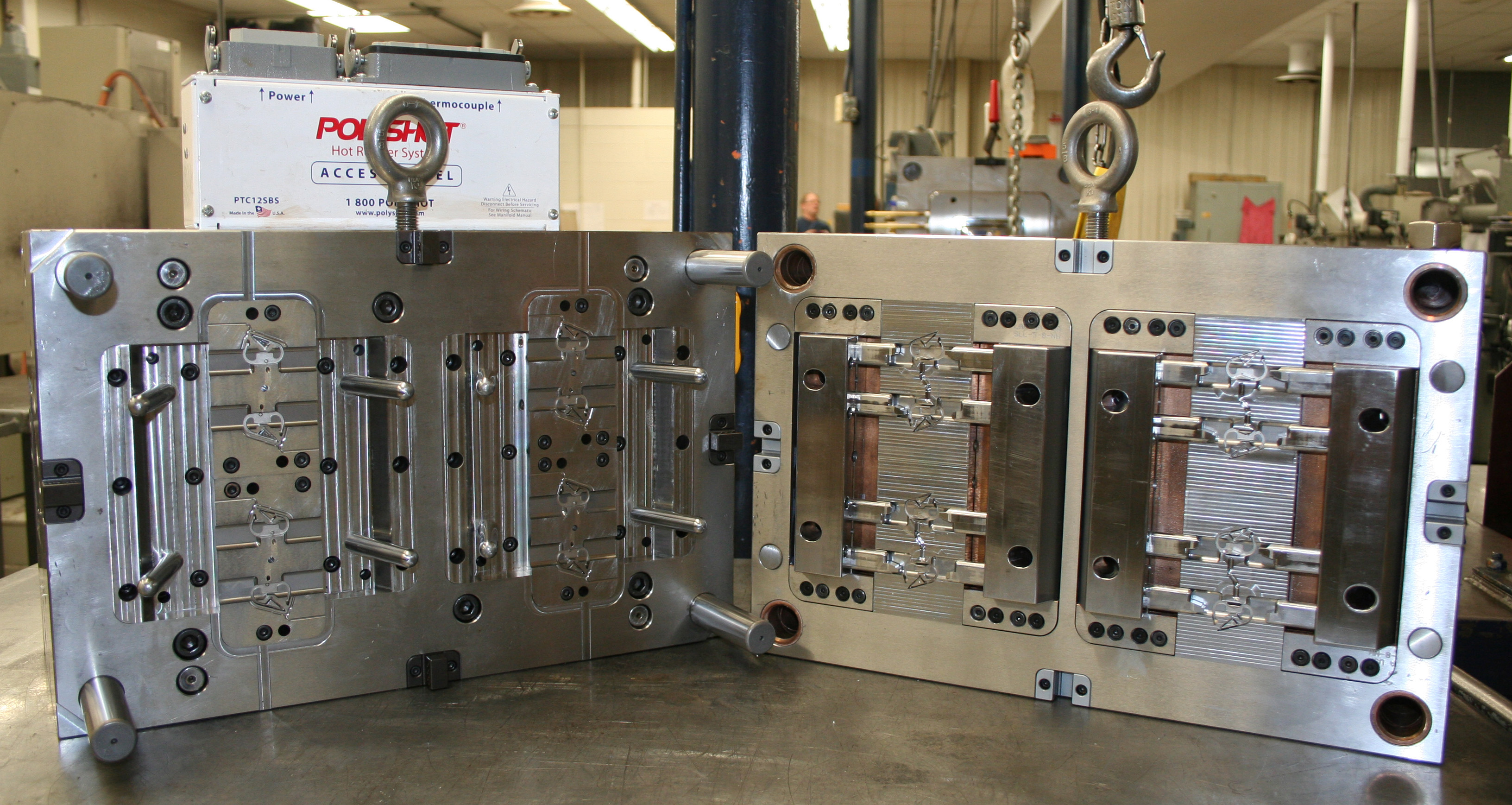
The Role of Hot Runners in Injection Molding
Before the invention of hot runner systems, manufacturers used cold runner injection methods. These systems use unheated plates to move molten thermoplastic through the system. The plastic in a cold runner system solidifies and must be removed from the plates and reprocessed.
Although the hot runner system was invented in 1963, it wasn’t until the mid-1980s that the process was streamlined in the evolving industry with more advanced technology. Since then, hot runner injection molding systems have been widely used due to their increased efficiency and precision capabilities.
What Is a Hot Runner System?
A hot runner injection molding system is a high-efficiency manufacturing process that works by keeping the plastic in a heated, molten state throughout the system. It delivers the plastic directly to the mold cavities without the need for repetitive cooling and reheating. A hot runner system allows for faster production of precision parts, such as those used in the medical, defense, and original equipment manufacturing (OEM) industries.
Benefits of Hot Runners in Enhancing Efficiency
While there are still some use cases where cold runner injection systems are preferred, hot runner systems are the better option when
manufacturers need high-volume injection molding with intricate parts.
Reduction of Material Waste
Hot runners use less material because they function without the need for cold plates, which convey the plastic through the system in a cold runner. These plates are attached to the finished product and must be removed from it at the end of the process. With a hot runner system, however, only the amount of plastic needed to
fill the cavity is used, so there’s no waste.At the end of the process in hot runner systems, there’s no need for wasteful post processing. The controlled flow in a hot runner system also makes filling the mold more accurate, eliminating waste associated with over or under filling. Because the process is more precise, fewer parts need to be discarded because of defects.
Faster Cycle Times and Improved Production Rates
In addition to using less material, hot runner injection molding systems are faster than cold runner systems. In a cold runner system, the plastic has to cool down in the runner before the molded material is ejected. This cooling slows down the process and adds to the cycle time.
In hot runners, only the pieces in the mold have to cool, reducing the cooling time and allowing for faster cycles and higher production rates. At the end of the process, the molded material doesn’t need additional trim work. Without this time-consuming step, manufacturers experience faster turnaround between production cycles.
Most hot runner systems require less maintenance in the form of cleaning and purging, which reduces downtime and interruptions. And because they support multi-cavity molds, manufacturers can produce more parts simultaneously, which can drastically increase production speed.
Lower Part Cost Over Time
Cold runner injection mold systems usually have lower initial mold costs. However, over time, hot runner systems cost less per part. You’ll pay less for materials because all your injected plastic will be used in part production.
Material savings can be a considerable factor, particularly when dealing with expensive, high-performance, or technical polymers. Additionally, with hot runner systems, you don’t have to pay for the extra steps involved in processing parts after ejection in cold runners.
Because of their increased efficiency, hot runners allow you to produce more parts in the same amount of time. Their consistent temperature also results in better energy efficiency, which contributes to a lower per-part cost in the long run.
How Hot Runner Systems Work in Injection Molding
The basic structure of a hot runner system includes a heated manifold and nozzles that keep thermoplastic material in a molten state as it flows into mold cavities. The injection molding machine uses temperature controllers to provide uniform material flow across cavities. The nozzles deliver the thermoplastic to the mold cavity, where it can cool before it’s ejected.
The two primary types of nozzles used in these systems are open-gate nozzles and valve-gate nozzles. Open-gate nozzles allow plastic to flow continuously into the mold cavity, while valve-gate nozzles control plastic flow with a pin or valve mechanism. Simple designs often work well with open-gate nozzles. If your design requires high precision, you may want to go for valve-gate nozzles.
Molten plastic is isolated in the system to keep it in a liquid form until it’s injected into the mold. This setup uses precise control to produce higher-quality parts at a faster rate than cold runners.
Is a Hot Runner System Right for Your Next Injection Molding Project?
When you’re considering whether to use a hot runner system for injection molding or a cold runner, you should consider several factors, including the following:
- High-volume production runs will be cheaper with an injection molding hot runner system over time. The lower long-term part price can make the initial investment worthwhile. For lower production runs, the cost may be too high.
- Part Complexity. Parts that are extremely intricate or require tight tolerances, such as medical devices, may need a hot runner system even for smaller volumes. These types of parts may be impossible to manufacture accurately using cold runner systems.
- Material Requirements. When you’re using expensive technical materials such as engineering-grade polymers, hot runner technology can save you money by eliminating material waste. However, if you need to use multiple materials, you may want to go with a cold runner system since frequently purging hot runner systems will add a significant cost factor.
- Other Priorities. While volume, part complexity, and material costs are the primary factors, you may also want to consider associated objectives, such as your budget and sustainability goals. Hot runner systems result in less waste, which can be important for companies prioritizing environmental sustainability. If you’re on a limited budget or producing an initial prototype, a cold runner system may be a better choice.
To learn more about hot runner system injection molding and discuss the needs of your next project, reach out to Crescent Industries today.
Topics:
Related Articles
-
May 12, 2025
The Role of Hot Runners in Injection Molding
Before the invention of hot runner systems, manufacturers used cold runner injection methods. These...
-
Apr 23, 2025
How Long Does an Injection Mold Last? | Durability Factors
Plastic injection molds can manufacture custom parts in numerous industries with great accuracy and...
-
Apr 10, 2025
How Are Injection Molds Made for Plastic Manufacturing?
Do you have a part design and need an injection mold built? Are you interested in finding a tooling...