ITAR RegisterED Military Manufacturing Company
Your Trusted Partner in Military Injection Molding Solutions
At Crescent Industries, we understand the magnitude of responsibility that comes with military applications. As an ITAR-registered manufacturer, we are recognized by the US Department of State for our commitment to meeting the highest standards for security and compliance.
Using scientific and decoupled molding to establish a stable and reliable injection molding process, starting with LRIP (low-rate initial production) for proof of design before moving to FRP (full rate production).
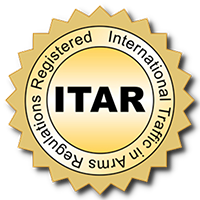
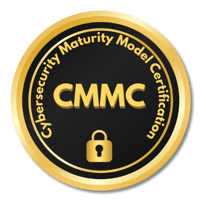
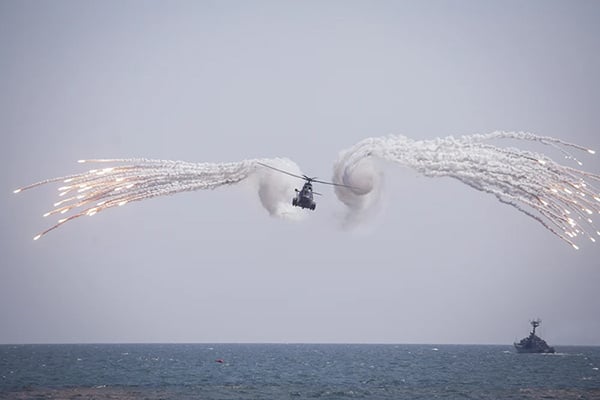
Our expertise in military injection molded applications include:
- Handheld Communication Devices
- Weaponry
- Binocular & Monocular Housings
- Military Medical Devices
- Munitions
- Decoys
- Battery Packs
- Guidance Systems
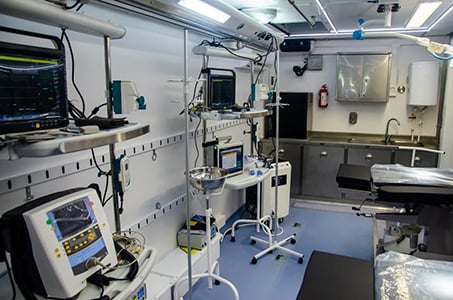
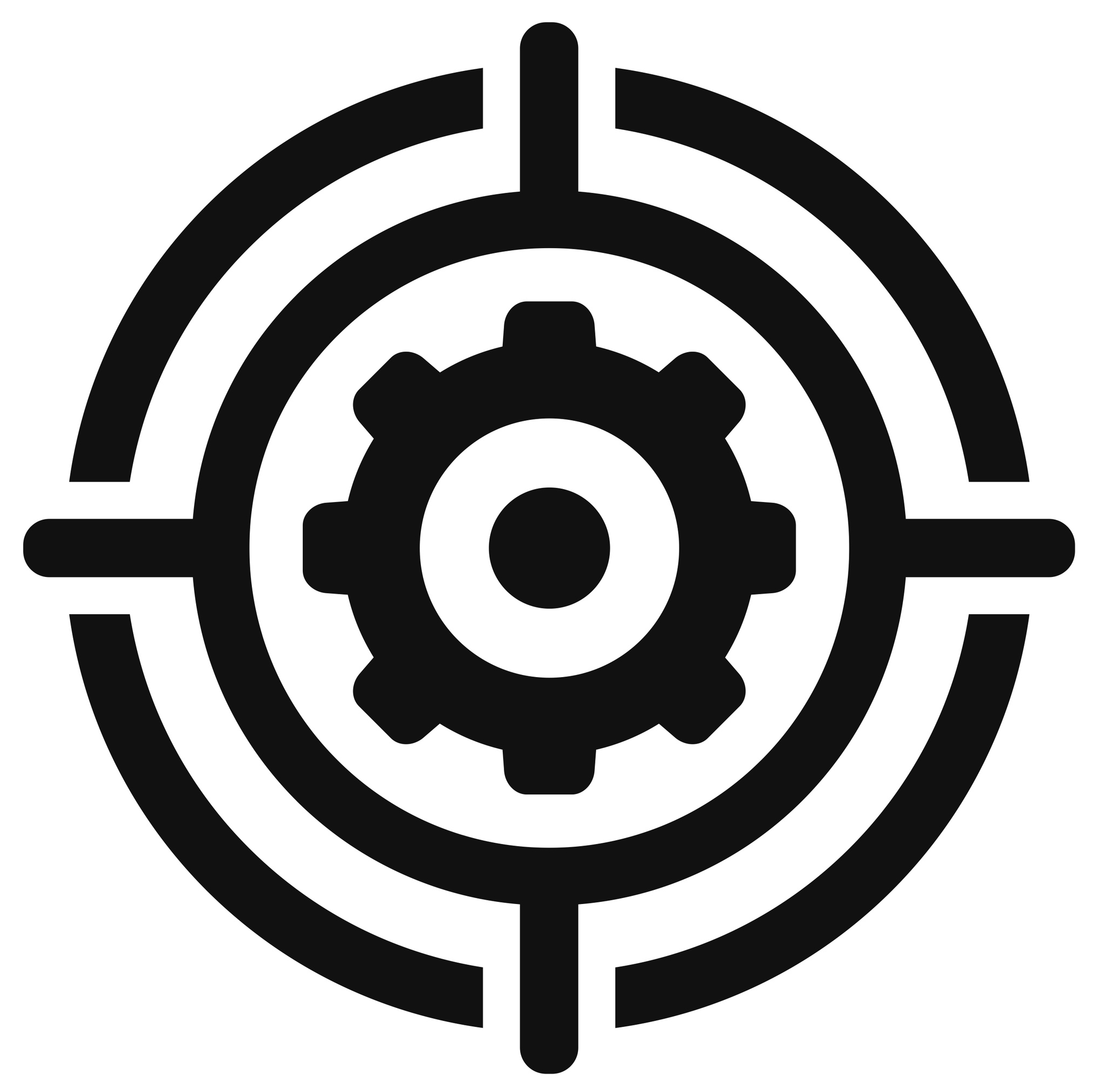
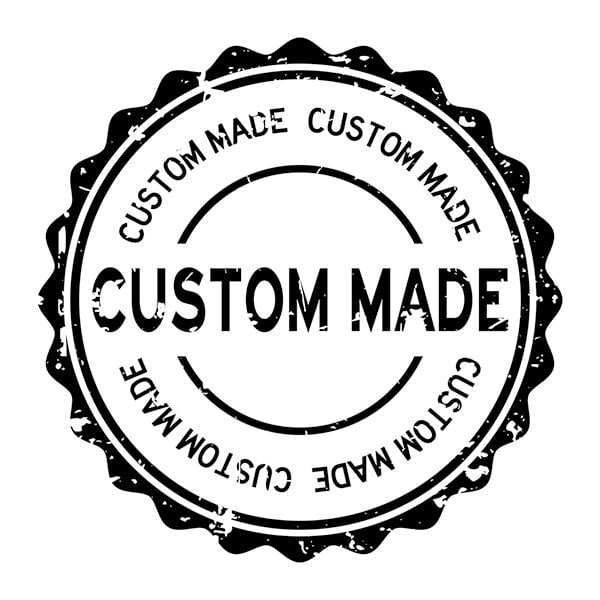
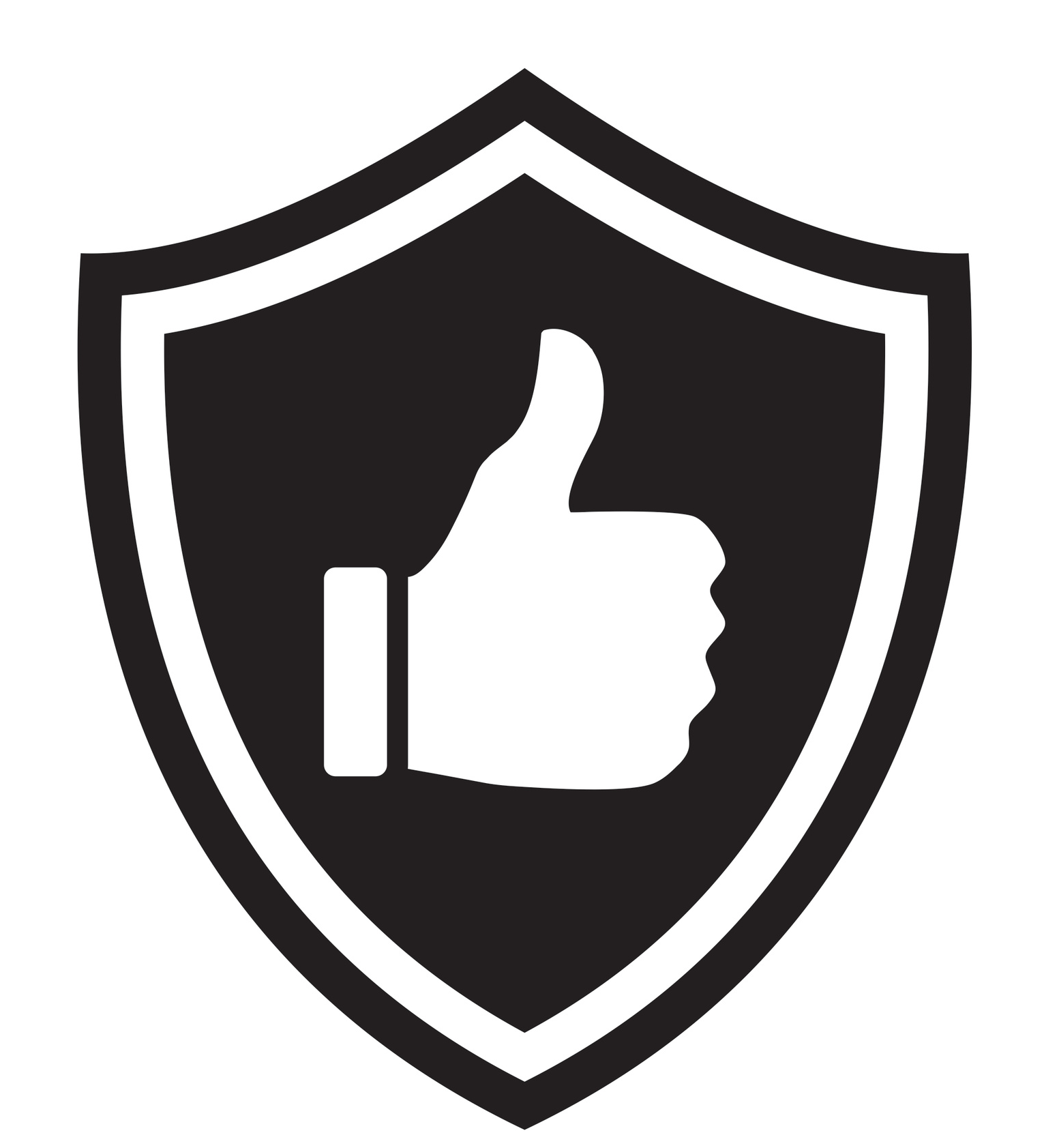
Our focus is on precision and reliability. We adhere to strict mil-spec quality requirements and documentation in our quality management system, understanding that every component must meet the highest standards to ensure safety in the field.
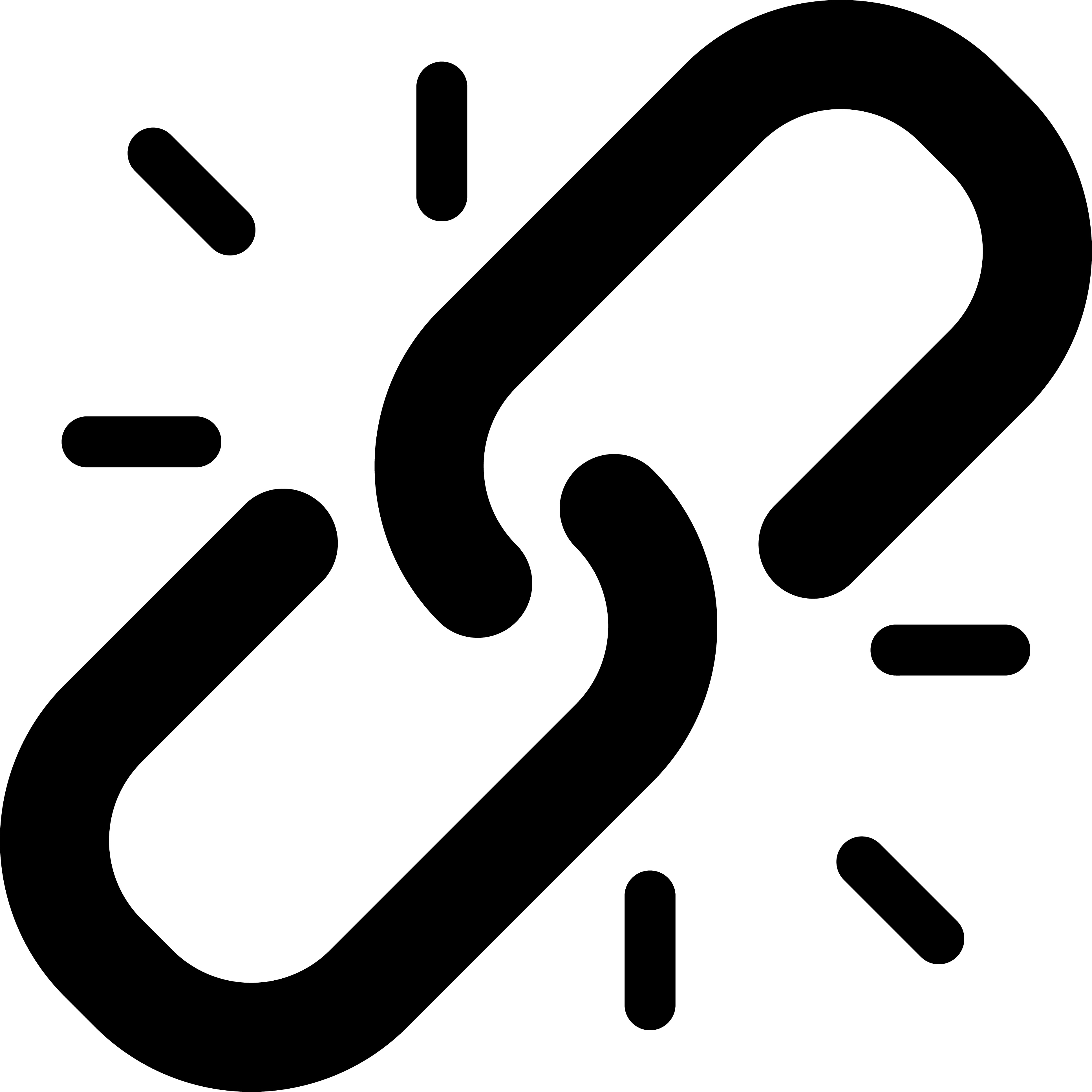
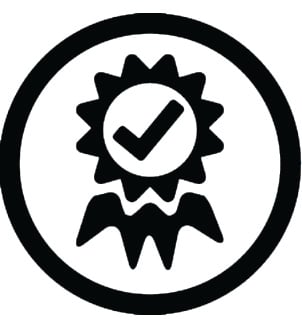
Why Choose Crescent?
Discover the countless benefits of partnering with us for all your injection molding manufacturing needs and let us show you why we are the perfect match for your business.