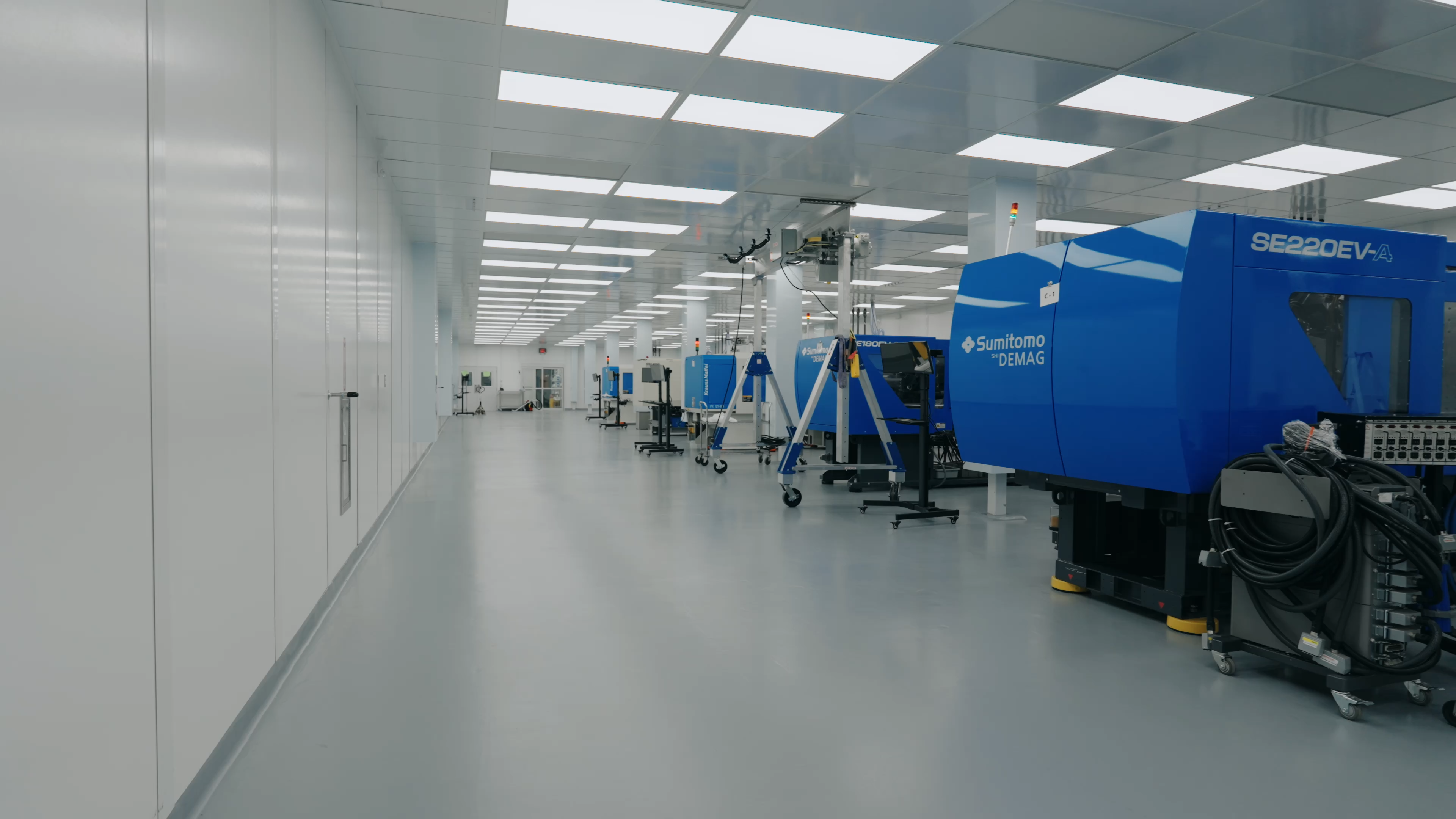
The Key Benefits of ISO 7 Cleanroom Standards for Injection Molding
The International Organization for Standardization (ISO) sets strict standards for the safety and quality of plastic injection molded products. Becoming ISO certified is a way for consumers, clients, and business partners to trust that a company’s product runs are up to standard, no matter where in the world the company operates.
There are 10 types of ISO standards, ranging from general organizational quality management systems to data and information security management systems. For plastic molding operations, ISO 7 Cleanroom Standards, also known as the Class 10K Cleanroom Particle Count Classification, are an important benchmark for ensuring top quality products.
ISO 7 Cleanroom Standards 101
The ISO Cleanroom Standards describe the allowed total amount of airborne particles permissible in a given volume of space. The ISO 7 standard allows a maximum of 10,000 particles per cubic foot of interior air, with a minimum of 60 HEPA air exchanges per hour.
It’s often used in plastic extrusion and molding for biotechnology, pharmaceuticals, and medical devices. This level of cleanliness ensures minimal contamination during the manufacturing and packaging stages, without sacrificing faster cycle times.
The Importance of Cleanroom Standards in Injection Molding
Cleanliness is particularly important during the manufacturing process of plastic injection molding. That's because even small levels of contamination can negatively impact the quality of the final product.
For plastic molds and slow-curing resin, air-born particles can get mixed in with the material, resulting in impurities or pores that could harbor future contamination and cause color staining or bacterial growth.
The level of cleanliness needed for a product depends primarily on the manufacturing process and the served industry. Injection molding facilities that adhere to the Class 7 Cleanroom Standards minimize the risks of airborne pollutants settling into the molded material during curing times.
The standard your process will follow depends on injection speeds, required plastic pressures, and the resistance of your injection molding plastic type to impurities. These factors may also affect the surface finish of the plastic parts during the manufacturing process.
ISO 7 Specifications and Requirements
Meeting ISO 7 standards requires a manufacturing facility to adhere to specific guidelines for air quality and composition. The Class 8 standard determines the allowed concentration of particles depending on their size:
- Particles larger than 5 µm are limited to 2,930 per m3
- Particles larger than 1 µm are limited to per 83,200 m3
- Particles larger than 0.5 µm are limited to per 352,000 m3
There are no restrictions on particles larger than 0.3 µm in the Class 7 standards.
Other environmental parameters, including lighting levels, noise, humidity static, and temperature, are case-specific and depend on the manufacturing process in question. However, they should be maintained at constant rates that ensure the optimum material production and worker conditions.
Benefits of ISO 7 Cleanrooms in Injection Molding
ISO 7 cleanroom for plastic injection molding offers numerous benefits for industries such as biotechnology, pharmaceuticals, and medical devices. These controlled environments help ensure enhanced product quality and reliability, compliance with industry regulations, and a reduction in contamination risks. By maintaining strict standards for air quality and composition, ISO 7 cleanrooms play a crucial role in producing high-quality, uncontaminated plastic parts for various critical applications.
Enhanced Product Quality and Reliability
Working under controlled conditions and standardizing the configurations of injection molding machines ensures the replicability of results when manufacturing large quantities. Manufacturers can optimize their production processes for efficiency and quality without worrying about variants such as seasonal temperature drops, humidity, or dust, which can interact with the resin polymers during the injection process.
Class 8 cleanrooms also ensure the plastic injection molded parts aren’t contaminated with embedded particles during the molding process. This is particularly important for the manufacturing of medical and pharmaceutical devices, where the environment must be sterile.
Compliance with Industry Regulations
Highly sensitive industries, such as pharmaceuticals, dental, defense, and industrial parts manufacturing, tend to be much more limited by local regulations in the quality of parts they can use. Cleanroom standards are often required by law for the production of plastic parts in these industries, in order to reduce the risk of machinery failure or unhygienic equipment.
For example, the Pharmaceutical Inspection Co-Operation Scheme (PIC/S) states that cleanrooms are mandatory for the manufacturing of sterile medical devices. It also requires a minimal number of personnel to have access to any cleanroom molding facilities for parts used in healthcare.
Reduction in Contamination Risks
Plastic part contamination ranges in severity depending on the pollutants involved and the target industry.
For example, microscopic metal shards from other manufacturing processes can make their way into plastic that is meant to be fully non-magnetic, non-abrasive, and non-conductive, which would increase the risk of injury.
For manufacturing dental and pharmaceutical parts using injection molding equipment, high temperatures, and moisture can influence the safety of the material and whether they can be used with patients.
Choose a High-Quality Injection Molding Partner
When outsourcing the manufacturing of your plastic parts, it’s important to work with a trustworthy and reliable injection molding partner. ISO certifications, such as Class 7 cleanroom standards, can help you determine manufacturers that prioritize quality in manufacturing and deliver reliable results.
Crescent Industries is a USA-based and employee-owned plastic injection molding company offering ISO 7 cleanroom injection molding solutions. We have options for all your custom-molded component needs, putting our engineering specialties towards quality production of injection molds over a comprehensive range of industrial and commodity-grade resins.
Get in touch to learn more about how we can help your business with injection molding plastic.
Topics:
Related Articles
-
Mar 17, 2025
Labware & Diagnostic Injection Mold Building and Molding
Medical device molding requires much higher levels of precision injection molding and tolerance...
-
Jan 10, 2025
Benefits of a Plastic Medical Device Manufacturer
Reusable and single-use plastic medical devices are held to high standards of sanitation, texture,...
-
Jun 07, 2024
The Key Benefits of ISO 7 Cleanroom Standards for Injection Molding
The International Organization for Standardization (ISO) sets strict standards for the safety and...