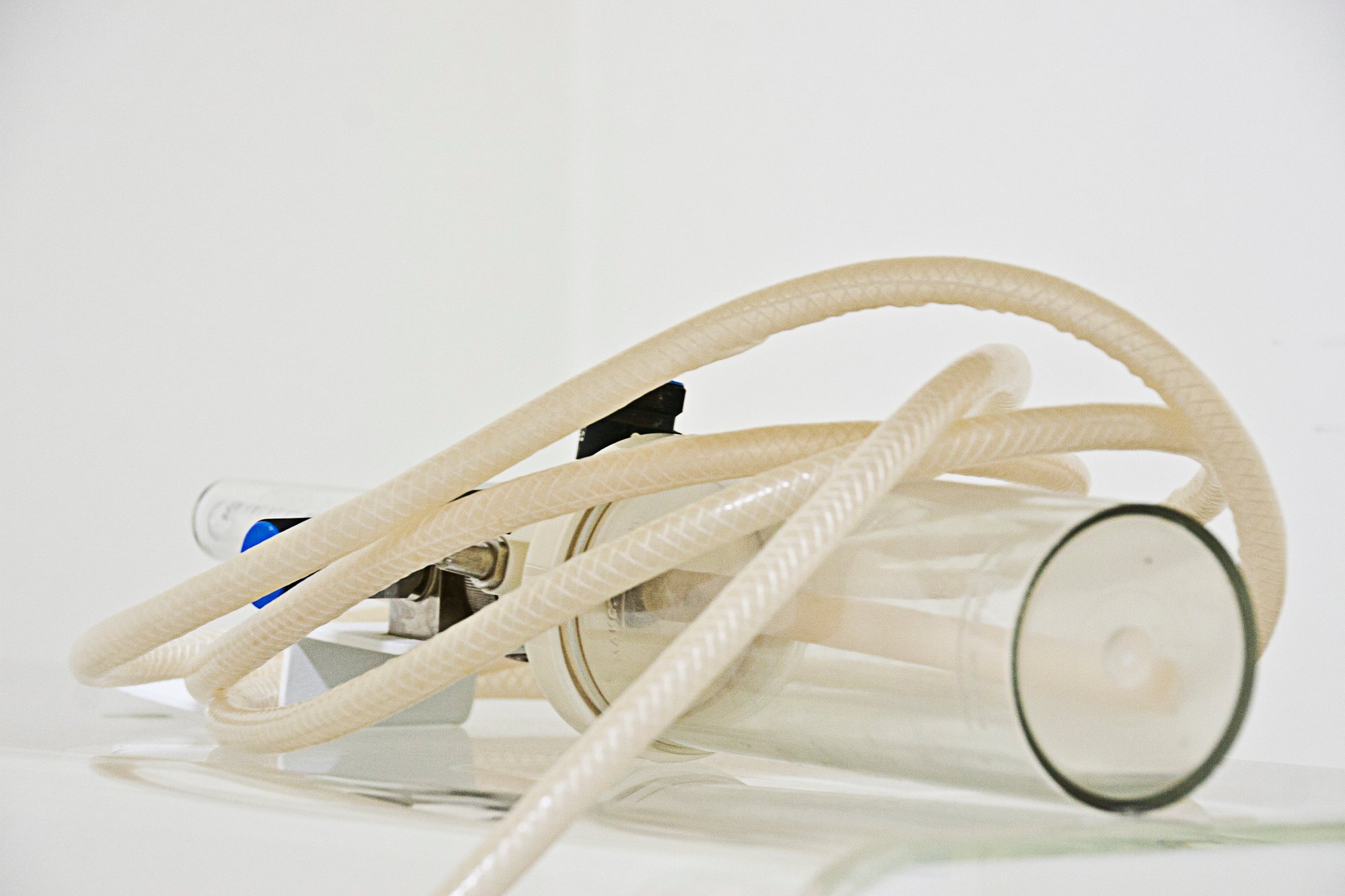
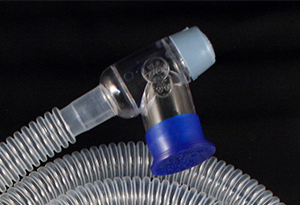
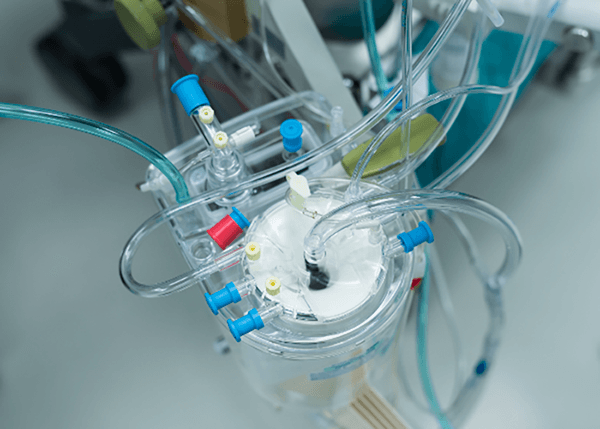
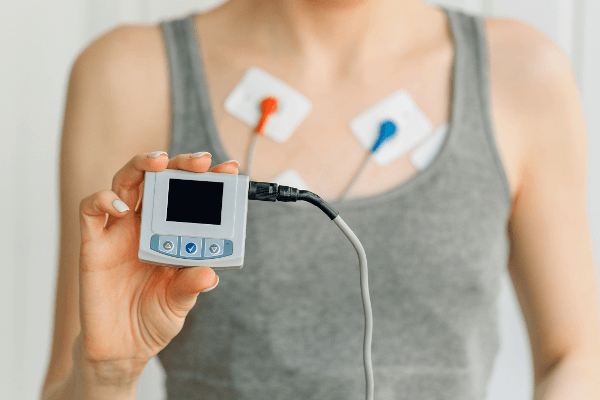
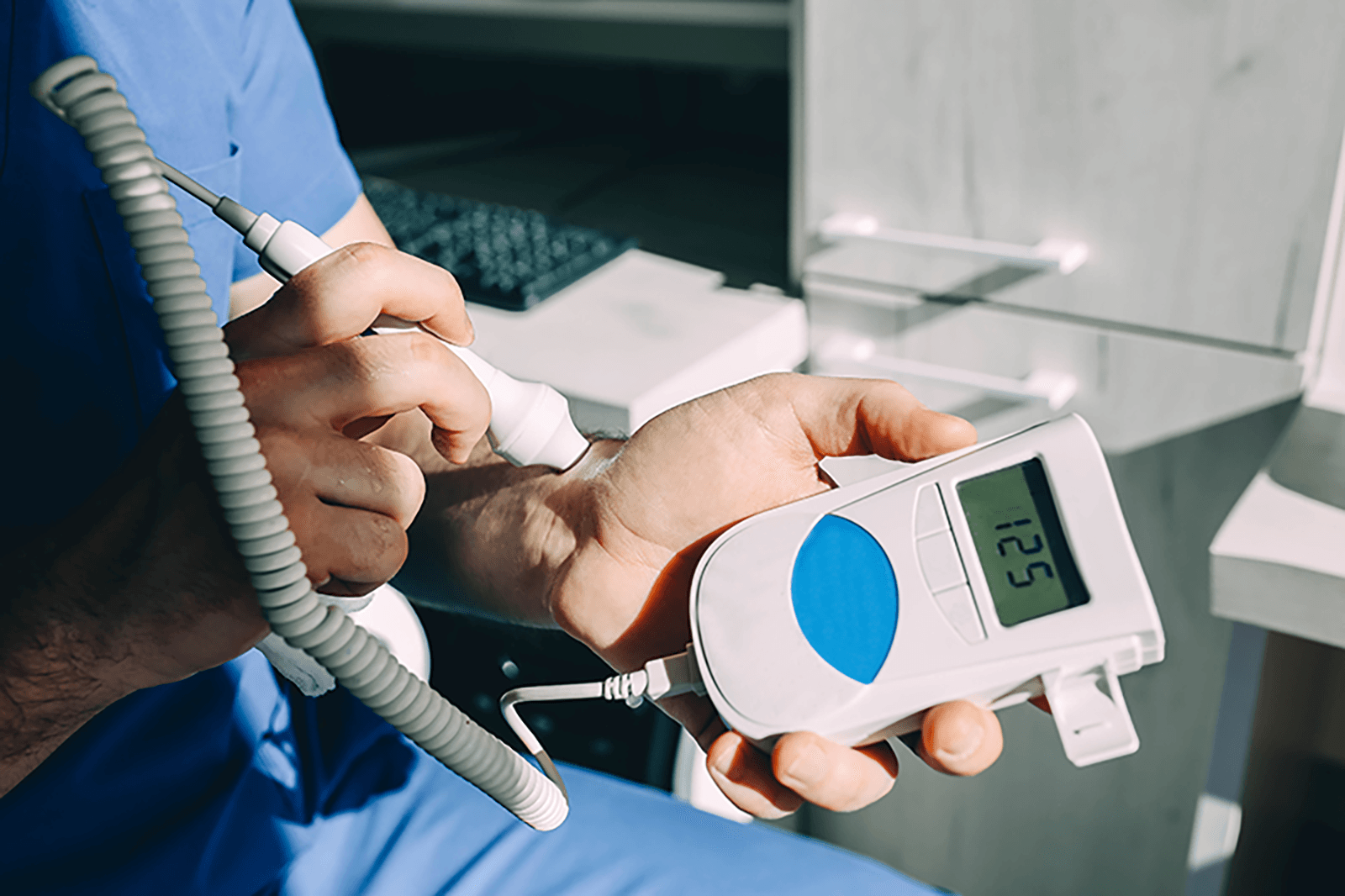
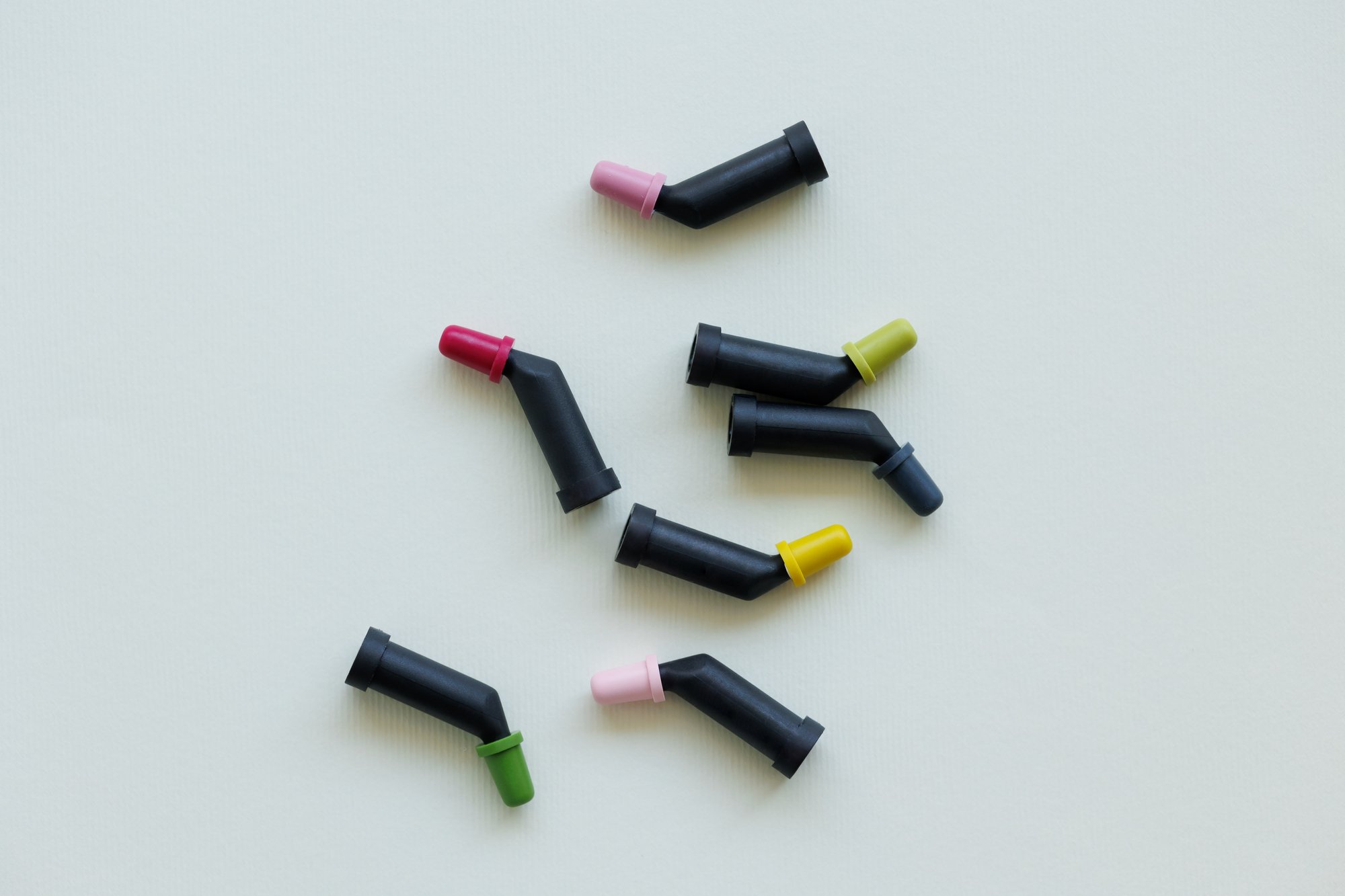
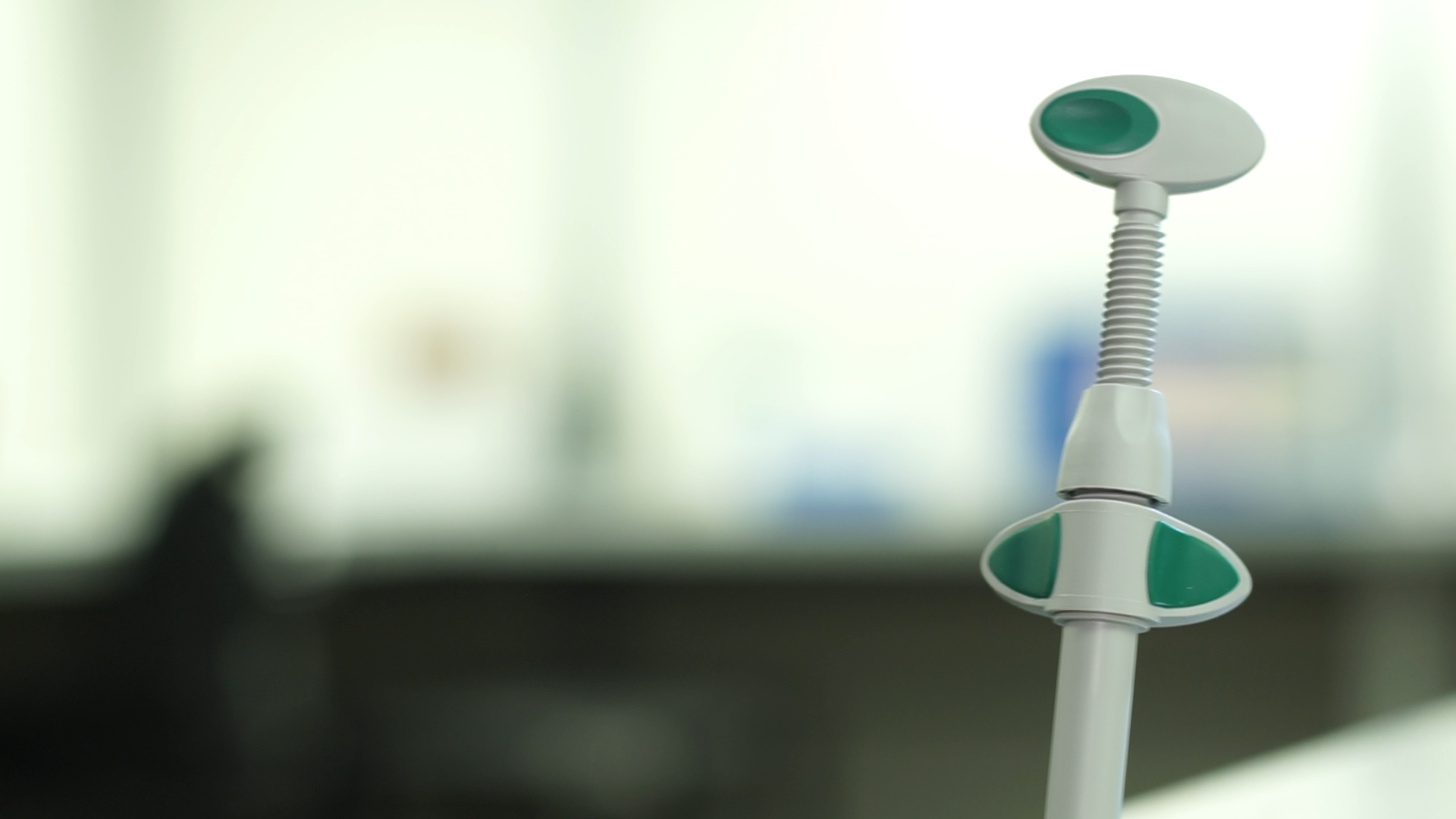
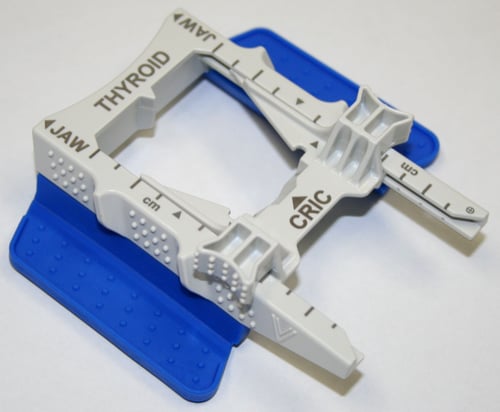
WORKING WITH CRESCENT INDUSTRIES OFFERS OUR CLIENTS A RANGE OF BENEFITS.
- Experience and expertise with medical device injection molding for 50+ years
- Guidance on DFM (design for manufacturing) and mold design using 3D mold simulation software
- New Injection Mold Tooling
- Dedicated Process Development Engineers and Protocols
- Post-Processing Operations to Complete Your Project in our cleanroom or general molding facility
- Quality Inspections – state of the art quality-lab and automated in-line inspections
- Offer Up-scaling Production Solutions
Medical Device Case Studies: Real Results from Crescent Industries
Full Service Cleanroom Injection Molding Solution
The Challange
The Solution
Custom Automated Solution
The Challange
The Solution
Crescent started by designing and building End-Of-Arm-Tools (EOAT) for each pf the four injection molds. We than use a quick change feature for each EOAT, Allowing easy and accurate switching back and forth during tooling changes.
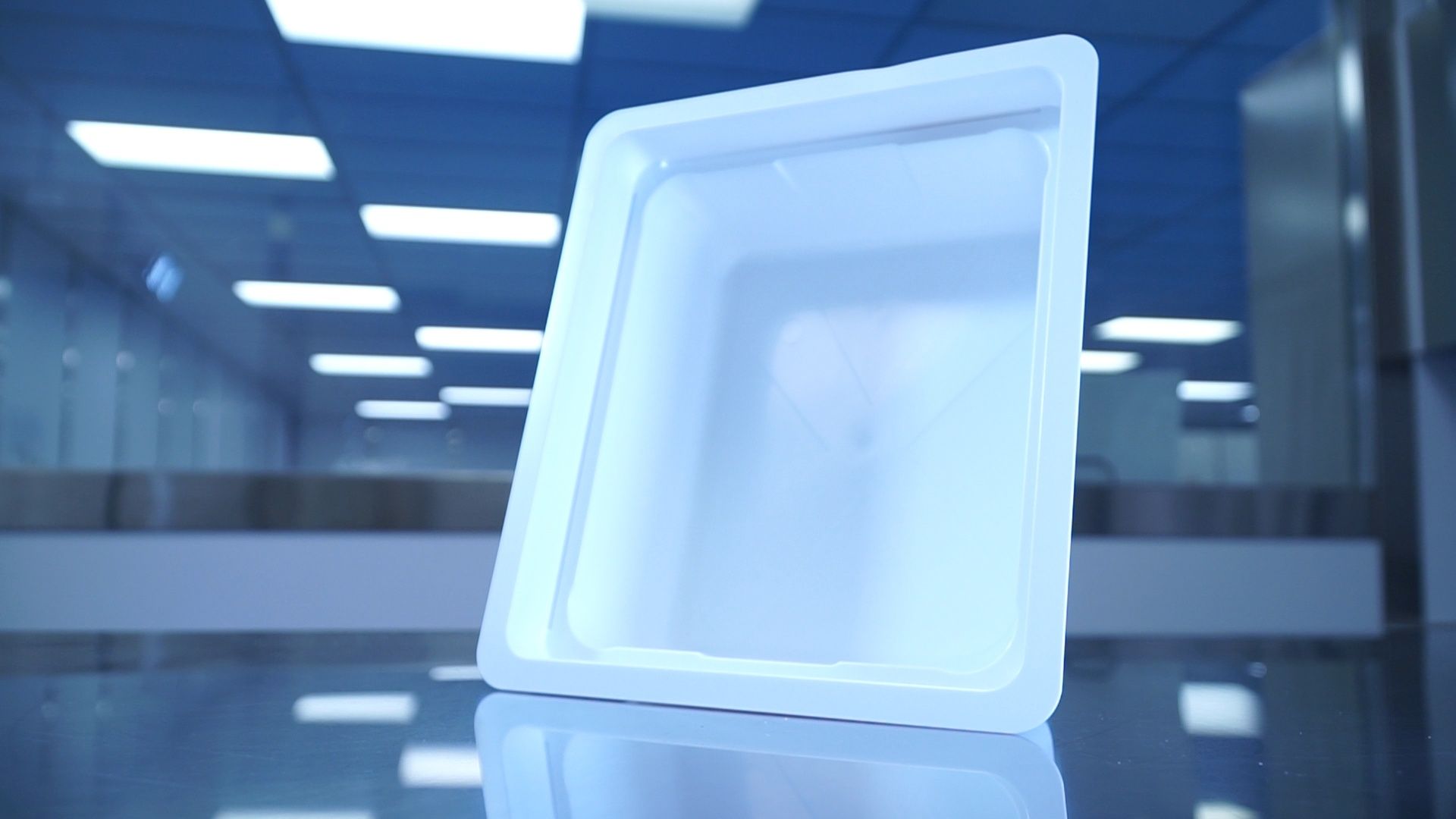
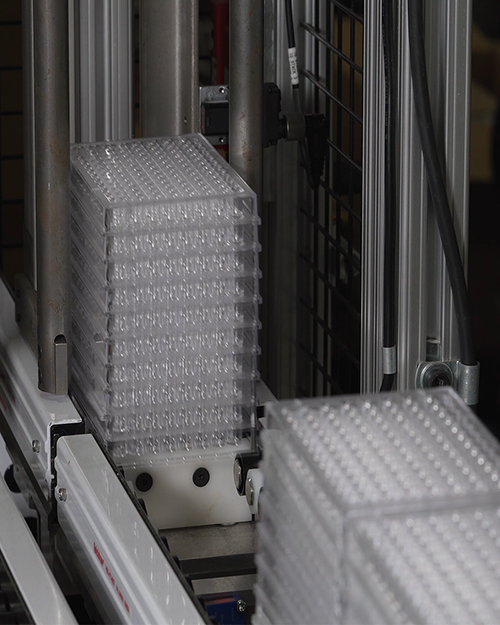
Why Choose Crescent?
Discover the countless benefits of partnering with us for all your injection molding manufacturing needs and let us show you why we are the perfect match for your business.