About Crescent Industries
75+
Years in Business
160
Employee-Owners
43 Million
Custom Parts Molded
10 Years
Average Employee Tenure
Are you in search of a company that prioritizes excellence, innovation, and quality? Look no further than Crescent Industries! With over 75 years of experience, our injection molding company is not only fourth-generation family-owned but also employee-owned. That's right- every employee is a stakeholder, which means you can expect a passionate and dedicated team that takes immense pride in their work.
At Crescent Industries, we don't just talk about collaboration, accountability, and long-term thinking - we live it. This shared ownership model fosters a unique culture that makes every employee feel valued and appreciated. It's a combination of family values and employee empowerment that sets Crescent Industries apart, ensuring a bright and sustainable future for both our team and you, the customer.
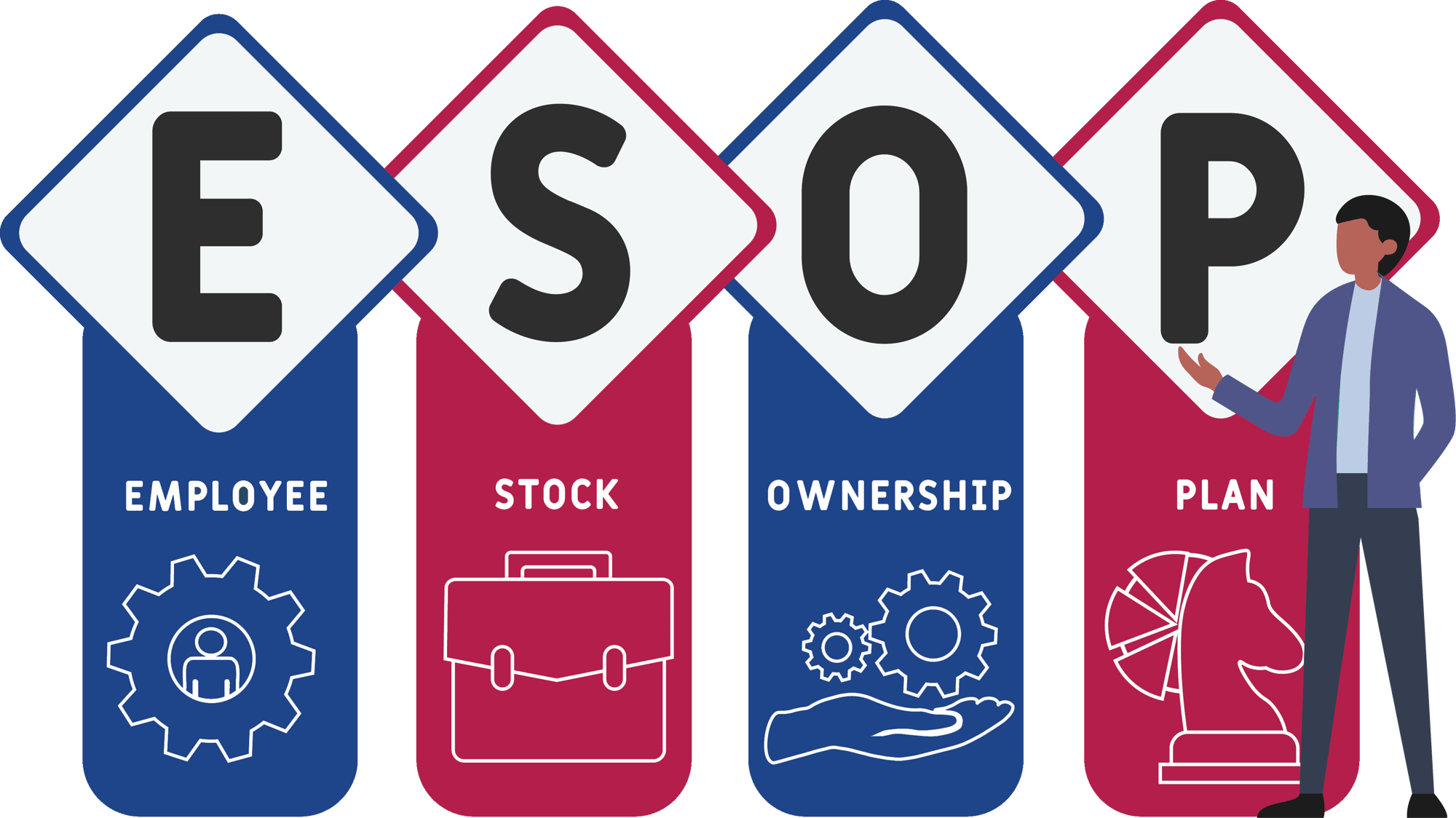
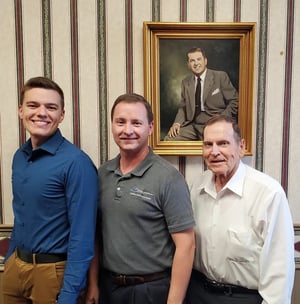
3 FACILITIES TO MEET YOUR MANUFACTURING NEEDS
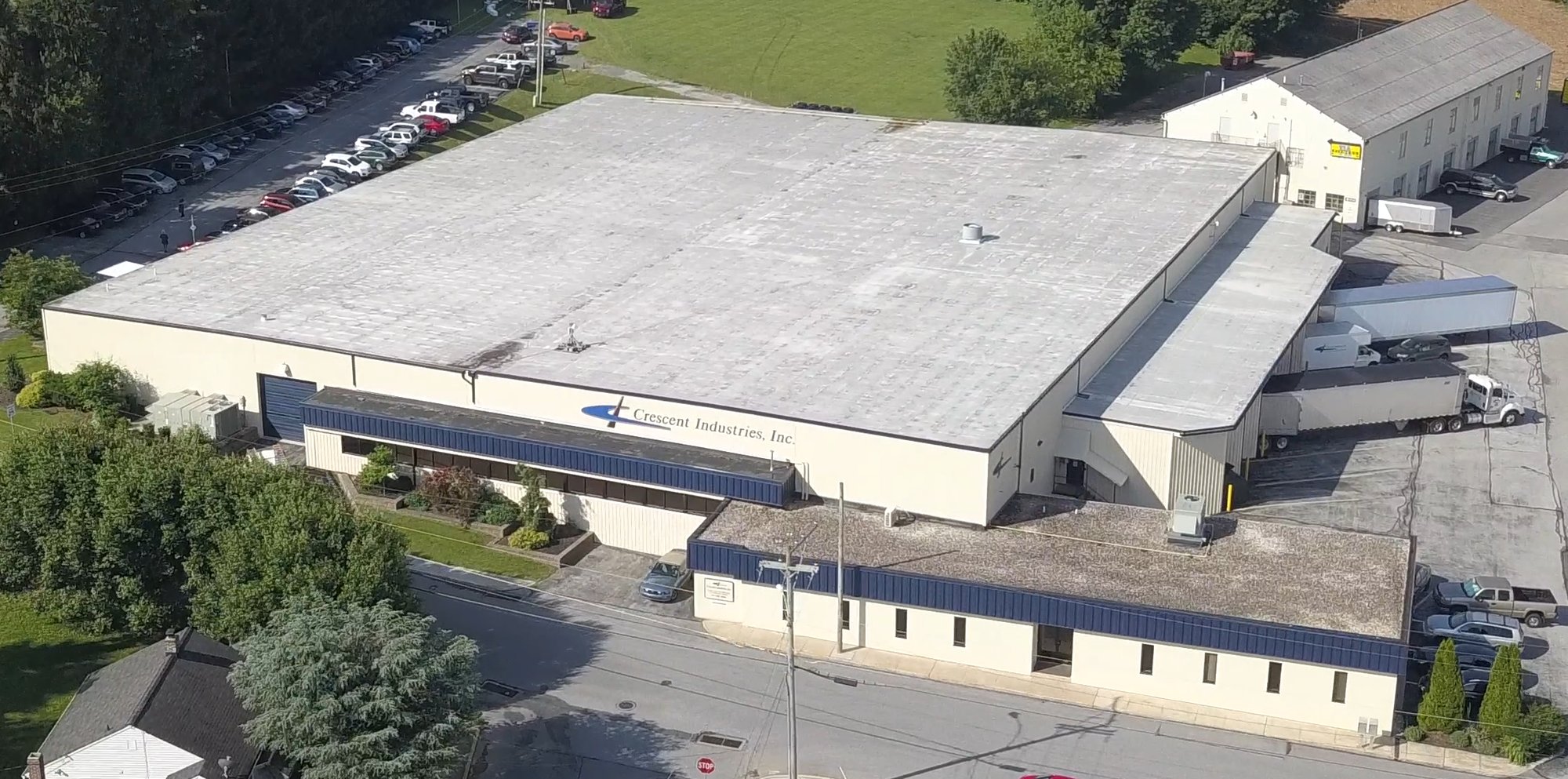

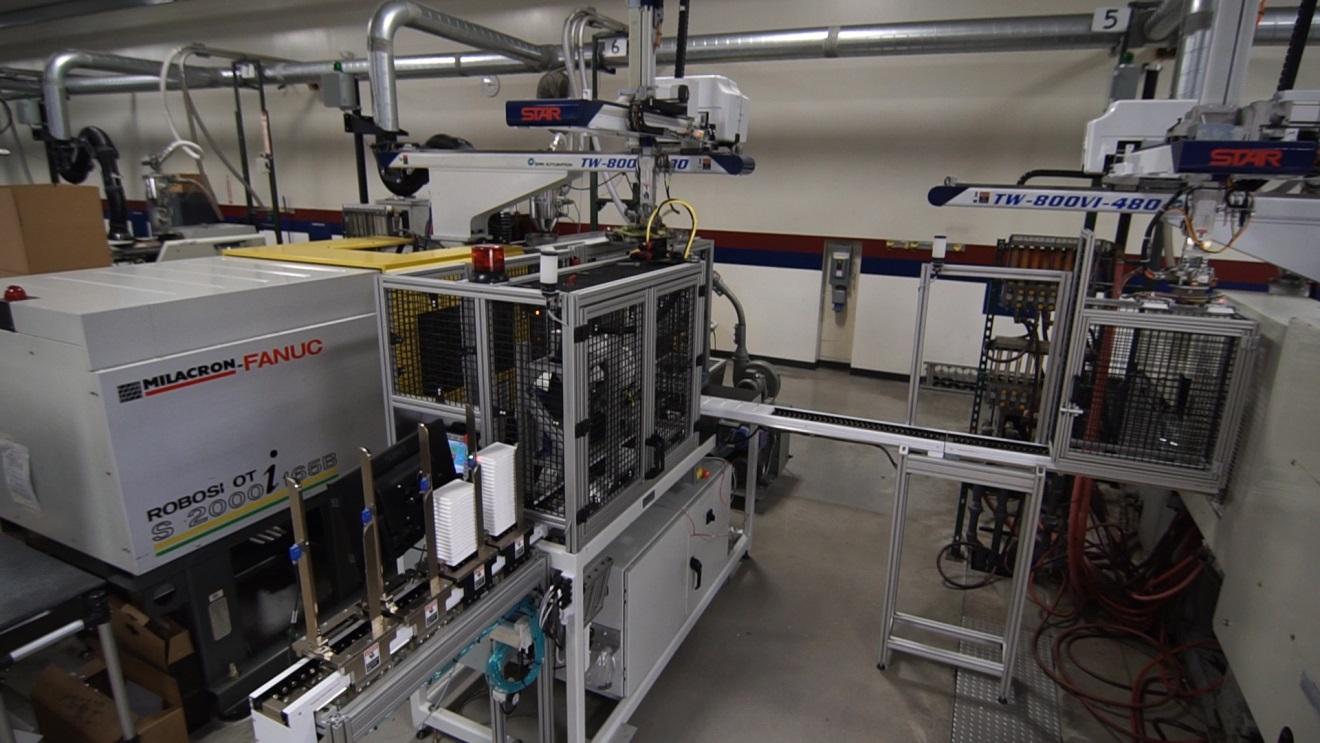
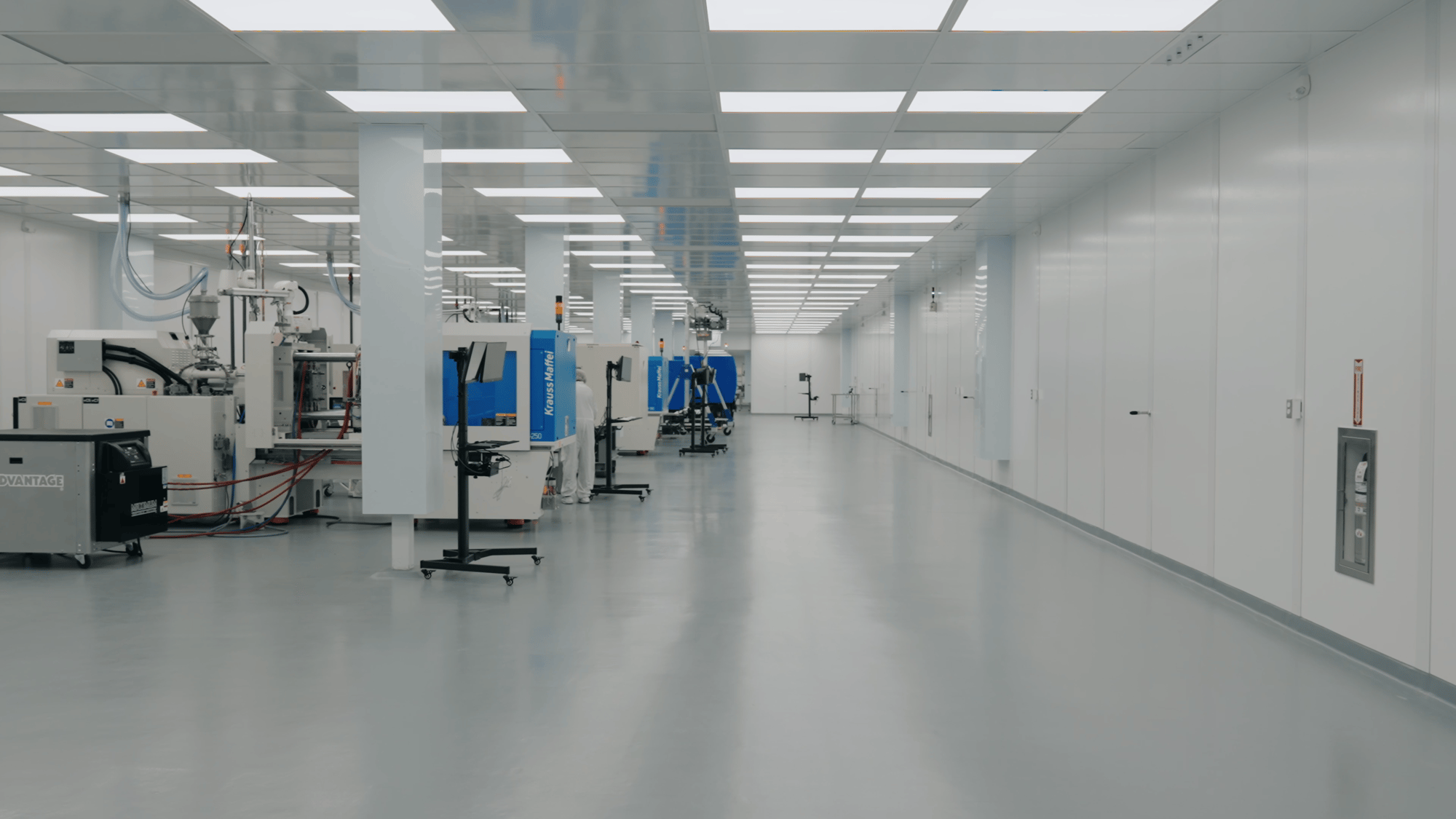
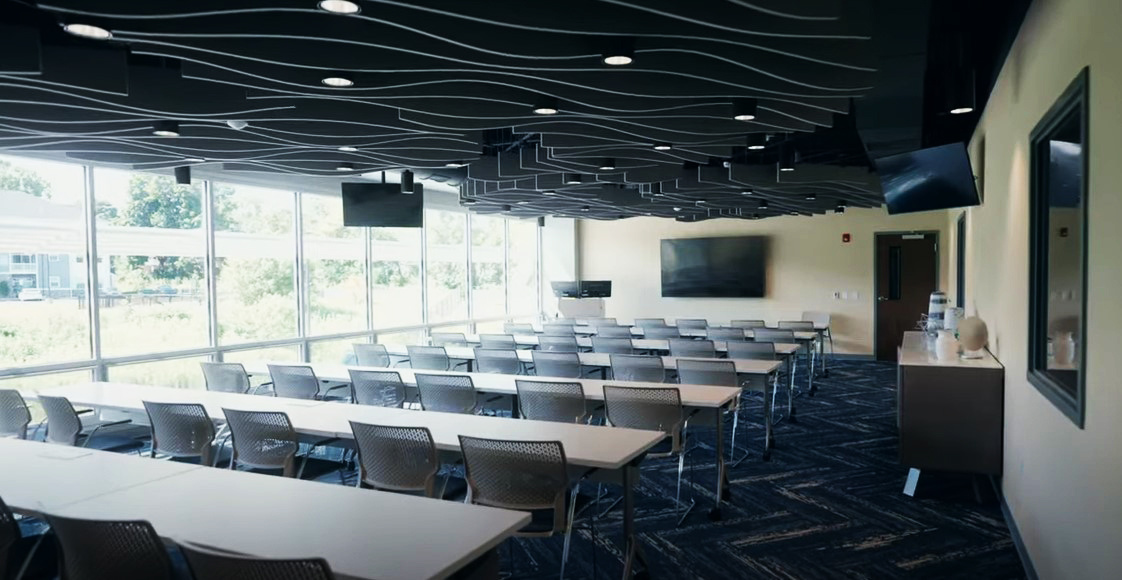
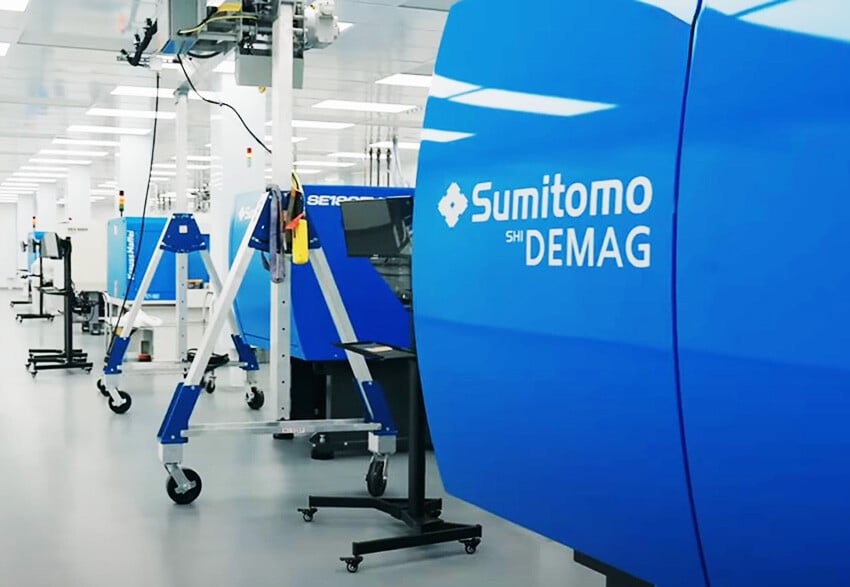
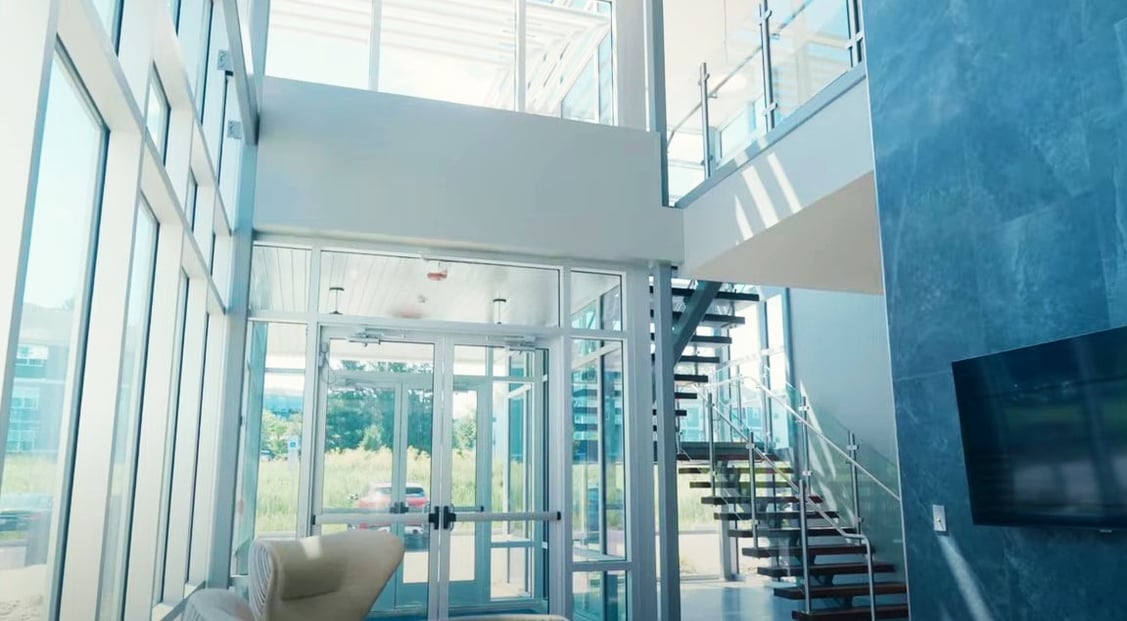
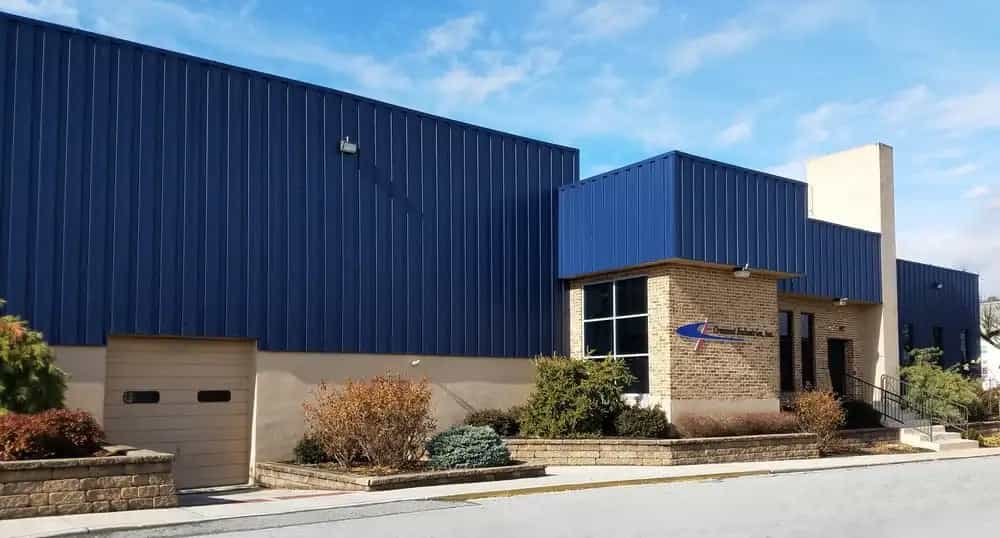
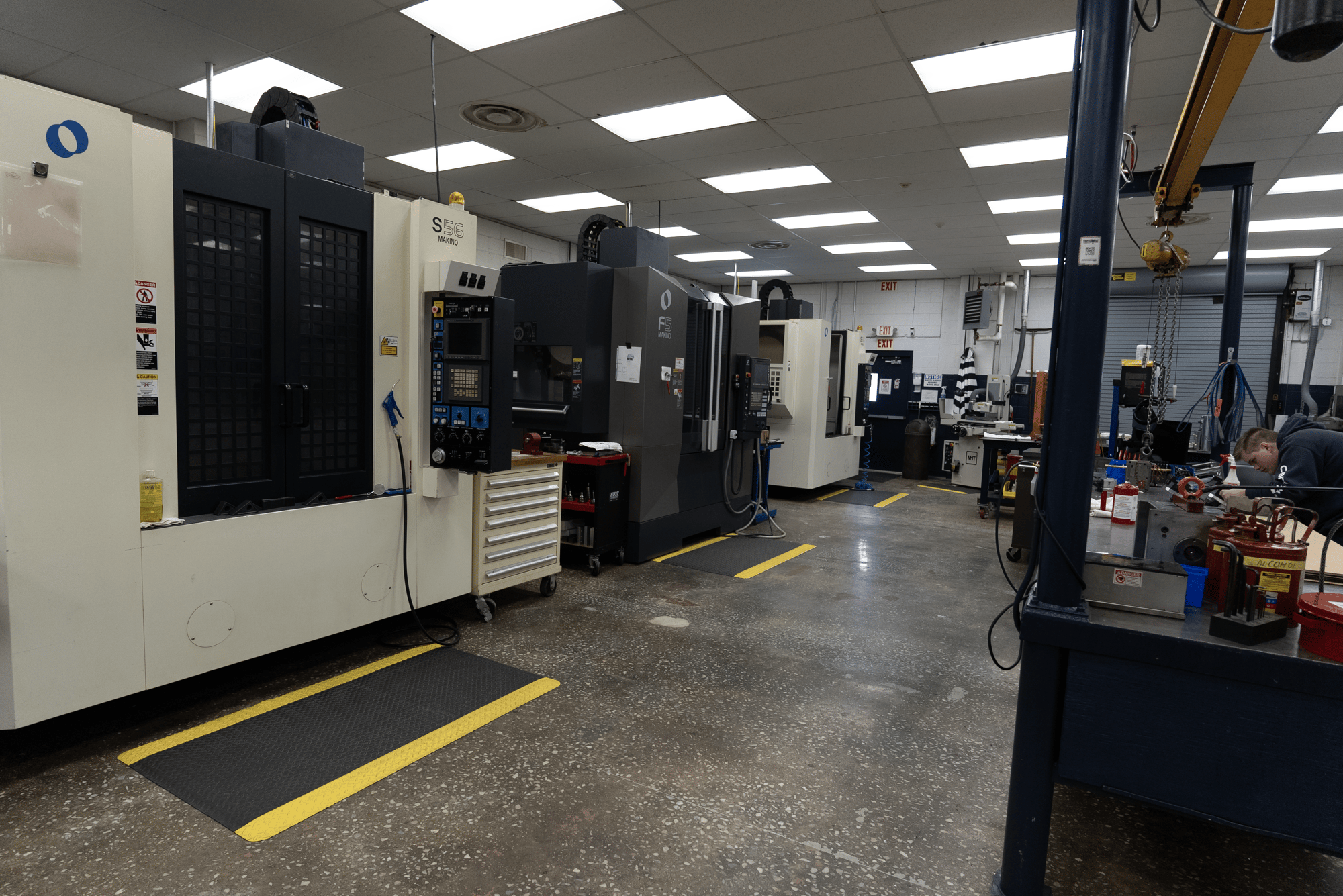
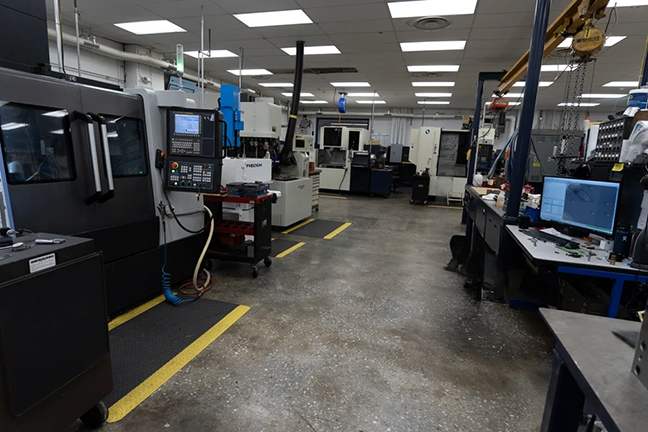
Serving the Following Markets
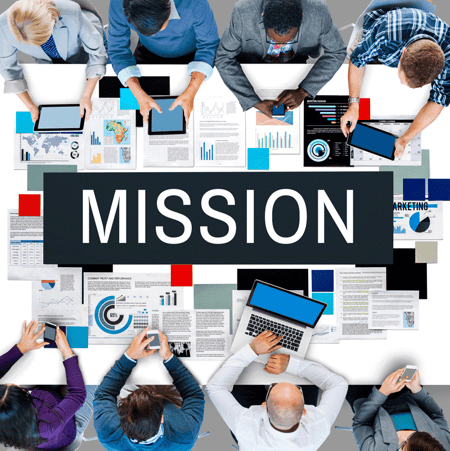
CRESCENT'S MISSION STATEMENT
Crescent Industries is a supplier of custom molds and injection-molded plastic products for medical, industrial OEM, and defense applications.
Our mission is to build mutually beneficial partnerships with our customers, providing them with exceptional product value and service. The Crescent Team is committed to high ethical standards and continuous improvement throughout all phases of our business.
We take pride in contributing to our customers’ success, and we pledge our resources to exceed expectations.
Why Choose Crescent?
Discover the countless benefits of partnering with us for all your injection molding manufacturing needs and let us show you why we are the perfect match for your business.