everything you need to know about Medical Device Contract Manufacturing
Explore the complete process—from design and compliance to scalable production—for Class I, II, and III medical devices.
Do you have a design for a new medical device? Do you have a new or updated product design and need manufacturing support?
If so, you may appreciate medical device contract manufacturing. It can help you get your device created and assist you in handling the regulatory challenges that can come with producing medical devices for sale in the United States.
Review this guide to learn more about manufacturing your plastic components or medical devices.⬇️
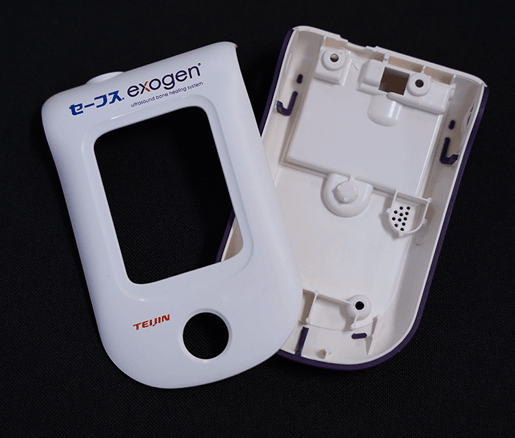
What is Medical Device Contract Manufacturing?
Medical device contract manufacturing refers to the system by which a company makes medical devices or components that can be sold by another company at a later date. At its core, this process is simply the outsourced fabrication of medical devices that are designed and produced for the medical market.
The reason OEMs like medical device contract manufacturing is because they can utilize their partners to efficiently make products. They may have more than one contracted partner, and each may produce a different medical device and/or components.
The scope of medical device contract manufacturing can be wide, but some of the basic, consistent parts of this kind of manufacturing include:
- Designing the process used to manufacture the product
- Other post-processing operations like parts decorating, assembly, packaging, and more
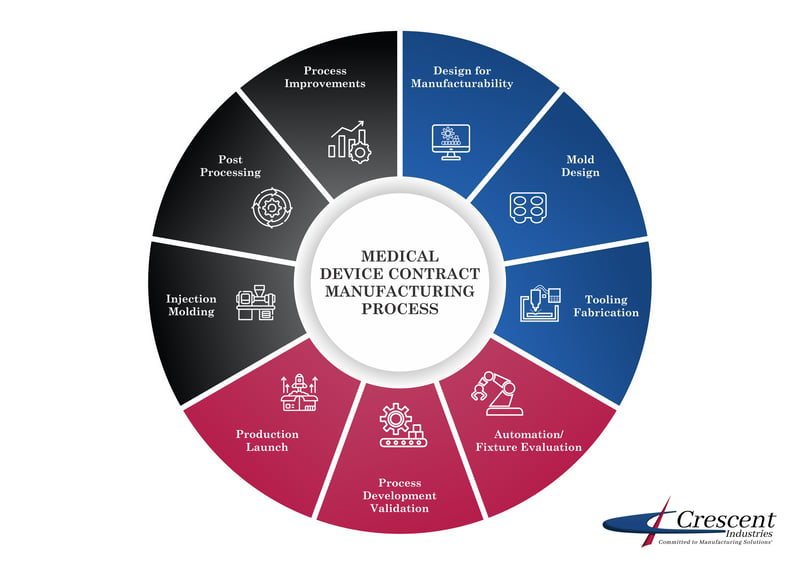
Additional services may also be added depending on the manufacturer and contract.
In What Ways Can Medical Device Contract Manufacturing Be Better for Businesses?
Medical device manufacturing can be an excellent choice because there is the potential to minimize manufacturing issues. The lean method of medical device contract manufacturing is beneficial because it aims to eliminate waste and to improve efficiency and quality.
Your company may appreciate that you can have a faster turnaround time and shorter wait before your product makes it into the hands of end-users when you choose contract manufacturing.
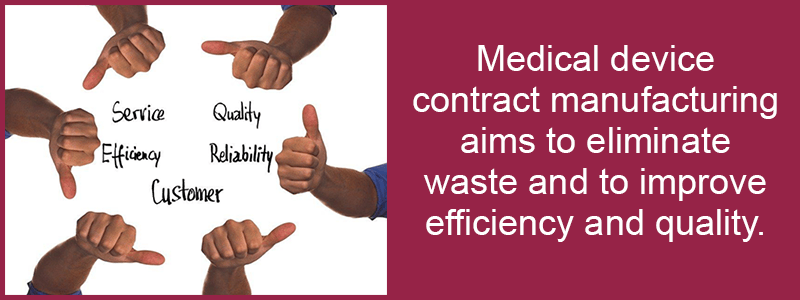
What are the FDA Medical Device Classifications?
The definition of a medical device is highly specific. The U.S. Food and Drug Administration (FDA) sets criteria that define what a medical device is. Specifically, the FDA states that a product is a medical device if the apparatus, instrument, machine, contrivance, implant, implement, in vitro reagent, or other item or article, part, or accessory is:
- Recognized by the United States Pharmacopoeia, official National Formulary, or a supplement of them
- Intended to affect the function or structure of the body of a man or animal when that structure can't achieve its primary purpose through chemical actions
- Intended to be used in the diagnosis of a medical condition or disease
- Intended to be used to mitigate, treat, cure, or prevent a disease or illness of a man or animal
- Does not achieve its purpose through chemical action on or within the body of a man or animal and isn't reliant on being metabolized
- Not software functions, which are excluded from this definition
It is important to note that the industry is highly regulated. Different sectors may need support with varied regulations depending on where they fall in the FDA's three-tier classification system. Quality controls, approvals, and registrations also vary based on how the medical devices are rated by the classification system.
The FDA's Medical Device Classifications
The U.S. Food and Drug Administration has three established classification tiers for around 1,700 generic types of devices. The administration places those into different medical specialties (16 are currently available). These specialties are known as "panels."
The three classes can be broken down into the following controls.
-
Class I General Controls with or without exemptions
-
Class II General Controls/Special Controls with or without exemptions
-
Class III General Controls and Premarket Approval
Depending on the classification your device falls into, you could see differences in your premarketing submission or application requirements and what it takes to get your product cleared to go to market. Class I controls are generally for the lowest risk applications, while Class III controls are for products that pose a greater risk to patients or users.
For marketing a Class I or II medical device that is not exempt, you will need to file a 510(k), which our medical device contract manufacturing company is capable of providing manufacturing documentation.
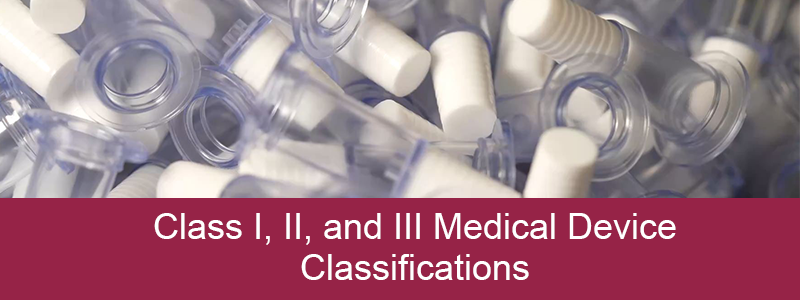
Services Medical Device Contract Manufacturers Provide for Plastic Parts & Devices
With medical device contract manufacturing, you are outsourcing a single part of a product or an entire product to a manufacturing company of your choice. This is common in the medical device industry.
It is common for the medical device contract manufacturer to provide services such as:
- Evaluations of the parts or design for manufacturability
- Tooling
- Process and product validation
- Automation/Quality inspection
- Post-processing
- Process improvement identification
The relationship with a medical device contract manufacturing company should be synergistic. Your goal should be to provide clear order expectations while also listening to what the manufacturer knows is realistic for your product based on data, years of experience, and skill.
If the company cannot handle all aspects of the medical device's build, they are not a full-service contract manufacturing company. While it is possible to work with multiple companies, doing so will slow down the production of the end product. Additionally, there is a greater risk of errors or defects when working with multiple manufacturers.
For those reasons, many business owners and product designers decide to work with a single contract manufacturer from the design phase all the way through assembling the final product.
Design for Manufacturing (DFM)
One thing that a medical device contract manufacturer and injection molder can help with is design for manufacturability. This is a process of designing and engineering your product to reduce how much it costs to create. With DFM, any issues with the product design may be addressed in the design phase, making it more affordable.
Design for manufacturability takes control over costs by considering how a product could be best created through manufacturing techniques. DFM goes over different approaches for manufacturing products, determining which would be the best in terms of cost and time savings.
A good DFM process will come up with the easiest method of producing the parts needed based on the manufacturing technology available.
Engineering Support
A good medical device contract manufacturer will offer engineering support. This means that they’ll have staff that is concerned with technical support and equipment support.
Engineering support can include several kinds of support such as DFM and plastics selection support. Engineers who are acutely aware of the costs of these processes as well as the best methods of creating certain parts may be able to help your company save time and money as they suggest the best routes to create your design.
If your design needs to be re-engineered, they may also be able to help you with this and even reduce the number of parts needed to minimize retooling.
Injection Mold Design
Injection mold design is a high-precision process. During this process, molten plastic will be poured into a mold designed to make a part of your product. The plastic cools in that mold. Once it hardens, the product or part is ready to be used.
Each mold design has to have a gate, which is an opening that allows the molten plastic to be injected into the mold. Where that gate is may influence the appearance of the part. It may also influence the part’s dimensions or if any warping will occur.
Mold Fabrication
Injection molding is an excellent, cost-effective manner of creating plastic parts en masse, but you first have to have a mold to use. Mold fabrication is the process of creating the mold that will be used to create the pieces of your design. Many times, these molds are designed and printed in 3D, though there are other methods of creating them.
Full Production Using Automation
Saving time, making more precise movements, and gaining better operational efficiency is possible with automation. Full production using automation doesn’t require human involvement in all aspects of the operation or production of a design or its parts. With this process, mechanical and automated systems independently handle production. This removes the potential for many human errors, but it does still require management and oversight to be effective.
Post-Processing
Following the completion of a part, post-processing improves the piece to be ready for the end-use. Corrective actions can be taken at this stage, allowing any surface defects to be removed. This is also the stage when functional or decorative changes can be made with secondary processes.
How Long Will It Take a Product to Go to Market?
If you have a medical device design, it may make your life easier to take it to market with the help of medical device contract manufacturing outsourcing. It would be common for medical device companies to outsource to several vendors to get a product ready. This resulted in a much longer wait before a product could be tested or taken to market due to having more complex logistics and multiple locations for manufacturing, assembly, packaging, and sterilization.
Some companies have been created to become one-stop shops for medical device outsourcing with the goal of handling all parts of the process under one roof. These companies provide the necessary capabilities in one location, which can then reduce the time it takes to bring a new medical device to market or to make it ready for testing and approval by the FDA.
Quality Systems & Regulatory Compliance for Medical Devices
Quality is of the utmost importance to those working in the medical device contract manufacturing sphere. There is a quality assurance process that all manufacturers should follow. There are also agency regulations that need to be kept in mind at all times.
Some of the critical items that the quality assurance process has to monitor include:
- Maintaining quality
- Maintaining the cost of production
- Verifying that all internal standards are met
- Ensuring patient safety
You need to be sure that these quality assurances are in place. Remember, a medical device contract manufacturer does need to use ISO 13845 certification protocols.
On top of quality assurances, you want to have good quality controls. Quality control failures could lead to product defects and recalls that have the potential to damage your business in the future. Recalls in particular are commonly used as the basis for lawsuits, so it's crucial to be meticulous about quality control to minimize the chances of a recall.
What Sets Quality Control Apart from Quality Assurance?
Quality control and quality assurance both are part of the quality management system, but they have two different jobs. Quality control refers to finding flaws in your products before they're sent out to distributors. Quality control tests are a normal part of medical device manufacturing and attempt to find defective products or batches before they have the potential to cause problems.
Quality assurance looks at how to prevent flaws in the manufacturing process. The staff at the manufacturing facility will take steps to keep the quality assurance controls in place throughout the production of a product so that each one comes out identical. If there are any problems with nonconforming products throughout the process, the problems causing the defects will be addressed before additional devices will be made.
You should also know that quality control doesn't happen until after the product is produced. This is different from quality assurance, as quality assurance is handled throughout the lifecycle of your product.
If you have questions, talk with the medical device contract manufacturing company that you're interested in working with. They should be able to give you a detailed answer about their current quality assurance process and the quality controls that they implement to keep your product in line with the FDA's manufacturing requirements.
A contract manufacturer will not help your business register with the FDA or medical listing, but provide the manufacturing validation support documents needed for your FDA approval. They can help you manufacture the product to your high specifications.
What can an injection molding manufacturer do for you? They can help you create the design you’re looking for and provide you with the support that is needed to come up with the end product that you were hoping to design. From the initial design for manufacturability through the post-processing stage, a medical device contract manufacturer will handle every part of the process to make sure your final parts or pieces are created to the highest standard.
Choosing the Right Manufacturing Partner
One of the major benefits of medical device contract manufacturing is that you are in greater control of who works with your product design and creates the device from start to finish. There are some questions to ask to make sure that products are made by the right manufacturer. These include the following:
- What is their current production capacity, and can it be expanded in the case that the product is highly successful?
- What is the cost to produce each unit, and does it decrease with larger orders?
- How do they assure that the quality of the product remains high across multiple orders or batches?
- What is the expected turnaround time for the units and how long will delivery take to the end-user?
These are among the most common questions asked of medical device contract manufacturing companies.
Are You Looking for a Company to Help with Medical Device Contract Manufacturer?
If you are looking for a company to manufacture a new medical product, think about the company as a long-term partner. You may want to choose a company familiar with specific processes, such as medical molding, or look for an ISO 13845 contract manufacturer specifically for your product. No matter what kind of company you select, you should choose the one that will help you meet the FDA's requirements and get your product to market within budget and on time while maintaining the efficacy and safety of the item. Read this Case Study.