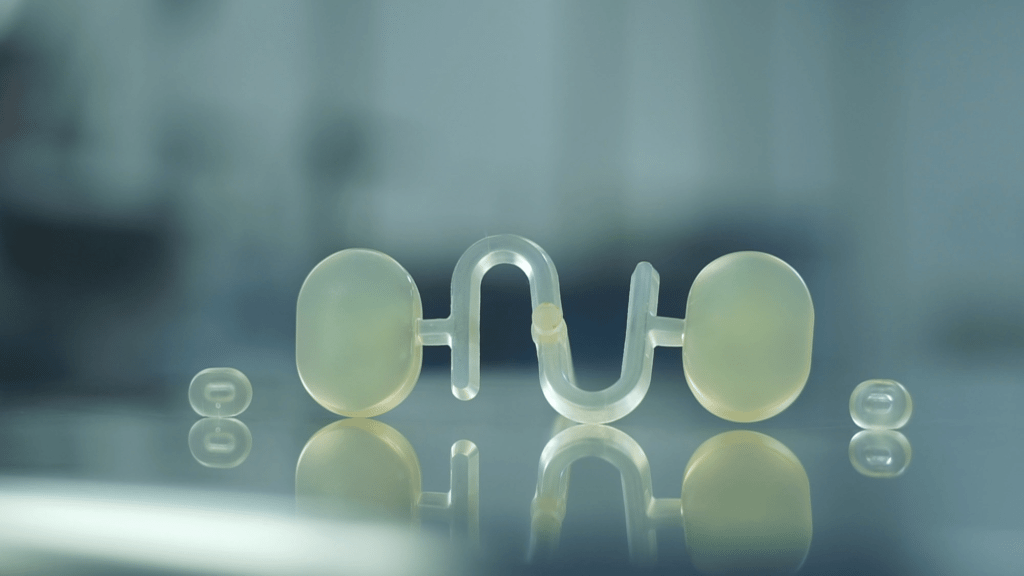
Different Types of Gates for Plastic Injection Molds
Gates play an important role in the quality of injection molded parts, as well as the efficiency with which parts can be molded. What is the function of gates in injection molding? Gates are the method through which the heated liquid plastic enters each mold cavity, after traveling through the mold runners. Depending on the part’s design, the mold construction may include multiple gates per cavity. There are also myriad varieties of gates in injection molding.
Below, we will explore these categories of gates.
How Gates are Determined for Plastic Injection Molds
First, let’s look at the factors to consider when a mold design selects a gate and location and the risks of choosing the wrong gate type:
- Part shape: Certain gate types are better suited for varying part shapes, such as flat geometries versus disks or cylindrical shapes.
- Automatic vs. manual trimming: Some gate types are more conducive to manual trimming, while other gate types will facilitate more efficient automatic trimming upon ejection.
- Number of cavities per mold: Single-cavity molds work better for certain gate types than multicavity molds.
- Part size: Different gate types are used to more easily fill larger mold cavities, while other types are more suitable for smaller sizes.
- Material: Depending on the cooling temperature and viscosity of the material in use, some gate types may be preferable over others.
Improper gate selection can lead to plastic overheating and burning via shear; can degrade or crack the plastic; can result in “short shot” part defects due to poor filling; and can lead to trimming errors and rework. Below, we will go more in-depth into how to choose the right gate to avoid these issues.
Gate Types for Injection Molds
Next, we will look at common gate designs, and will discuss how the factors above determine gate selection for the injection mold.
- Edge gate: Also referred to as “side gates,” these models are placed along the side or edge of a flat molded shape. Edge gates are among the most popular of all gate types. They include configurations such as fan gates and tab gates, which similarly feed into the edge of a part but are used for larger parts (in the case of fan gates) or thinner sections (in the case of tab gates). Edge gates are well-suited for general use, and are good for longer pack and hold times.
- Tunnel gate: Ideal for smaller parts and molds with many cavities, tunnel gates are used for automatic trimming due to their placement below the mold parting line. Since tunnel gates involve a small gate opening, they should not be used for larger parts.
- Cashew gate: Cashew gates are frequently used when maintaining a smooth, uniform surface finish is critical. Named for their unique shape, cashew gates arc around a part face to avoid visible surface scars. These types of gates are ideal for smaller parts, and are placed below the part line for automatic trimming.
- Sprue gate: Sprue gates are hand-operated, and thus are best for lower-volume, single-cavity molds. Sprue gates allow for uniform filling of larger parts, and are commonly used for cylindrical geometries.
- Pinpoint gate: Designed for smaller parts and multicavity molds, pinpoint gates leave almost no mark on the surface finish. They are used for applications where final appearance is important, or where finishing processes must be minimized. Diameters for these gates run between 0.5 millimeters and 2 millimeters.
- Hot runner valve gate: Used in hot runner systems (where the mold and the material in the runner do not cool, and the plastic remains in a liquid phase, thus greatly reducing waste). The hot runner valve gate type allows for maximum control over material flow, holding and packing — and can nearly eliminate the need for trimming and other finishing.
- Hot runner hot tip: Similar to the hot runner valve gate, the hot runner hot tip flows through the “nose” or tip of a cone or similarly shaped part. Like the valve gate, the hot runner allows for a high degree of control over material flow and cooling, and only leaves a small amount of excess material at the gate location.
At Crescent Industries, we offer expertise in mold design, gate selection and material selection. Our custom injection molding solutions are engineered to suit your needs across a wide range of industries. For more information, contact us today.
Resources:
https://www.basilius.com/blog/types-of-gating-for-injection-molding
https://www.plasticmold.net/plastic-injection-molding-gate-types/
https://nationalmolding.com/blog/the-most-popular-types-of-plastic-injection-molding-gates/
Topics:
Related Articles
-
May 12, 2025
The Role of Hot Runners in Injection Molding
Before the invention of hot runner systems, manufacturers used cold runner injection methods. These...
-
Apr 23, 2025
How Long Does an Injection Mold Last? | Durability Factors
Plastic injection molds can manufacture custom parts in numerous industries with great accuracy and...
-
Apr 10, 2025
How Are Injection Molds Made for Plastic Manufacturing?
Do you have a part design and need an injection mold built? Are you interested in finding a tooling...