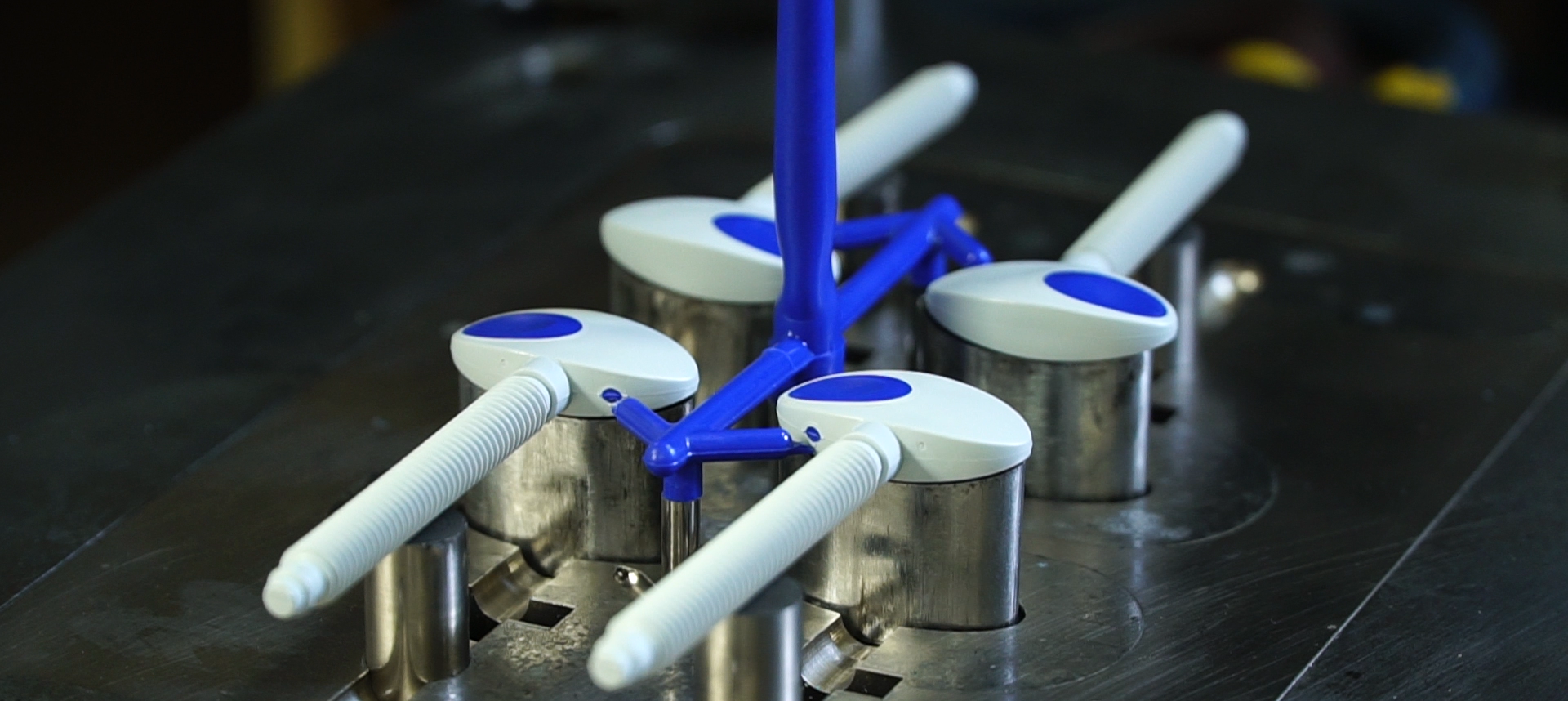
How Medical Overmolding Enhances Devices: Key Benefits and Applications
The number of medical devices hitting the market is constantly rising to meet the healthcare industry’s growing demand. As a result, medical OEMs are under pressure to develop complex yet functional devices within a limited timeframe. This may leave you wondering how durable, effective, and user-friendly products are achieved.
Overmolding, a specialized injection molding technique available at Crescent Industries, can help fulfill the unique needs of the medical industry. But what is overmolding, and how can you transform your medical appliances with the technology? Here’s an extensive guide covering the working principle of medical overmolding, its benefits, and its uses.
How Medical Overmolding Works
Overmolding is a variation of conventional plastic injection molding where we partially or fully immerse and mold components over another. Instead of manufacturing two products separately, we are creating a single, integrated product. An example of such a device is a plastic surgical instrument with a rubber grip. There are two main components of the medical overmolding process:
- The substrate, a base material that we mold first to form the foundation or core of the final medical product.
- The secondary material or overmold, which comprises a soft and flexible thermoplastic elastomer that we inject over the substrate.
Overmolding medical devices is achievable through insert molding and two-shot molding. They both follow a complex sequence that requires careful preparation, accuracy, and expertise. These steps are:
Material Selection
Choosing the right raw materials for custom medical device overmolding ensures compatibility. The overmold and substrate material must have compatible physical, thermal, and chemical properties.
There are two main material combinations. They include the plastic-over-metal substrate with a higher compatibility rate than plastic-over-plastic substrates. Common overmolded materials for the substrate include:
- Acrylonitrile butadiene styrene (ABS), a tough resin with excellent resistance to acids, oils, heat, and alkalis.
- Polyethylene (PE), a plastic comprising ethylene monomer units with different arrangements that give rise to low-density, high-density, and ultrahigh molecular weight plastics.
- Polypropylene (PP), a polymer with a methyl group in the place of an ethylene monomer that makes it harder than PE.
- Polyether ether ketone (PEEK), a high-performance material that offers resilience to stretching, stress, chemical corrosion, and high temperature.
- Others include polymethyl methacrylate (PMMA), polycarbonate (PC), and polyoxymethylene (POM)
The material for the overmold is soft and flexible. Some examples are
- Thermoplastic polyurethane (TPE), a plastic renowned for its toughness, biocompatibility, and flexibility.
- Thermoplastic elastomers (TPUs), polymers with similar elasticity to rubber. They are easy to color and offer consistent performance.
Mold Design
We require two molds to produce the substrate and the overmolded part, as they comprise different materials. There are multiple factors and features to consider when designing these molds to ensure proper bonding between the materials. One consideration is the inclusion of vents and gates that ensure the uniform distribution of molten resin. Another factor is ensuring the mold can accommodate the material’s inherent traits, such as shrinkage during cooling and varying solidification rates.
Substrate Injection MOLDING
At this stage, we introduce the solid substrate resin into the injection molding machine and melt it under intense heat. The machine then injects the molten resin into the mold cavity. We carefully monitor the injection phase for uniform filling of the mold cavities. This helps maintain the structural integrity and dimensional accuracy of the substrate parts.
Overmolding
After creating the substrate, we can introduce the overmold. This step entails adding the second material, melting it, and injecting it into the mold over the substrate. Once the overmold solidifies, it forms a secure bond with the substrate. The mold has cooling channels that prevent deformation or premature separation during the cooling process. After achieving adequate bonding, we carefully eject the final product from the mold.
Key Benefits of Medical Overmolding
Medical device overmolding has improved the healthcare industry. Medical practitioners can perform more effectively through this injection molding process, enhancing patient outcomes. Notable benefits of overmolding include:
Enhanced Device Durability
Overmolding helps create sturdy medical products with excellent impact, pressure, abrasion, and chemical-resistant. This improved durability allows the consumer to enjoy functional use for an extended duration.
Better Ergonomics and User Comfort
Medical device overmolding is exceptionally effective at enhancing user comfort. The process allows us to incorporate soft overmolded materials on hard surfaces, providing a cushioned grip. The enhanced ergonomics enable the prolonged, comfortable use of surgical tools and wearable medical equipment.
Applications of Medical Overmolding in Healthcare
Overmolding has numerous uses in the medical industry, including these products:
Surgical Instruments
Surgical tools require a perfect balance between rigidity and ergonomics to ensure precision and comfort during handling. Overmolding helps create instruments with a solid core for strength and an outer ergonomic layer. This design reduces the surgeon’s fatigue or discomfort during long procedures while improving control for better patient outcomes.
Diagnostic Devices
Overmolding enables the production of functional and user-friendly handheld diagnostic devices, such as blood glucose monitors and thermometers. This encourages safe and regular use by caregivers. Overmolded materials are also easy to clean, aiding proper sanitation.
Implantable Medical Devices
Overmolding also helps create biocompatible and durable medical device implants. The medical-grade resins we use to mold orthopedic implants elicit minimal reaction from the immune system. They also offer excellent strength and flexibility to keep up with the body’s dynamic movement and load bearing.
Transform Your Medical Devices With Overmolding Technology
Overmolding offers unmatched versatility to the healthcare industry. Whether you need durable, biocompatible, flexible, or ergonomic devices, Crescent Industries' team of professionals can help you create them with this manufacturing process. Contact us today to unlock the full medical applications of the overmolding process.
👉Check out Crescent's Overmolding Capabilities!
Topics:
Related Articles
-
Jun 30, 2025
How Medical Overmolding Enhances Devices: Key Benefits and Applications
The number of medical devices hitting the market is constantly rising to meet the healthcare...
-
Dec 10, 2024
Injection Molding Burn Marks: Causes and How To Avoid Them
The injection molding process can be complicated. If you rush your project or do not pay close...
-
Apr 02, 2024
An Expert's Approach to Injection Molding Process Development
Are you curious about the innovation behind your flawlessly molded plastic products? Welcome to the...