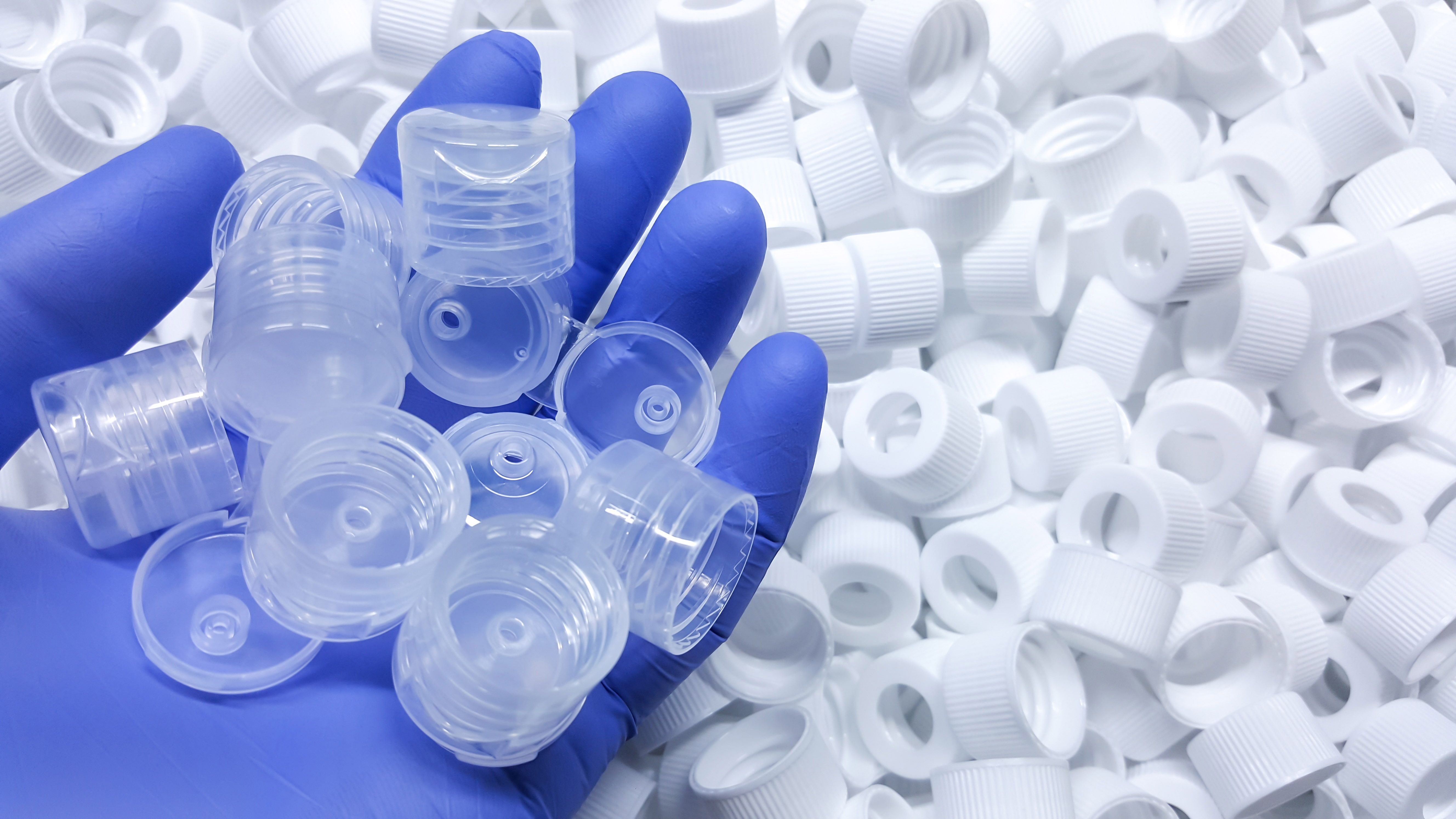
ABS Injection Molding: Benefits and Process
The types of plastic used to create components and products depend on its strength, heat resistance, flexibility, and other factors. ABS plastic is a versatile thermoplastic with various characteristics that make it ideal for many industries. That's why ABS is used for injection molding to create a wide range of products, from medical devices to industrial products.
What Is ABS? (Acrylonitrile Butadiene Styrene)
ABS — Acrylonitrile Butadiene Styrene — is a durable amorphous thermoplastic polymer known for its strength, impact resistance, and heat stability. It's made of three monomers:
- Acrylonitrile
- Butadiene
- Styrene
Each of these monomers contributes different attributes to the structure of ABS. Styrene provides a glossy finish in addition to its rigidity. Polybutadiene offers toughness and ductility—similar to malleability. Acrylonitrile makes it resistant to fatigue and chemicals.
ABS is created by polymerizing acrylonitrile and styrene in the presence of polybutadiene. The ratios of these three components can be varied. Typically, ABS contains at least 50% styrene. However, these ratios vary for different types of ABS to produce different grades. Each of these grades of ABS offers a unique set of properties tailored for specific applications, which include:
- Medium to high-impact properties
- Conductive properties
- Extrusion grade properties (strength and electrical insulation)
- Heat-resistant properties
- Flame-retardant properties
Overall, ABS plastic is generally known as a tough, chemical-resistant, and affordable plastic.
Key Benefits and Applications of Using ABS
When 3D printing first came out, it almost exclusively used ABS. It's still widely used in 3D printing because of its many benefits. These include:
- Dimensional stability: ABS plastics retain their shape and dimensions under varying environmental conditions
- Impact resistance: ABS has a high impact strength, so it can withstand shocks and physical stress without quickly buckling
- Heat resistance: ABS is a high-heat commodity resin. It has a head deflection temperature of 80 - 100 °C
- Chemical resistance: Depending on its particular grade, many types of ABS remain stable when exposed to a wide range of chemicals
- Overall strength: ABS's tensile strength — the maximum stress something can take before breaking or stretching — is 8 - 43 MPa, which makes it tough to break
- Ease of machinability: ABS is easy to cut, drill, and shape, facilitating efficient manufacturing processes
- Recyclability: ABS can be broken down and reprocessed into recycled material, contributing to waste reduction
Because of these attributes, ABS has a range of applications in many industries, including:
- Medical devices: ABS finds applications in making durable, chemical-resistant, and easily sterilizable components for the medical industry
- Consumer electronics: ABS makes casings and components for consumer electronics like TV sets, computers, and smartphones
- Industrial machinery components: ABS makes panels, covers, and guards on industrial machinery due to its durability and ease of maintenance
- Industrial pipes and fittings: ABS is popular for drain-waste vents because of its chemical resistance and sturdiness. Plus, it's commonly used in connectors, elbows, and joints for its long-term performance and resistance to corrosion
- Household appliances: ABS helps make vacuum cleaners, coffee makers, and other common household appliances that require durable and affordable plastic parts
- Defense components: ABS is used for the casings of radios and other communication equipment as well as parts of training simulators
The Injection Molding Process for ABS
The ABS injection molding process is a precise procedure that ensures consistent quality creation of parts and products. This involves paying close attention to injection pressure and temperature controls to guarantee optimal conditions for producing items with all the above-listed attributes and benefits.
Design Your Injection Mold for ABS
Understanding ABS properties is fundamental in the mold design process. The behavior of ABS under various conditions, including its reaction to heat, pressure, and cooling, plays a pivotal role in designing molds. Here are a few things to consider in the mold design process:
- Wall thickness
- Shrinkage rate
- Stress concentration
- Melt temperature
- Injection pressure
- Injection molding speed
- Cooling rate
Learning and mastering the critical factors of the injection molding process takes extensive time. Thus, professionals in injection mold building and injection molding can help develop the best process parameters to achieve a reliable and repeatable injection molding process.
Prepare ABS Material
As discussed above, ABS plastic comes in many different grades. Whether you need high impact resistance, heat resistance, reduced production costs, or advanced mechanical properties, choosing the suitable ABS grade is vital to creating a high-quality product successfully.
ABS plastic is hygroscopic, which means it can absorb moisture from the air. Excess moisture in ABS can lead to various issues during the molding process, including surface defects and reduced mechanical properties. To mitigate these issues, ABS is usually dried using industrial-grade dryers. The material is subjected to a specific temperature for a pre-determined amount of time to effectively reduce its moisture content without damaging its intrinsic properties.
Melt ABS Injection into the Mold
There are various considerations when melting and injecting ABS plastic into a mold. For instance, the melt temperature varies between 170 and 320 °C based on the ABS and mold temperature. The injection molding pressure also varies from 700 to 21800 psi. These are specific factors that your plastic injection molding professional will be familiar with when designing your mold.
However, there are three critical stages of the injection molding process: fill, pack, and hold.
- Fill stage:This is where the majority of your ABS material — about 95 - 98% — is injected into your mold
- Pack stage:This is the stage where pressure is adjusted to inject more ABS material into your mold to account for shrinkage and backflow
- Hold stage:This is the stage where your material is held at a fixed pressure until the cooling process begins
Solidify ABS and Ejecting the Part
To solidify the ABS in your mold, cooling channels are created in the mold design to ensure uniform cooling of molten ABS. Real-time temperature monitoring also helps ensure optimal conditions are consistently maintained throughout the cooling process. This is done to prevent defects and inconsistencies.
Once cooling is complete, ejection pins help to release the part from the mold smoothly. Post-ejection, each component undergoes a rigorous visual and dimensional inspection, ensuring adherence to specified tolerances and quality standards. Any excess material is trimmed, and additional finishing processes are applied as needed.
Partner With an Expert in All Thermoplastic Materials
Before you get a high-quality part or final product, a lot of expertise goes into choosing the right ABS material, designing a great mold, and following all the right injection molding procedures. That's why it helps to have experts on your side when creating an ABS injection molding product.
Crescent Industries has been helping the medical, defense, and industrial industries create high-quality plastic injection parts for decades. Discover how Crescent Industries can help fulfill your injection molding needs with ABS or almost any commodity or engineered resin grade.
Topics:
Related Articles
-
Mar 17, 2025
Advancements in Plastics Additives – What to Consider
Plastic additive technology has made some massive advancements over the past 10 years, but with all...
-
May 13, 2024
ABS Injection Molding: Benefits and Process
The types of plastic used to create components and products depend on its strength, heat...
-
Feb 20, 2024
What are Thermoplastic Elastomers?
Have you ever wondered about the versatile materials that seamlessly blend rubber's flexibility...