Smarter Production Starts Here: How In-House Automation from Crescent Delivers Consistent Results
Reduce labor demands, accelerate cycle times, and improve part consistency with robotics tailored to your process
Crescent Industries is committed to offering the highest-quality and most efficient injection molding processes. We extensively use in-house injection molding automation to support our capabilities and provide optimal service. This ensures maximum quality and repeatability while reducing production time, improving efficiency, and keeping costs reasonable. Watch the video to learn more.➡️
.png)
Types of Automation Used at Crescent!
-
End-of-arm tooling (EOAT)
End-of-arm tooling allows robots to pick and place materials and products in a wide range of shapes and sizes, and to complete tasks such as assembly, packaging, pad printing, and more.
-
Collaborative robots
Collaborative robots, also called cobots, are found more and more frequently in our injection molding processes, especially for lower volumes and custom applications. Collaborative robots are built to work safely within close proximity with humans, assisting in tasks such as heavy lifting and loading, finely detailed assembly, and more. -
Automated work cells
Automated work cells foster efficiency and produce upscale benefits by integrating various tasks or processes into one work area. With the benefit of interchangeable end-of-arm tooling, robotics to carry out a number of tasks to reduce overhead and costs. Watch this automated assembly work cell created by our in-house automation team.
Benefits of Injection Molding Automation
Automation creates several benefits throughout all stages of the injection molding process. These benefits are passed on to you in the form of increased quality, reduced cost, and shorter lead times.
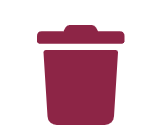
Reduce Part Rejects
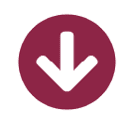
Reduce Labor For Injection Molding
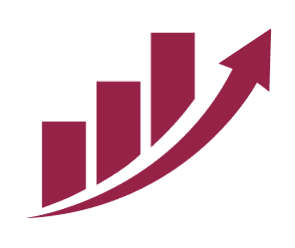
Increase Injection Molding Throughput
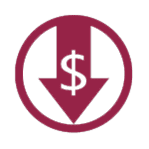
Reduce Overall Costs While Maintaining Quality
SEE HOW CRESCENT DOES IT: REAL CLIENT RESULTS!
Custom Automated Solution
The Challange
The Solution
We Started By Designing And Building End-Of-Arm-Tools (EOAT) For Each Of The Four Molds. We Use A Quick Change Feature For Each EOAT, Allowing Easy And Accurate Switching Back And Forth During Mold Changes.
Slashing Lead Times by Innovative Automation
The Challange
The Solution
Why Choose Crescent?
Discover the countless benefits of partnering with us for all your injection molding manufacturing needs and let us show you why we are the perfect match for your business.